- Fujitsu Manufacturing Solutions
- Offerings
- Production Preparation Sophistication Offering
- Upgradation of cost and production Offering
- Solutions
- Fujitsu Application for SAP® Solutions
- Production Planning
Fujitsu Application for SAP® Solutions Detail Scheduling Template - Build-to-order manufacturing
Fujitsu Application for SAP® Solutions Mass Customization Template - Actual Cost
Fujitsu Application for SAP® Solutions Actual Costs Template - SAP S/4HANA® Manufacturing for Production Engineering and Operations (SAP PEO)
- SAP® Digital Manufacturing (SAP DM)
- SAP® Integrated Business Planning (SAP IBP)
- SAP® Portfolio and Project Management (SAP PPM)
- Case study
- SAP S/4HANA® Manufacturing for Production Engineering and Operations (SAP PEO)
- Kawasaki Heavy Industries, Ltd.
- Kawasaki Heavy Industries, Ltd. (Fujitsu Uvance)
- Kawasaki Heavy Industries, Ltd. (SAP Website)
- SAP® Digital Manufacturing (SAP DM)
- Anaplan
- Fujitsu Supply Chain Planning Solutions
(Old name: FUJITSU Enterprise Application GLOVIA smart PROFOURS
FUJITSU Manufacturing Industry Solution COLMINA scheduler / PSI)
- FUJITSU DIE-TECH CORPORATION OF THE PHILIPPINES Innovative Case Study Report on Production Planning Operations in the Global Supply Chain GLOVIA smart PROFOURS (PDF)
- Successful application of "PROFOURS" in FUJITSU DIE-TECH CORPORATION OF THE PHILIPPINES (YouTube)
- Tohshin Seiki Co.,Ltd. (PDF)
- RISU PACK CO., LTD. (PDF)
- GOLD PAK CO., LTD. (PDF)
- Fujitsu Limited (PDF)
- Fujitsu Supply Chain Planning Solutions
- Fujitsu ERP Solutions for Process
(Old name: FUJITSU Enterprise Application GLOVIA ProcessC1)
- TOAGOSEI CO., LTD. (PDF)
- ASAHI BREWERIES, LTD. (PDF)
- NIHON NOHYAKU CO.,LTD. (PDF)
- Nippon Light Metal Company, Ltd. (PDF)
- ADEKA Corporation (PDF)
- Showa Denko K.K. (PDF)
- Fujitsu Digital Manufacturing FJVPS
- Fujitsu ERP Solutions for Process
- Catalog
- List of introductory materials on Planning Sophistication Offering
- Supply Chain Planning Solutions for Profit Maximizing S & OP Processes
SAP® Integrated Business Planning (SAP IBP) - Integrated Production Planning Solution for Supply Chain DX
GLOVIA smart PROFOURS
- List of introductory materials on Manufacturing execution management sophistication Offering
- List of introductory materials on Upgradation of cost and production Offering
- List of introductory materials on Upgradation of cost Offering
- For SAP deployment users
Cost / Profit and loss management solutions
Fujitsu Application for SAP® Solutions Actual Costs Template
- List of introductory materials on Upgradation of production Offering
- Fujitsu best add-in solution for flexible use of SAP
Fujitsu Application for SAP® Solutions Mass Customization Template - An ERP solution for Assembly Manufacturers Realize Mass Customization through Product Configuration Management
Fujitsu Application for SAP® Solutions Mass Customization Template (SIEMENS) - Provided by Fujitsu SAP Engineering Manufacturing Execution Solution
SAP S/4HANA® Manufacturing for Production Engineering and Operations (SAP PEO) - Solutions to manage all multiple parallel planning, development, and investment projects
SAP® Portfolio and Project Management (SAP PPM) - Fujitsu’s SAP Manufacturing Solutions
- Video (YouTube)
- List of videos (YouTube) related to Planning Sophistication Offering
- Successful application of "PROFOURS" in FUJITSU DIE-TECH CORPORATION OF THE PHILIPPINES
- Fujitsu Manufacturing DX journey to the best
