- Fujitsu Manufacturing Solutions
- Offerings
- Production Preparation Sophistication Offering
- Upgradation of cost and production Offering
- Solutions
- Fujitsu Application for SAP® Solutions
- Production Planning
Fujitsu Application for SAP® Solutions Detail Scheduling Template - Build-to-order manufacturing
Fujitsu Application for SAP® Solutions Mass Customization Template - Actual Cost
Fujitsu Application for SAP® Solutions Actual Costs Template - SAP S/4HANA® Manufacturing for Production Engineering and Operations (SAP PEO)
- SAP® Digital Manufacturing (SAP DM)
- SAP® Integrated Business Planning (SAP IBP)
- SAP® Portfolio and Project Management (SAP PPM)
- Case study
- SAP S/4HANA® Manufacturing for Production Engineering and Operations (SAP PEO)
- Kawasaki Heavy Industries, Ltd.
- Kawasaki Heavy Industries, Ltd. (Fujitsu Uvance)
- Kawasaki Heavy Industries, Ltd. (SAP Website)
- SAP® Digital Manufacturing (SAP DM)
- Anaplan
- Fujitsu Supply Chain Planning Solutions
(Old name: FUJITSU Enterprise Application GLOVIA smart PROFOURS
FUJITSU Manufacturing Industry Solution COLMINA scheduler / PSI)
- FUJITSU DIE-TECH CORPORATION OF THE PHILIPPINES Innovative Case Study Report on Production Planning Operations in the Global Supply Chain GLOVIA smart PROFOURS (PDF)
- Successful application of "PROFOURS" in FUJITSU DIE-TECH CORPORATION OF THE PHILIPPINES (YouTube)
- Tohshin Seiki Co.,Ltd. (PDF)
- RISU PACK CO., LTD. (PDF)
- GOLD PAK CO., LTD. (PDF)
- Fujitsu Limited (PDF)
- Fujitsu Supply Chain Planning Solutions
- Fujitsu ERP Solutions for Process
(Old name: FUJITSU Enterprise Application GLOVIA ProcessC1)
- TOAGOSEI CO., LTD. (PDF)
- ASAHI BREWERIES, LTD. (PDF)
- NIHON NOHYAKU CO.,LTD. (PDF)
- Nippon Light Metal Company, Ltd. (PDF)
- ADEKA Corporation (PDF)
- Showa Denko K.K. (PDF)
- Fujitsu Digital Manufacturing FJVPS
- Fujitsu ERP Solutions for Process
- Catalog
- List of introductory materials on Planning Sophistication Offering
- Supply Chain Planning Solutions for Profit Maximizing S & OP Processes
SAP® Integrated Business Planning (SAP IBP) - Integrated Production Planning Solution for Supply Chain DX
GLOVIA smart PROFOURS
- List of introductory materials on Manufacturing execution management sophistication Offering
- List of introductory materials on Upgradation of cost and production Offering
- List of introductory materials on Upgradation of cost Offering
- For SAP deployment users
Cost / Profit and loss management solutions
Fujitsu Application for SAP® Solutions Actual Costs Template
- List of introductory materials on Upgradation of production Offering
- Fujitsu best add-in solution for flexible use of SAP
Fujitsu Application for SAP® Solutions Mass Customization Template - An ERP solution for Assembly Manufacturers Realize Mass Customization through Product Configuration Management
Fujitsu Application for SAP® Solutions Mass Customization Template (SIEMENS) - Provided by Fujitsu SAP Engineering Manufacturing Execution Solution
SAP S/4HANA® Manufacturing for Production Engineering and Operations (SAP PEO) - Solutions to manage all multiple parallel planning, development, and investment projects
SAP® Portfolio and Project Management (SAP PPM) - Fujitsu’s SAP Manufacturing Solutions
- Video (YouTube)
- List of videos (YouTube) related to Planning Sophistication Offering
- Successful application of "PROFOURS" in FUJITSU DIE-TECH CORPORATION OF THE PHILIPPINES
- Fujitsu Manufacturing DX journey to the best
- An Integrated Planning and Management Solution “PROFOURS” : A reliable field partner
- GLOVIA smart PROFOURS - Integrated production planning system for improving work efficiency
- Production Scheduling Software " Fujitsu Enterprise Application GLOVIA smart PROFOURS"
- List of videos (YouTube) related to Upgradation of cost and production Offering
- Fujitsu Manufacturing DX journey to the best
- Fujitsu Application for SAP Solutions makes mass customization for manufacturing possible
- Fujitsu Application for SAP® Solutions Mass Customization Template
~Product Concept Version~ - Fujitsu Application for SAP® Solutions Mass Customization Template
