-
Sustainability at Fujitsu Group
- Sustainability Management in the Fujitsu Group
- GRB(Global Responsible Business)Goals and Achievments for FY2022
- GRB(Global Responsible Business)Goals for FY2025
- Fujitsu's accessibility
- Stakeholder Engagement
- United Nations Global Compact
- SDG-related Activities in Fujitsu
- External Recognition and Awards
-
Global Responsible Business
- Environment
-
- Environmental Management
- The Fujitsu Group Environmental Vision on Climate Change
- Living in Harmony with Nature (Conservation of Biodiversity)
- Environmental Action Plan
- Environmental Data
- Environmental Communication
- Environmental Social Activities
- Disposal and Recycling of ICT products
- Environmental Considerations in ICT Products
- Governance
-
Data and Documents
- Fujitsu Group Sustainability Data Book 2024
- Social, Governance and Environmental data
- Independent Assurance Report
- GRI Standards / United Nations Global Compact (UNGC) principles Comparison Table
- SASB Standards Comparison Table
- Sustainability Information Disclosure Framework
- Link to regions responsible business reports
- Contact
- Sitemap
Response to Environmental Risks
Environmental Risk Management Structure
The Fujitsu Group built and operates a group-wide risk management system to identify, prevent, and mitigate a variety of potential risks, or prevent their recurrence, including issues related to climate change and environmental pollution. In addition to the Risk Management & Compliance Committee, which reports directly to the Board of Directors, and Risk Management & Compliance Officers at each Fujitsu division and Group company in Japan and overseas, we have regional Risk Management & Compliance Committees, to build a structure where these organizations cooperate with each other to promote risk management and compliance throughout the Fujitsu Group, both in terms of preventing potential risks and responding to risks that have emerged. The Committee identifies, analyzes, and assesses key risks associated with the business activities of each Fujitsu division and Group company in Japan and overseas (focusing on 33 risks considered to be important to the Group), and formulates and reviews the countermeasures for these risks after confirming the status of countermeasures for avoiding, mitigating, transferring, or retaining them. The Committee makes regular reports to the Board of Directors about key risks that have been identified, analyzed and assessed, using methods such as the creation of visualized rankings and maps which take the degree of impact and likelihood of occurrence into account. In addition, we have put response processes into place in the event that risks become tangible, despite the implementation of various measures. Each division and Group company will immediately report to the Risk Management & Compliance Committee about any key risks that become tangible, such as natural disasters, accidents, product accidents or failures, system or service problems, compliance violations such as fraud, information security incidents, or environmental problems.
We also leverage the group’s Environmental Management System (EMS), which is based on ISO14001, for minimizing risks to the environment through continuous improvements.
Efforts to Minimize Risks to the Environment
Dealing with Risks Related to Climate Change
There is a possibility of significant impacts on our business continuity from increases in the frequency and effects of natural disasters as a result of recent climate changes. For that reason, we have formulated a business continuity plan and are devoting effort to continually revising and improving the plan.
In addition to risks such as implementation of stricter regulations for greenhouse gas emissions and a carbon tax, there is demand from customers and society for contribution to carbon neutral. This creates a risk of increasing the energy cost incurred by the Fujitsu Group, as well as the cost required to comply with regulations related to measures for reducing greenhouse gas emissions. Additionally, if climate change countermeasures are insufficient, there is a risk of harm to our corporate reputation or a disadvantage at bidding.
In order to minimize these risks, we are conducting short-term, medium-term and long-term risk analysis/response within our company-wide risk management structure. As the trend toward carbon neutrality in the global community as a measure against climate change, we have obtained net-zero target certification from the Science Based Targets initiative (SBTi). We will further raise the 1.5°C level we acquired in fiscal 2021 and aim for net-zero by FY 2040.
In accordance with the recommendations issued by the Task Force on Climate-Related Financial Disclosures (TCFD) in 2017, the Fujitsu Group analyzes and discloses risks associated with climate change that may have an impact on its business and financial strategies. Refer to the table below for the major potential risks and responses currently identified.
Risks Associated with the Transition to a Low Carbon Economy, and Our Response to Them
Policy/Legal Risks | ● Risks: Increase in cost in order to respond to the strengthened laws and regulations on greenhouse gas emissions and energy use (such as a carbon tax), and diminished corporate value in the event of a violation.