- An Integrated Planning and Management Solution “PROFOURS” : A reliable field partner
- GLOVIA smart PROFOURS - Integrated production planning system for improving work efficiency
- Production Scheduling Software " Fujitsu Enterprise Application GLOVIA smart PROFOURS"
- List of videos (YouTube) related to Upgradation of cost and production Offering
- Fujitsu Manufacturing DX journey to the best
- Fujitsu Application for SAP Solutions makes mass customization for manufacturing possible
- Fujitsu Application for SAP® Solutions Mass Customization Template
~Product Concept Version~ - Fujitsu Application for SAP® Solutions Mass Customization Template
~Quotation Version~ - Fujitsu Application for SAP® Solutions Mass Customization Template
~Order Navigator Version~ - Introduction Fujitsu Manufacturing Industry Services
- Fujitsu Transforming the future of manufacturing
- List of videos (YouTube) related to Manufacturing execution management sophistication Offering
- Fujitsu Manufacturing DX journey to the best
- How to keep manufacturing operations compliant
- Smart Manufacturing Customer References with COLMINA and SAP Offerings ”Collaboration with SEMENS”
- FNC uses Fujitsu SAP to build the factory of the future
- Reimagine your business with Fujitsu and SAP : KAWASAKI case study
- Transform your manufacturing to next generation with Fujitsu SAP Industry 4.0
- SAP® Manufacturing Integration and Intelligence (SAP MII) Solution proposed by FUJITSU
- Events and Seminars
Iida Industry Co., Ltd.
Overcome DX implementation challenges with teamwork and a passion to improve
Iida Industry Co., Ltd. develops, manufactures, and sells sound insulators, dampers, and sealants for the automobile, architecture, and railway sectors and introduced Fujitsu's COLMINA MES in 2018. In this interview, Naoki Yoshida of Fujitsu, who supported the introduction, and Fujitsu's Senior Evangelist Koji Takeda sat down with Iida Industry President Kosuke Iida and three employees Shinya Mizutani and Ken Nakagawa, Production Management Division, and Kota Aoyama, Management Planning Division, to hear the thoughts of front-line workers.
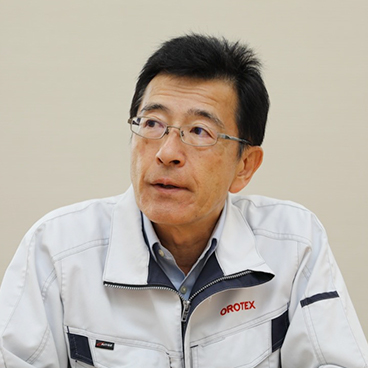
Business performance will never improve without trying something new. We are constantly aware that something new must be done in product development.
Kosuke Iida of Iida Industry, President
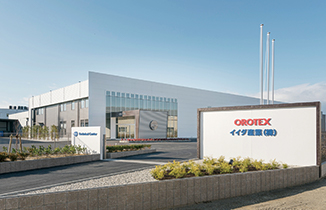
0
Number of delayed shipments
160
Monthly work reduction time
- Industry: Automobile manufacturing industry
- Country: Aichi, Japan
- Customer's website
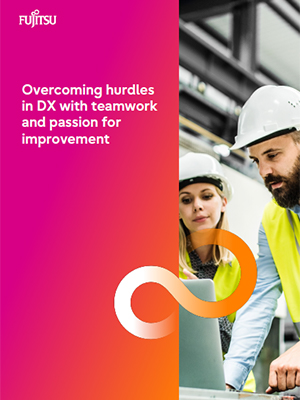
Contents
- No Company Can Survive without Introducing Something New
- An Open Corporate Culture Is a Major Foundation for Introducing DX
- DX Introduction, Starting Small with Domestic and Overseas Plants
- Project Team’s Willingness to Learn Thaws Resistance to DX
- Realizing New Work Styles After Introducing DX
- The Passion to Improve Is Essential for Eradicating Resistance to New Things
No Company Can Survive without Introducing Something New
For this interview, we visited Iida Industry, located in Inazawa, Aichi. The company has not only Factory No. 1 but also three other factories and a technical center in the city. First, we talked with President Kosuke Iida, who decided to move forward with DX, about the factors leading to the introduction of COLMINA MES, the company's attitudes toward new technology, and future prospects.