~Quotation Version~ - Fujitsu Application for SAP® Solutions Mass Customization Template
~Order Navigator Version~ - Introduction Fujitsu Manufacturing Industry Services
- Fujitsu Transforming the future of manufacturing
- List of videos (YouTube) related to Manufacturing execution management sophistication Offering
- Fujitsu Manufacturing DX journey to the best
- How to keep manufacturing operations compliant
- Smart Manufacturing Customer References with COLMINA and SAP Offerings ”Collaboration with SEMENS”
- FNC uses Fujitsu SAP to build the factory of the future
- Reimagine your business with Fujitsu and SAP : KAWASAKI case study
- Transform your manufacturing to next generation with Fujitsu SAP Industry 4.0
- SAP® Manufacturing Integration and Intelligence (SAP MII) Solution proposed by FUJITSU
- Events and Seminars
Shaping Future of Manufacturing and Innovation force
Fujitsu Manufacturing Solutions
What is Fujitsu Manufacturing DX?
Fujitsu's Commitment to Manufacturing Solutions
Ensure the continued use of ERP by our valued customers
We believe that what is required of ERP/SCM today are ERP/SCM that is resistant to change and user-friendly enterprise application that ensure a high level of usability.
The key to achieving this lies in 'Manufacturing Expertise'.
Fujitsu, itself a manufacturing company, has three commitments which are leverage its DNA as a manufacturing company, its manufacturing knowledge and ERP expertise.
We are committed to ensuring that our customers continue to use our ERP solutions. As a unique ERP vendor for manufacturing companies, we provide comprehensive support for our customers' digital transformation.
What is Fujitsu’s Manufacturing Digital Transformation (DX) ?
The key elements of manufacturing DX are engineering chain business processes such as design BOM/manufacturing BOM, which are related to manufacturing specifications and the response to changes in specifications has a significant impact on manufacturing productivity and quality.
The main point is centrally managed with digital information of the engineering chain, which covers operations from design to production, and how to transmit, share the information and keep track the changes for entire manufacturing departments.
Fujitsu believes that key points for the digital transformation(DX) of manufacturing are speeding up business processes by consistently linking tasks from design to production using the same information from a digital thread/data-driven perspective, and ensuring advanced analysis and traceability by leveraging data effectively across business processes.
Fujitsu's vision for DX, business process integration and circular concepts in the manufacturing sector
The seamless connection between engineering and supply chain processes enables us to enhance productivity and quality, key drivers of success in the manufacturing domain. This interconnectedness creates a resilient environment, responsive to dynamic market conditions. This directly addresses critical management challenges highlighted by business leaders: "Responding effectively to change " and "Data-driven decision-making"
Step-by-step approach for proceeding with Manufacturing DX
In order to realize DX, it is important to take a reasonable approach to DX by understanding and benchmarking one's own current level.
For example, here is a graphic representation of the concept of DX achievement as an indicator for each customer to realize DX for their own operations and industry.
In this way, the key point is to define the level based on the step-by-step concept of digitization first, then connect the processes, and then autonomously generate value from the connected results. By understanding and benchmarking the current level of DX achievement, a reasonable approach to DX can be found.
Main DX Themes and Usage Scenario Level MAP Figure
The Step-by-Step approach explained so far, defines a level for each category and DX theme, and summarizes and organizes the degree of DX achievement at each level in the form of usage scenarios.