○ Response: Complete compliance with laws and regulations through EMS. Continual reduction of the amount of GHG emissions through steady implementation of Science Based Targets and the Environmental Action Plan. |
---|---|
Technology Risks | ● Risk: Unrecovered investments and market share decline in the event that the company lags behind in a fierce competition in technological developments toward a carbon-free society (such as energy-saving performance and low-carbon services).
○ Response: Enhance development of energy-efficient products and energy-efficient enabling technologies, solutions, and services through steady implementation of Science Based Targets and our Environmental Action Plan. |
Market Risks | ● Risk: Losing business opportunities if products, solutions, and services do not meet energy-saving performance needs.
○ Response: Enhance development of energy-efficient products and energy-efficient enabling technologies, solutions, and services through steady implementation of Science Based Targets and our Environmental Action Plans. |
Risks to Reputation | ● Risk: Decreased corporate value and increased response costs associated with a negative stakeholder perceptions of the status of implementation of climate change mitigation efforts (e.g., improving renewable energy adoption rates).
○ Response: Enhance measures to counteract climate change and promote reduction of environmental footprint through steady achievement of the group's Science Based Targets and Environmental Action Plan. |
Climate Change Related Risks in the Supply Chain, and Our Response to Them
Upstream Supply Chain | ● Risk: A temporary suspension of the suppliers' business activities due to the occurrence of severe natural disasters such as large-scale floods, sudden heavy downpours, and lightning strikes, which affects the procurement of materials.
○ Response: Conduct surveys of the business continuity capabilities of suppliers and procure materials from multiple sources, as well as implement other measures. |
---|---|
Downstream Supply Chain | ● Risk: Losing business opportunities due to the inability to obtain environmental labelling, which is a green procurement requirement of customers.
○ Response: Conduct trend surveys and risk assessments of the environmental labelling scheme. Develop and provide top-level energy-efficient products through steady implementation of Science Based Targets and our Environmental Action Plan. |
Assessing and Monitoring of Potential Water Risks
In recent years, due to a tight demand-supply situation in many areas around the world because of water damage—such as flooding—and droughts that are caused by a variety of factors, including population growth and climate change, there is a growing concern that this issue may become a business risk. The Fujitsu Group conducts assessments of and monitors potential water risks for direct operations sites and supply chains.
Specifically, while using tools and databases provided by NGOs and national and local governments, we identify water stress conditions and natural disaster risks in regions where our business sites are located in accordance with RCP 4.5 (intermediate stabilization scenario) from among the emissions scenarios defined by the Intergovernmental Panel on Climate Change (IPCC). We then comprehensively assess the water risk at each site by analyzing how important water use is in the business activities of each operations base, and we confirm the level of compliance in a variety of activities such as the reduction of water intake, measures to reduce pollution in wastewater, business continuity management (BCM) systems, and others. For the supply chain, we also assess our suppliers' flood preparedness and other water risks based on the supply chain BCM surveys, field surveys conducted according to the Responsible Business Alliance's (RBA) code of conduct and the CDP Supply Chain Program. As a result, we have confirmed that there are no significant risks that could substantially affect our business activities.
Physical Climate Risk Adaptation
Fujitsu have risk assessment systems that include Physical Climate risk in place in Japan, Oceania, Europe and cross regional department Global Delivery.
As physical risk is different based on the location, adaption is tailored to that specific location and risk, for example.
Fujitsu Australia and New Zealand has identified the main physical climate risks to our business in the region, which include short term weather events e.g. extreme heat, flooding, storm events, as well as long-term climatic impacts e.g. drought.
Key measures undertaken in Australia and New Zealand to adapt to climate risks have included:
- Extreme heat events
- Processes to ensure built-in redundancy of critical equipment and reliable operation of uninterruptable power sources in the event of grid-scale outages.
- Ensuring equipment is designed to tolerate extreme temperatures.
- Installing temporary cooling equipment (e.g. misting) to reduce ambient temperatures.
- Bushfire
- Updating site-based procedures to assess business critical activities and evaluate which activities can be performed remotely in the short term.
- Turning off external air intakes to offices and data centers to limit smoke ingress.
- Drought
- Deployment and maintenance of rainwater storage tanks at some sites.
- Use of recycled water where possible.
- Installing real-time water loggers at all data centers to monitor consumption trends and help inform water usage efficiency projects.