Takeda: May I ask you the reasons and thoughts that led you to introduce DX?
Iida: We must have been driven by our challenging attitude of always trying something new. We are increasingly forced to cut the prices of conventional products, and competition is also becoming fiercer. Business performance will never improve without trying something new. We are constantly aware that something new must be done in product development. This time, it was system implementation. Our implementation staff came up with many ideas on what to do specifically.
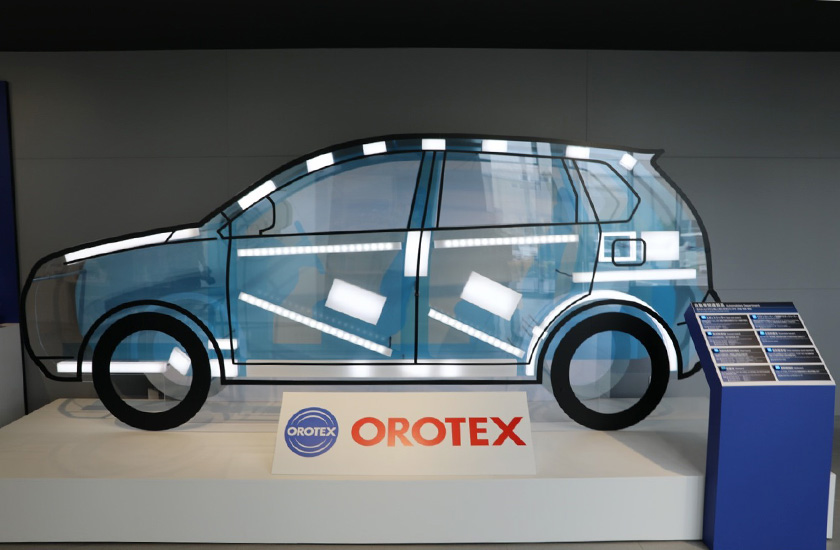
Takeda: Regarding DX, many people say it should be introduced only by large companies, and some often say there is no goal in sight or it is difficult to make a budget for it. What did you think about these points?
Iida: For details, it may be better to ask the three in charge you will talk to later. Of course, I was not too familiar with DX and don't give the okay to everything. It is true that the deadline was unclear and the budget was hard to allocate. The purpose of DX introduction was not to improve our business performance but to reduce our internal costs, so I thought DX should be done regardless of the size of the company. Competitors must also be working on DX. This transformation was required for us to create a competitive advantage and keep up with the times.
Takeda: Are you trying to actively use something new other than DX?
Iida: For DX, we launched a project team. We already had a system team, so I left everything to them, including the budget. Of course, I am studying myself. I participated in seminars and exhibitions to learn new things, and I always keep myself interested. For example, I am now learning about ChatGPT. But, whether to introduce new things to our company is another matter. I am curious but also cautious so I listen to the experiences my friends and fellow executives have had using things and research reputations myself before determining whether to adopt them.
Takeda: How did you build a corporate culture of developing a strong relationship of trust between the president and employees?
Iida: Our corporate philosophy and code of conduct are "Be honest, be sensitive, and be positive." I often tell employees to have something they can engage themselves in more than work. I've done aikido and Shorinji Kempo for a long time. They are both about avoiding force and letting it pass skillfully, rather than meeting force with force. This concept or view of these sports also helps me in business. People understand various ways of thinking and control others with different ways of thinking. Devotion to things other than work inspires you to develop such ideas in work.
Takeda: What are your future plans as a manufacturing company?
Iida: We would like to further grow the sales of our automobile business and further expand our building material business, hopefully as the second pillar. As vehicles become autonomous, there will be more need for our sound insulators and dampers because electric vehicles make sounds that are barely noticeable above the engine sounds more conspicuous. This could be a business opportunity for us. About 30 years ago, our clients often asked, "Can you make a product like this?" but today, we have to explore new products ourselves. Under such circumstances, we collect various essences, set up a hypothesis, perform assembly and embodiment, and give feedback. We have no choice but to keep always searching blindly for answers in a crude and honest manner.