The key point of the Step-by-Step approach is to share the current state of each customer based on this "usage scenarios level" and share the "theme" and "level" to be raised in the future. For example, by defining the desired state level 4 from the current state level 1, while realizing the effects, the path is improved each time and approaches the ideal state.
Manufacturing DX Theme and Problem Solving Solution System
Manufacturing DX Themes and Challenges to Realize Company's Management Reform in Manufacturing Domain
At Fujitsu main themes of reform management categorize as "Design Sophistication", "Production Preparation Sophistication", "Planning Sophistication", " Costing and Production Sophistication", "Manufacturing Execution Management Sophistication" and "Leveraging Manufacturing Data Sophistication". These are main manufacturing DX themes and provide guidance for systemization and business reform. By building a business process model that utilizes the solutions needed to realize each theme, and can achieve the customer's DX manufacturing goal.
Addressing challenges in manufacturing ECM process through below offerings
Design Sophistication Offering
In a market demanding low-cost, high-quality manufacturing, achieving both quality and efficiency poses a significant challenge. Designers require advanced skills while facing the additional hurdle of securing and developing talent due to shrinking workforce. Through the 'Design Sophistication Offering', we leverage share data from design, production and maintenance to drive innovation in the manufacturing process. Expertise and automation in design data empowers labor efficiency and the transmission of advanced design skills.
3D Equipment Design
3D Mechanical Design
- Collaboration and Sharing of Manufacturing Information
Integrate data information from design, manufacturing and assembly, enabling a revolutionary new manufacturing process. Furthermore, storing design information for machine, electrical, and control systems in a centralized data platform enables its utilization for design consideration, verification in manufacturing and maintenance services. This also enables environmentally friendly designs. - Design know-how Digitization
By incorporating automation into design process through the input of parameters, there is substantial decrease in both time and labor. This augmentation bolsters the efficacy of design tasks and expedites dissemination of sophisticated design technology.
Bill of Material (BOM)
Manufacturing industry faces the challenge of accelerating new product design and production due to the diversification of customer needs and shorter product lifecycles. A bill of material (BOM) provides a comprehensive overview of the unit and material to produce a finished product. It is linked with technical information such as change specifications, cost, CAD data, technical documents. Digital thread seamlessly transmits product information from design to production, streamlining the manufacturing process and reducing lead times and costs. In addition, accumulating technical information, mainly BOM information, addresses critical challenges such as ensuring traceability in case of product issues and facilitating technology knowledge transfer to younger employees.
Design Simulation
Optimize product quality (Q), cost (C), and delivery (D) through predicting of product performance at the early stages of product development and identify potential issues proactively. In addition, leveraging High-Performance Computing(HPC), rapid model-based combinatorial validation, and utilizing AI for prior predictions etc. alongside CAE to significantly reduce your time and cost.
Chemical Substance Management
Centralize information of chemical substances, achieve depersonalized operations, reduced workload, and improved operational quality. Additionally, it responds to the request of product LCA/CFP information, and formulates measures to analyze, evaluate and reduce environmental impact of product throughout its life cycles.
Production Preparation Sophistication Offering
The diverse market needs has led to increasingly complex manufacturing demands, including the need for multi-variety small-batch production, automation, and continuous quality improvement. The reliance on human knowledge and labor for production preparation tasks has reached its limit. Through the "Production Preparation Sophistication Offering", we introduce the BOP (Bill of Process) data model, which encompasses the "5Ms of Production". The offering also consolidates scattered production information and seamlessly integrates design and manufacturing processes. This enables advanced consideration based on data before actual production, immediate confirmation of the impact of changes such as plan changes or quality issues, and decision-making while simulating countermeasures, achieving sophisticated manufacturing that is resilient to changes.