- Other
- Climate risk (e.g. extreme heat modelling) incorporated into assessment of siting of new data centers
Within Europe the climate risk is different to Oceania and a number of measures to adapt to climate change risk have been undertaken at a cost of over £1million in one London location showing the seriousness that we consider Climate impact and the commitment that we take protecting our continued service.
- Installing the infrastructure to enable the local water authority pumping equipment to use our data centers Uninterruptable Power Supply (UPS) in the event of a flood
- Dredging the local lagoon to help it act as a water sink
Other examples of adaption based on Physical climate risk in specific locations
- Philippines, the Business Continuity Planning includes natural disaster events such a typhoons and monsoons and other extreme weather events
- Malaysia – Natural Disaster Prevention guidelines provides emergency contact details and advice for employees with their safety prevalent
Another example off adaption is the modernisation and cocreation of the Flood Warning System (working with the UK Environment Agency). A system that can issue flood warnings to citizens within 20 minutes. The flood warning service hosts more than 1.5 million registered properties, 2.9 million telephone numbers, 180,000 email addresses and 1.5 million registrations for mobile text alerts. Since its launch the flood warning system has sent more than 7 million messages across email, text, telephone and social media.
*Co-creating a flood warning system to alert citizens faster
https://designinaction.global.fujitsu.com/reimagining-the-dynamics-of-success-and-resilience/co-creation-in-action/environment-agency
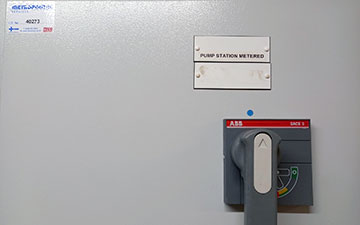
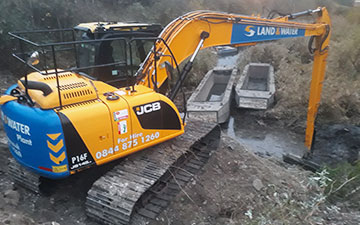
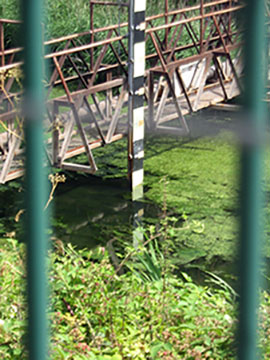
Flooding Damage Impact Assessments Through Hazard Maps and Measures Against Flooding
Fujitsu and its domestic Group companies conduct impact assessments of flooding damage according to a rainfall scale with two types, depending on the magnitude of the impact on our business, as follows. We identify and assign rankings to business sites which will be highly impacted. If a business site falls under a level 4 impact ranking, we implement various measures.
[Assessment 1 Planned scale (Rainfall on a scale that occurs about once every 10-100 years)]
- Assessment subjects: 169 sites for Fujitsu, 280 sites for Group companies All owned properties and major leased properties (such as sales offices and data centers) in the Fujitsu Group
- Assessment method: We assess whether or not the site falls within the "estimated flood inundation area (planned scale)" for nearby rivers as established by the Ministry of Land, Infrastructure, Transport and Tourism or the prefectural government, as well as the extent of the impact within and outside the site and the impact of flooding on buildings.
We rank sites that were assessed as being impacted by flooding on a scale of 1 (minor impact) to 4 (major impact).
[Assessment 2 Assumed maximum scale (Rainfall on a scale that occurs about once every 1000 years)]
- Assessment subjects: Domestic data centers and business sites that will be heavily impacted by flooding (such as Fujitsu Solution Square (SS) and the Kawasaki factory)
- Assessment method: We conduct reassessments by upgrading the criteria to "estimated flood inundation area (assumed maximum scale)," and rank the sites on a four-point scale.
[Results for Assessment 1 and Assessment 2 *Only sites with an impact rank of 4 are shown below.]