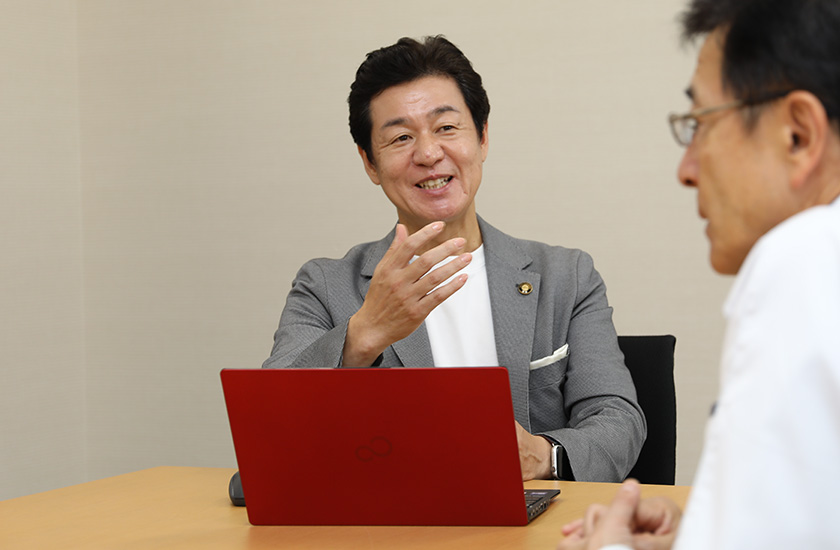
An Open Corporate Culture Is a Major Foundation for Introducing DX
Next, we interviewed Shinya Mizutani and Ken Nakagawa, Production Management Division, and Kota Aoyama, Management Planning Division, all of who operated the system on the front lines when DX was introduced in 2018, about the company's strengths, what they learned, and what they struggled with when introducing DX.
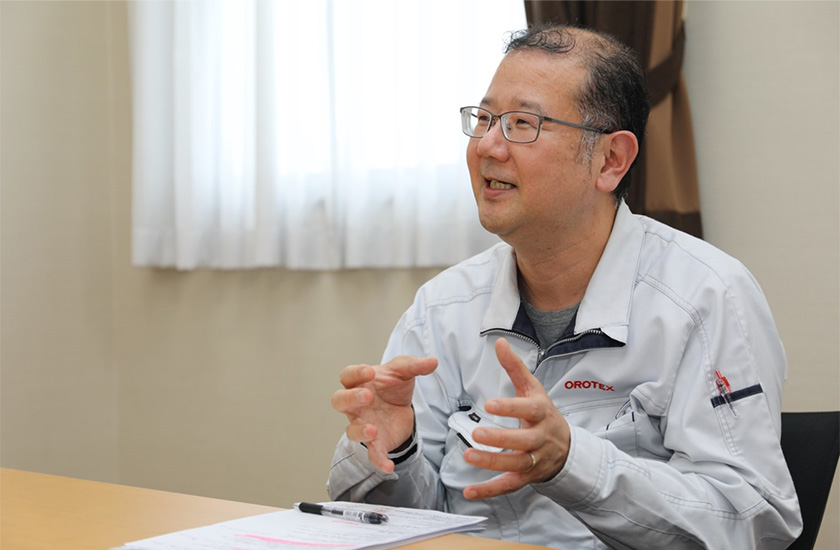
Takeda: Let me ask the three of you on the front lines for more details about the DX introduction. I hear that you mostly manage production and introduce systems. What do you place importance on when you work?
Mizutani: I am in charge of production management and value the so-called "QCD" the most. I always make sure to keep on top of management, particularly in order not to miss deadlines for clients.
Nakagawa: In addition to QCD, I keep in mind time reduction. I am also thinking about how to reduce the workforce while working.
Aoyama: I am responsible for the company's system, so I focus on keeping it running, having a system backup available, and restoring it as soon as possible even if it goes down.
Takeda: Do you think you have successfully put QCD into practice, including meeting deadlines?
Mizutani & Nakagawa: We think we have. (laugh)
Aoyama: I am just the opposite. I think we still have a long way to go.
Takeda: What do you think about the strengths of your company as front-line workers?
Mizutani: We are in the manufacturing industry but good at adapting quickly. For example, in case of cars, if unexpected issues arise, we can redesign and remanufacture cars immediately.