Digital Production Preparation
Integrate design information such as 3DCAD data and E-BOM, and create a BOP data model that links with "5Ms of Production", enables to centralized scattered production information and seamlessly connect the entire process, from upstream to downstream and shopfloor operations. We leverage VR for interactive testing through the digital verification using virtual line and virtual facility, facilitate early detection and improvement of potential issues. Additionally, integrate BOP with system such as M-BOM and MES, enables overall optimization from production preparation to mass production.
Production Preparation Data Management
Manage BOP data created based on drawing number systematically and securely to ensure data reliability. Integrate BOP data with PLM system creates a seamless flow of information between design and manufacturing.
Addressing challenges in manufacturing SCM process through below offerings
Planning Sophistication Offering
In the age of unpredictable VUCA, human coordinated planning has its limitations. It is important to improve the planning process in order to quickly recognize changes and respond to them immediately. The "Planning Sophistication Offering" connects planning between companies and within companies, and provides a mechanism to speed up decision-making throughout the entire supply chain.
Financial Planning
With top-down and bottom-up two-way communication, a financial (budget) plan is created that is consistent throughout the company and conduct simulations that are linked to daily operational plans. Efficient information sharing throughout the company and visualization of KPIs that maintain consistency between management and worksites contribute to maximizing profits.
Supply and Demand + Manufacturing Planning
The supply and demand balance adjustment, which includes not only products but also work-in-progress and intermediate products, and more detailed manufacturing plans that take site restrictions into consideration are mutually linked to realize smooth simulations of changes in demand, site troubles, and other situations. Efficient information coordination between the head office and the field contributes to quick and optimal decision-making in response to change.
Supply and Demand Adjustment (PSI)
Centralize manage sales, inventory, production, and procurement data, visualize warnings in real time about changes in the situation. It enables automatic and manual scheduling of production and procurement plans while maintaining inventory balance, taking into account limitations such as plant loads and warehouse capacity. By adjusting supply and demand in real-time to reflect changing circumstances, it optimizes inventories and enhances the ability to respond quickly and flexibly to changes.
Manufacturing Shop Floor Scheduling
It aggregates detailed manufacturing limitations that differ from industry to industry, and specialist know-how. It can achieve automatic and manual scheduling that takes into account constraints and resources (people, factories, equipment loads).
It contributes to eliminating the number of employees through centralized management of information and know-how, reducing the workload by planning automation, and improving the planning speed.
Costing and Production Sophistication Offering
In the manufacturing industry that survives the VUCA era, the key to corporate survival is the realization of a DX manufacturing with a mechanism for data-driven management and physical strength. In addition, it is becoming more advanced to realize production process operations (design, production, procurement, arrangement, etc.) that can be analyzed and executed immediately by digitally sharing actual data required by management and manufacturing shop floor. As a result, it is possible to feed back the actual site results to design, eliminate defects, visualize production results, and respond to changes in a timely manner.
Data-driven Management
In the process industry, we deal with "fluctuations in raw material prices" such as rising prices of naphtha and imported raw materials, "discrepancies in actual production orders" due to manufacturing conditions such as seasonal fluctuations, and "complex production processes" due to inverted tree type production. There is a need for cost and profit/loss management that takes into account market fluctuations and industry characteristics. This offering actively aids customer's data-driven management by focusing on cost and profit management.
Mass Customization
This solution is designed to help customers in the manufacturing industry achieve mass customization by eliminating the complexity of their work. Through integrated manufacturing solutions with SAP ERP, provide benefits such as "improved operational efficiency", "improved usability" and "use of the latest technology" for customers with various production models such as repetitive production, make to order production, and engineering to order production.
Manufacturing Execution Management Sophistication Offering
In this uncertain era, manufacturing shop floors are required to seamlessly integrate management and production activities to address various challenges, including a declining workforce and diversifying needs. Building a data-driven manufacturing environment that enables the PDCA cycle throughout the company, which enables the collection, analysis, and feedback of real-time on-site information from inside and outside the company, will lead to the manufacturing execution management sophistication. It enables the creation of a flexible manufacturing execution management system by integrating standardized information for management decisions with real-time data optimized for various production scenarios.