Sites | Assessment 1
(Assessment on a planned scale) | Assessment 2
(Assessment on an assumed maximum scale) | Final impact | |
---|---|---|---|---|
Fujitsu | Fujitsu SS | Impact rank 4 | Impact rank 4 | Impact rank 4 |
Fujitsu | Kawasaki factory | No impact | Impact rank 4 | Impact rank 4 |
Group companies | No sites which fall under impact rank 4 |
[Major Measures]
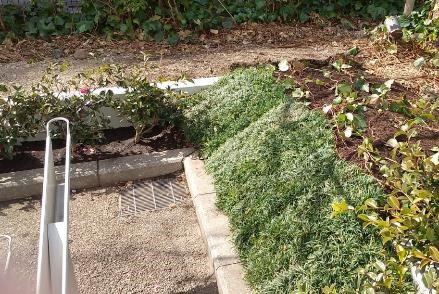
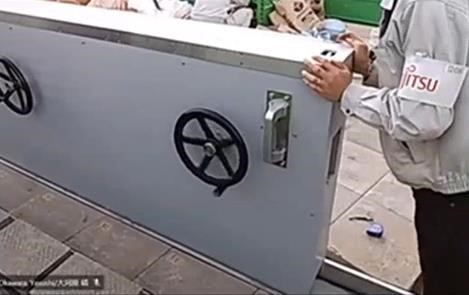
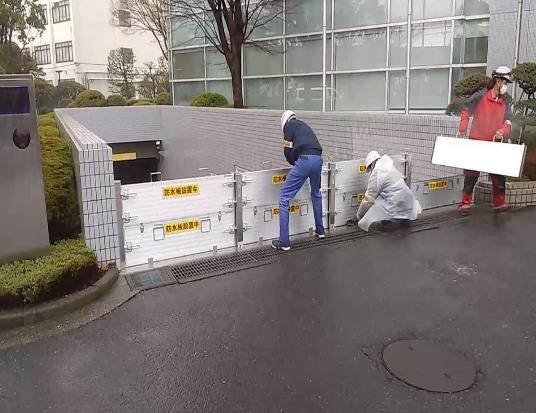
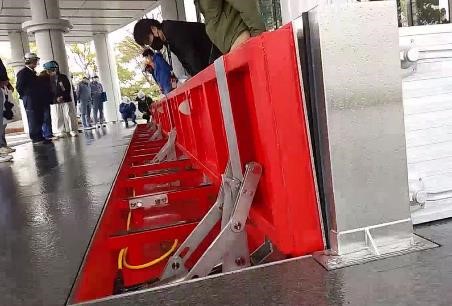
Preventing Water Pollution
In order to preserve the water quality of surrounding waterways, including rivers, groundwater and sewers, we have set voluntary controls that are even tougher than legal mandates, and conduct measurement and monitoring on a regular basis. We recover and recycle chemicals used in production processes, instead of discharging them into wastewater. We are also working to properly manage and reduce discharge of harmful substances and pollutants by ensuring appropriate chemical use, preventing chemical leaks and penetration, and properly managing the operations of water treatment and purification facilities, among other measures.
Preventing Air Pollution
We have set voluntary control values that are more stringent than legally mandated emissions standards in order to prevent air pollution and limit acid rain. Regular measurement and monitoring are conducted based on these controls. Efforts are also made to appropriately process dust and soot, sulfur oxide, nitrogen oxide, and other harmful substances, and reduce emissions through measures including combustion management at facilities that produce soot and smoke, use of fuels with low sulfur content, and managing the operations of exhaust gas processing equipment. Furthermore, we have installed activated carbon adsorption treatment equipment and are reducing our atmospheric emissions of organic solvent vapors containing substances like VOCs. Moreover, with the enactment in April 2015 of the Act on Rational Use and Proper Management of Fluorocarbons, we have set in-house stipulations and striven for proper management of specified products (commercial refrigerators and air conditioners containing fluorocarbon refrigerants) while working to identify the volume of our fluorocarbon leakage.
In addition, emission of dioxins has been prevented by suspending use of all in-house incineration facilities as of January 2000.
Preventing Destruction of the Ozone Layer
Since fluorocarbons not only destroy the ozone layer but also cause global warming, we have totally eliminated the use of ozone-depleting substances in manufacturing processes (parts cleaning and solvents) by introducing precision water cleaning systems and no-clean soldering technology. On the other hand, with regard to fluorocarbons for refrigerants used in air conditioning facilities (freezers, etc.), we are switching to non-fluorocarbons when equipment is renewed, and are working to appropriately manage and dispose of Class I specified products in accordance with the Fluorocarbons Emission Control Act.
In addition, the annual confirmation of the amount of leakage in the calculation of fluorocarbons indicates that it is less than 1,000 t-CO2 (not subject to reporting to the minister in charge) for FY2023.