Nakagawa: Our company has a homey atmosphere where employees can easily express themselves, which allows quick and flexible responses, as Mizutani said.
Aoyama: Our company listens carefully to even employees who are not directly involved in products, like me. We are given the power to exercise discretion or approval and work very closely with our president. This comfortable working environment is one of our strengths, I think.
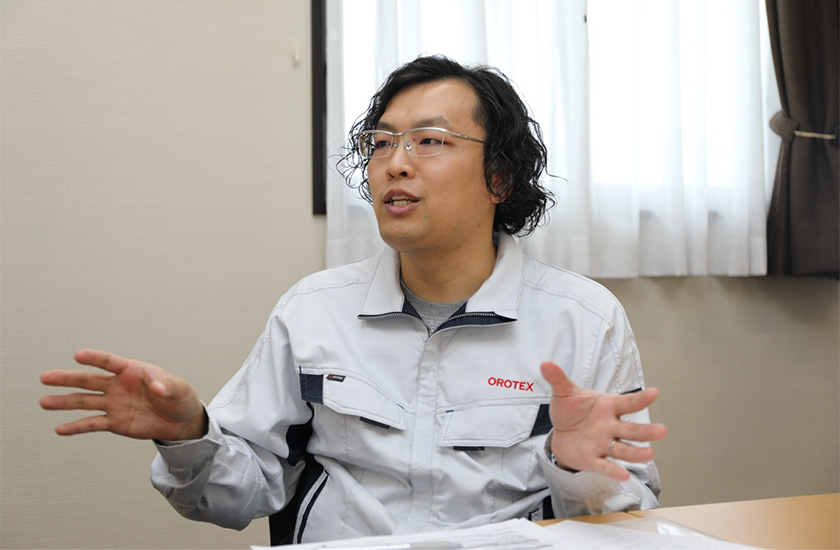
DX Introduction, Starting Small with Domestic and Overseas Plants
Takeda: Let's change the subject to the MES implementation. What made you decide to introduce a DX system?
Mizutani: We already had talked about introducing a system in Japan and in our subsidiary in Thailand almost at the same time since around 2016. The system would be for material receiving and product shipment where goods are incoming. We introduced a warehousing system in Thailand in 2017 and saw the effects. However, applying the system implemented in Thailand to Japan would not be that simple. Things were more complicated In Japan with more materials and products to handle than in Thailand. For this reason, the company launched a logistics project with a mission to improve the situation using a considerable budget given. At first, we had no clue at all, so we started by gathering information by participating in exhibitions and study sessions.
Takeda: Did you talk with many vendors?
Mizutani: Yes. While meeting with different vendors, we decided to choose a system that could be achieved within our budget, solve the most annoying problem, and greatly benefit us. Actually, we had almost no problems with the products we complete ourselves. Meetings with vendors made it apparent again that the real issue is the complex process management of products half-finished by us and half-finished by a contractor.
Nakagawa: Let me add something here. We could not tell what was happening with outsourced products in real-time. We had no idea where to start, what to digitize, and what to inventory. It was like grabbing at a cloud.
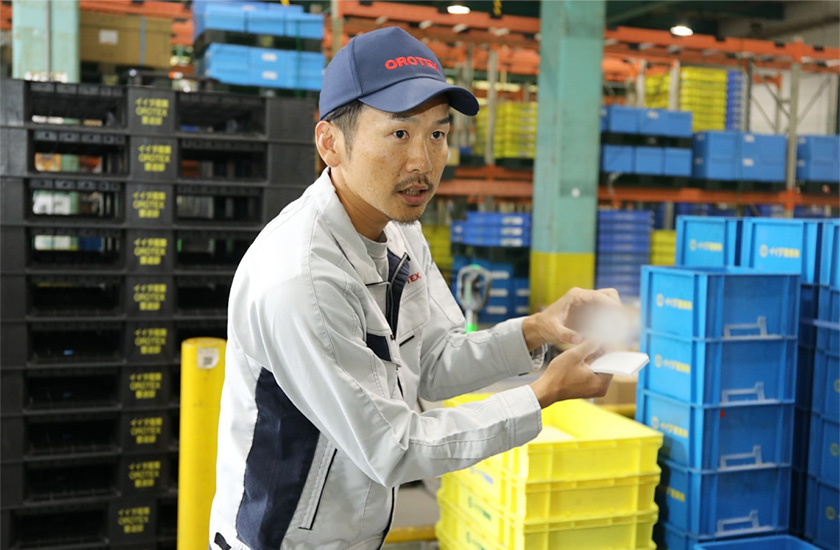
Mizutani: Although we had talks with many vendors, we did not reach the point of choosing the right vendor because we failed to make them clearly understand our intention or communicate with them very well. Then, Fujitsu offered us a free consultation to check all the steps of operation onsite, saying "Let's find issues together." After the check, Fujitsu concluded, "By introducing the MES system for inventory management, Iida Industry could solve all of its issues." Satisfied with the explanation, we installed the system in March 2018.