In-plant Logistics
We enable comprehensive factory inventory management by managing the location of materials, intermediate products, and finished products across all production sites, including in-house and external plants, and tracking real-time inventory information. This leads to optimized and sophisticated in-plant logistics tailored to specific manufacturing needs. Additionally, relocating manufacturing-related goods creates an environment where customers can focus on production by maximizing workspace and minimizing human errors like picking mistakes.
Manufacturing Execution
It serves as the foundation for collecting, storing, and linking manufacturing information that supports the supply and engineering chains. It provides instructions on design and work information to workers in a timely and easy-to-understand manner, and collects results without burdening them. This is the first step towards digitalizing the workplace and enhancing manufacturing execution management.
Factory Visualization
We visualize performance data accumulated in manufacturing according to the respective positions of top management, middle management and worker. This not only enables confirmation of progress on the manufacturing shop floor but also drives improvement activities and analysis.
Traceability
Heavy industry and engineering customers require comprehensive manufacturing management, from order intake to design, manufacturing, and production result. The manufacturing process involves various measures, including periodically design, design changes, process defect management, and rework. Even in this complex environment, product serial verification (tracing) for safety, functionality, and effectiveness is achieved through assured quality from design to production/manufacturing.
Leveraging Manufacturing Data Sophistication Offering
Equipment Maintenance Management
Unexpected failures and unplanned outages on manufacturing equipment can have devastating impacts. To prevent these issues, it's crucial to leverage routine maintenance records and equipment data effectively. By collecting, visualizing, and analyzing this data, we can enable early detection of abnormalities and efficiently analyze their causes. This leads to improved operational stability, product quality, and maintenance processes.
Manufacturing digital transformation (DX) theme and solution system to realize management innovation
Fujitsu Solution for ECM Upstream Processes in Manufacturing
Fujitsu Solution for SCM Downstream Processes in Manufacturing