Results for complete elimination of ozone-depleting substances | |
---|---|
Ozone-depleting substances | Time of complete elimination |
Washing chlorofluorocarbons (CFC-113, CFC-115) | End of 1992 |
Carbon tetrachloride | End of 1992 |
1,1,1-trichloroethane | End of October 1994 |
Alternative chlorofluorocarbons (HCFCs) | End of March 1999 |
Preventing Pollution of Soil and Groundwater
We have established rules for soil and groundwater surveys, measures and disclosures. We review these in accordance with changes in the law and social circumstances and respond based on these rules. We systematically examine soil and groundwater, based on the rules, and if pollution is confirmed, we carry out cleanup and countermeasures at each plant according to the situation, while working together with government authorities to disclose information.
As of FY2023, there are four business sites where soil and groundwater pollution from prior business activities have been confirmed. At those business sites, we have installed observation wells to observe effects outside the site due to groundwater pollution, while also working on purification measures through water-pumping aeration, etc.
Monitor Imoact of Groundwater Pollution on Areas Outside of Premises*
※Monitor impact of groundwater pollution on area outside of premises, which is the greatest risk of soil / groundwater water pollution
Business Sites Where Soil or Groundwater Contamination Has Been Found
Site Name | Location | Cleanup and Measure Execution Status | Maximum Value Found at Observation Well (mg/L) | Regulated Level
(mg/L) | |
---|---|---|---|---|---|
Substance | Measured Value | ||||
Kawasaki Plant | Kawasaki City, Kanagawa Prefecture | We are continuing to clean up VOCs by pumping and aeration. | 1, 2-dichloroethylene | 1.7 | 0.04 |
Chloroethylene | 9.4 | 0.002 | |||
Oyama Plant | Oyama City, Tochigi Prefecture | We are continuing to clean up VOCs by pumping and aeration. | Trichloroethylene | 0.54 | 0.01 |
1, 2-dichloroethylene | 3.8 | 0.04 | |||
Chloroethylene | 1.8 | 0.002 | |||
Nagano Plant | Nagano City, Nagano Prefecture | We are continuing to clean up VOCs by pumping and aeration. | Chloroethylene | 0.022 | 0.002 |
FDK Washizu Plant | Kosai City, Shizuoka Prefecture | We are continuing to clean up VOCs by pumping and aeration. | Tetrachloroethylene | 0.071 | 0.01 |
Trichloroethylene | 0.15 | 0.01 | |||
1, 2-dichloroethylene | 0.16 | 0.04 | |||
Chloroethylene | 0.0039 | 0.002 |
Chemical Substance Control
To prevent pollution of the natural environment or damage to health due to the use of harmful chemical substances, we are controlling the use of some 1,300 substances using our original Chemical Information System called "FACE" and working to appropriately control and reduce emissions at our business sites.
With regard to chemical substances included in products, we have determined banned substances according to regulations in Japan and worldwide and are working to thoroughly control them, not only inside the Group but also with business partners who deliver materials and products to us.
Appropriately Processing Waste
In accordance with the Act on Waste Management and Public Cleansing, we appropriately store and manage waste generated from our business sites, select waste disposal companies that can properly dispose of waste, and outsource disposal. Also, we regularly carry out on-site audits in order to confirm that subcontractors are appropriately handling the waste processing tasks we entrust to them. As part of our efforts to reduce waste, we are promoting the reuse of certain plastic trays in cooperation with a vendor that is working to reuse plastic trays and convert them into recyclable materials.
Environmental Liabilities
In properly assessing the Fujitsu Group’s expected future environmental liabilities, and communicating our integrity and corporate stance of not deferring our liabilities, we have recorded liabilities of 2.50 billion yen in soil pollution cleanup costs, high-level polychlorinated biphenyl (PCB) waste disposal costs, and asbestos processing costs during facilities demolition, which is the amount we calculate, as of the end of FY2023, to be necessary for the Fujitsu Group to conduct these tasks domestically in the next fiscal year and beyond.
Conserving Biodiversity
In recent years, risks involving the natural environment have been recognized as serious global risks. This necessitates the disclosure of relevant information disclosure by companies, and toward this end, the Task Force on Nature-related Financial Disclosures (TNFD) is considering an information disclosure framework.
If the Fujitsu Group fails to appropriately respond to information disclosure in accordance with the TNFD, its corporate reputation may decline and its ability to procure funds may be affected. Going forward, we will provide disclosures in line with the TNFD framework.