Project Team’s Willingness to Learn Thaws Resistance to DX
Takeda: Our clients often ask us how exactly to proceed with DX. In your case, your production management and information system divisions saw things differently and wanted to improve on different things. How did you go about prioritizing?
Mizutani: There were four of us when we launched the logistics project. After much discussion, we decided to prioritize managing contractors, which was the most time-consuming task, followed by physically checking received goods, which we had not been able to do. Of course, it was difficult because we did not know who to consult and we were on our own.
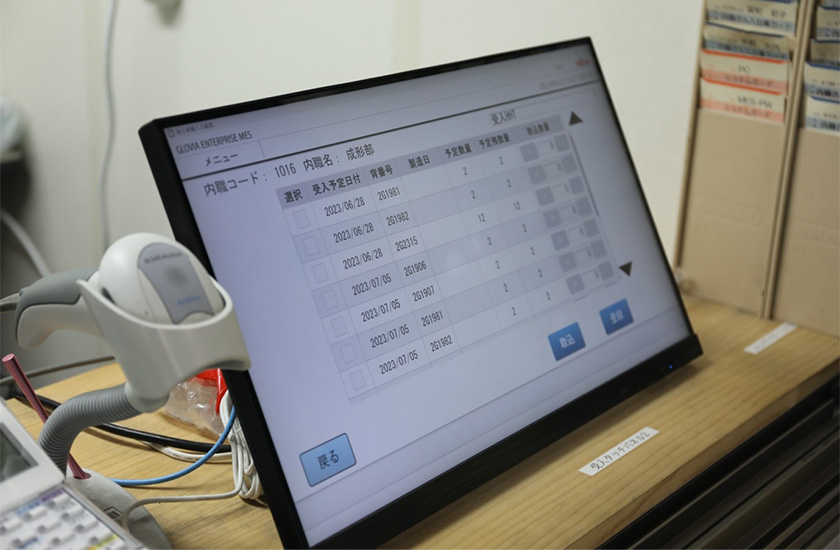
Takeda: May I ask what has happened since you installed the system?
Aoyama: I was not a member of the team that looked into introducing the system; I was assigned just before the installation. Even though he was a manager at the time, I saw Mizutani going to the front lines to learn how to use the new system from square one. Nakagawa and the others saw it, too. I was impressed that we all pursued the project as we learned from his way.
Yoshida (Fujitsu): The day the system was introduced, Mr. Mizutani was unable to use the system, and I myself asked him to increase the number of staff members. The next day, he was a different person—he could do everything he could not the day before, which I thought was truly amazing. I agree that that sort of effort spread throughout the company.
Takeda: We use the term "starting small," but what were some of the challenges you faced in customizing the system from there and making it your own?
Mizutani: It seemed to me that everyone but the members of the logistics project team were resistant to anything new. It was challenging to convince them.
Takeda: How did you overcome such pervasive rejection of new things?
Mizutani: We kept encouraging them, pointing out things that DX would improve and saying that things would get better. In any case, I made every effort to highlight the benefits of the project to get them to accept it.
Nakagawa: For me, ordering the new system build was more difficult than dealing with things in-house. For example, a painstakingly designed touch panel did not work well in actual operation, and data extraction was also found to be lacking in some areas in actual practice. The greatest difficulty came in figuring out how to ask for the system to be built with the outcomes in mind. Fujitsu made many improvements and has offered many insights during the process, so we are bringing them all together as we move forward.
Aoyama: I am in a position to receive the most feedback from the front lines, so I grappled with the question of how to get on the same page as them. Now that the system has been introduced, front-line personnel demand a fast-paced customization.
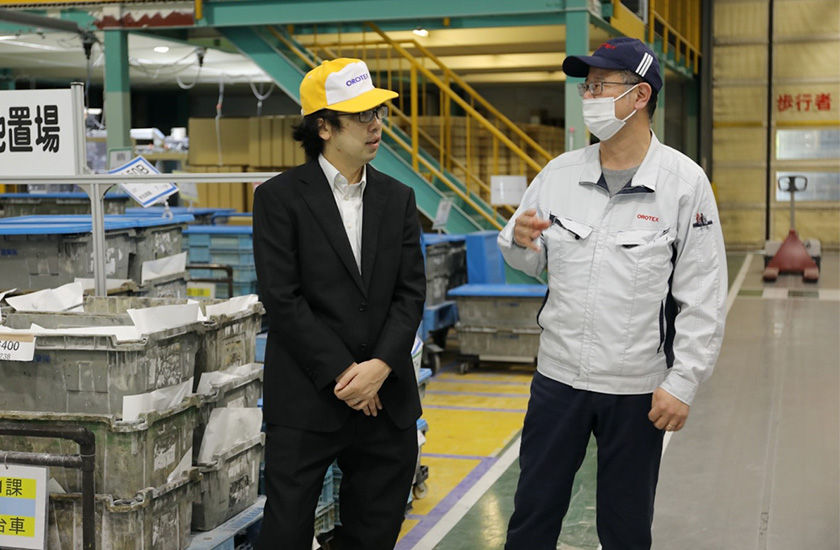
Realizing New Work Styles After Introducing DX
Takeda: What are the current structure of the project and your plans for promoting it in the future?
Mizutani: First, we made it possible to see the inventory of partially finished products, followed by the inventory of finished products through MES. This year, we are in the process of developing production plans. Our vision beyond that is to expand to subsidiary materials and eventually link them to production and shipping plans. We hope to continue working with Fujitsu to make gradual progress on this every year.
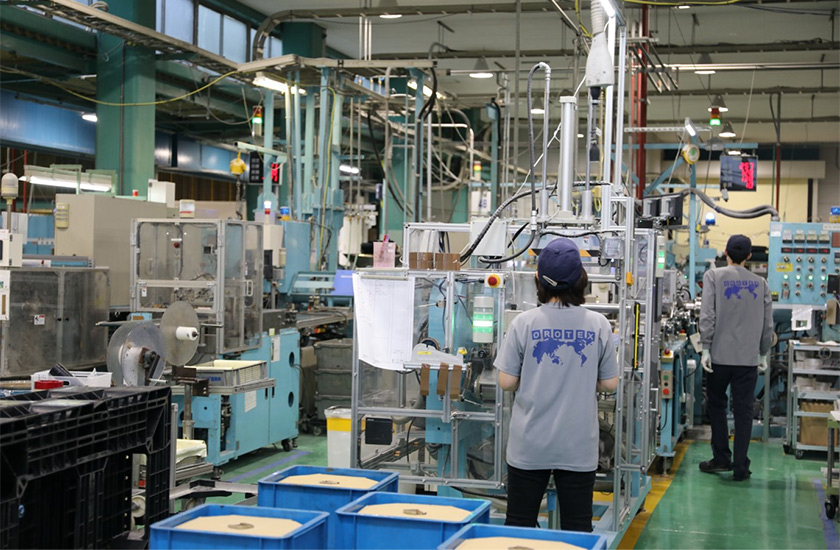
Takeda: What are some of the actual benefits you have enjoyed since introducing the system?
Mizutani: First and foremost, the accuracy of our inventory control has vastly improved. For example, we no longer need to input receiving work with contractors, which greatly reduces misshipments stemming from human error. Now we can check products, so mistakes and shipping delays have been eliminated. With MES in place, we stopped using vouchers with contractors because we get automatic receipts.
At month-end, we get a single invoice that allows us to proceed without errors.
Takeda: Let’s hear from someone who works with the system.
Aoyama: Originally, we had no information, but the information we get thanks to DX allows us to immediately show the details of inquiries, for example which partially finished products are where. Digitization allows us to instantly make lists that tell us what is happening with the products and do other things that meet a variety of needs.
Takeda: Does Fujitsu experience any benefits or effects?
Yoshida (Fujitsu): In 2018, Mr. Mizutani seemed really busy, but now I hear that he no longer works overtime. This makes me feel that MES has helped him.
Mizutani: It has helped my subordinates, too. Things are now visualized in terms of numbers, and the benefits are spreading to the point of changing how we work for the better.
Takeda: What is your outlook for the future?
Mizutani: The first step is to make an improvement using MES inventory to produce a planning index. We will expand this improvement not only to products, but also to raw materials and subsidiary materials, eventually achieving total visualization from receiving to shipping. I believe Fujitsu has the core systems and other tools necessary for this, so I intend to use them while moving forward with DX.
Nakagawa: Ideally, the same idea as Mizutani—centrally managing incoming raw materials, subsidiary materials, and the like from which various automatic calculations can be made. I also want to develop a system that produces the same figures no matter who does the work. This would allow us to anticipate and be more accurate when we respond to things like demand forecasts. In the automotive industry, we have unofficial projected figures that inevitably involve feel and guesswork, so we want to use DX to visualize these and create a system capable of rotating the absolute minimum of inventory.
Aoyama: I want to quickly figure out how to present the outcomes of informatization, quantification, digitalization, and visualization in ways that are easy for users to grasp. That would probably take us into the realm of BI tools.
The Passion to Improve Is Essential for Eradicating Resistance to New Things
Takeda: What advice would you give to those who are hesitant about promoting digitalization?
Aoyama: There is a large gap between the old way of doing things and the digital way, so we will need to study up. Mizutani also had a great influence on everyone around him with the way he started from nothing and studied until he was able to use the system.
Nakagawa: First and foremost, you have to try. Of course you will face resistance, doubt, and disbelief along the way, but the important thing is to show that you get results by giving things a try.
Mizutani: The hardest thing is to eliminate resistance to trying new things. There is this belief that the way things are done now is best, and it takes a certain amount of effort to change things. We need to be able to clear that hurdle. This ability is rooted in the passion to improve things and leave things in better shape for the people who come after us.
Takeda: In closing, what do you expect from Fujitsu?
Nakagawa: We are very happy when you give suggestions. There is a lot we don’t know about what else this system can do. It is important for us to ask if the system can do this or that, but it is also very helpful when you make suggestions.
Aoyama: In the first consultation, you showed us exactly where the bottlenecks were. We would appreciate if you could find the remaining issues and suggest improvements for each one.
Mizutani: Once I was involved in implementing the system, Mr. Yoshida was the main person in charge on the Fujitsu side. His on-point advice is the reason we have enjoyed our relationship to this point. There are always things we cannot see on our own, so we hope that you will continue to work alongside us.
Takeda: Thank you for your kind words. I will take your comments on board and give them the consideration they deserve.
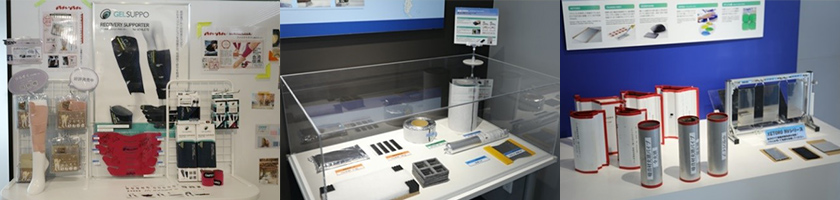
[ Published in October 2023 ]
Download the free catalog here
Manufacturing cluster that realizes manufacturing DX
Provided by Fujitsu SAP Manufacturing Execution System (MES)
Provided by Fujitsu
SAP Engineering Manufacturing Execution Solution
Enquiries and consultation about Fujitsu Digital Manufacturing FJVPS
Company uses SSL technology for security purposes.