Manufacturing Digital Transformation offerings by theme
Production Preparation Sophistication Offering Official Website
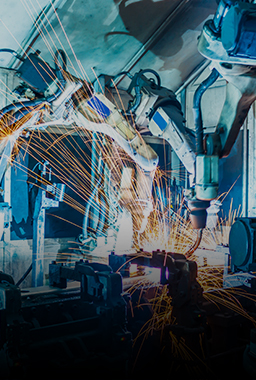
Sophistication
Offering Official
Website
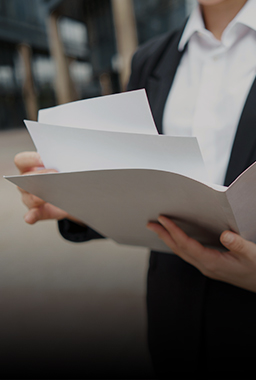
- Under Construction
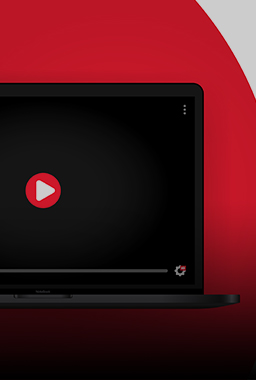
- Under Construction
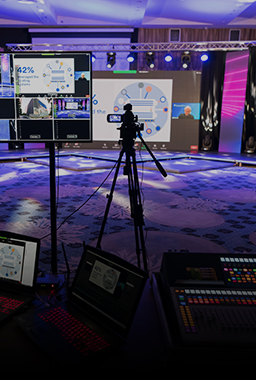
- Under Construction
Planning Sophistication Offering
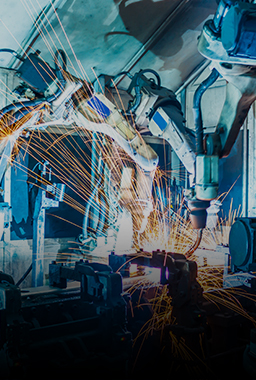
Sophistication
Offering Official
Website
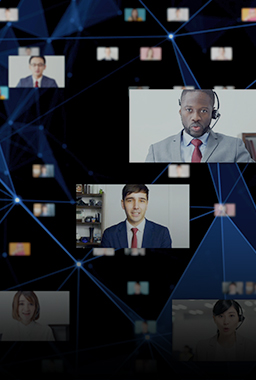
- Cutting costs and streamlining operations in the era of VUCA-Helping our clients transform their business operations based on our internal firsthand experience-
- 【Fujitsu Internal Practice】Workforce Planning Realized with Anaplan Short version (YouTube)
- 【Fujitsu Internal Practice】Workforce Planning Realized with Anaplan Full version (YouTube)
- FUJITSU DIE-TECH CORPORATION OF THE PHILIPPINES Innovative Case Study Report on Production Planning Operations in the Global Supply Chain GLOVIA smart PROFOURS (PDF)
- Successful application of "PROFOURS" in FUJITSU DIE-TECH CORPORATION OF THE PHILIPPINES (YouTube)
- Tohshin Seiki Co.,Ltd. (PDF)
- RISU PACK CO., LTD. (PDF)
- GOLD PAK CO., LTD. (PDF)
- Fujitsu Limited (PDF)
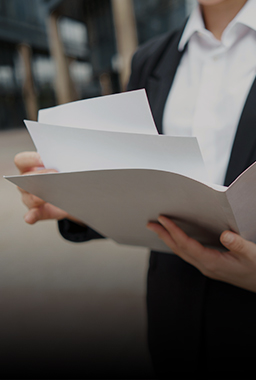
- List of introductory materials on Planning Sophistication Offering
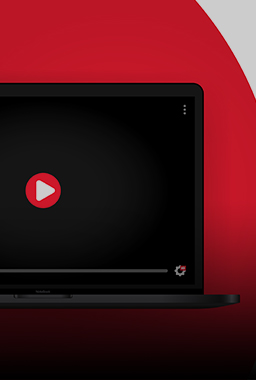
【Fujitsu Internal Practice】Workforce Planning Realized with Anaplan Short version (YouTube)
【Fujitsu Internal Practice】Workforce Planning Realized with Anaplan Full version (YouTube)
Successful application of "PROFOURS" in FUJITSU DIE-TECH CORPORATION OF THE PHILIPPINES
Fujitsu Manufacturing DX journey to the best
An Integrated Planning and Management Solution “PROFOURS” : A reliable field partner
GLOVIA smart PROFOURS - Integrated production planning system for improving work efficiency
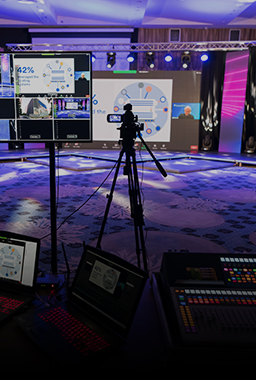
- Under Construction
Costing and Production Sophistication Offering
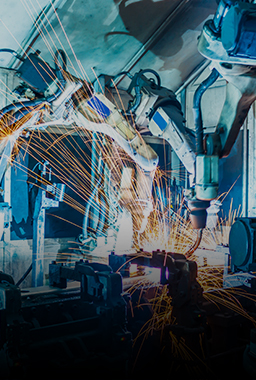
Sophistication
Offering Official
Website
- Upgradation of cost Offering
- Fujitsu Application for SAP® Solutions Actual Costs Template
- Fujitsu ERP Solutions for Process
(Old name : FUJITSU Enterprise Application GLOVIA ProcessC1)
- Upgradation of production Offering
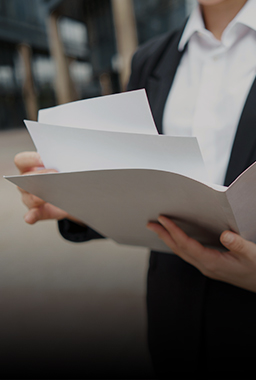
- List of introductory materials on Upgradation of cost Offering
- List of introductory materials on Upgradation of production Offering
Fujitsu best add-in solution for flexible use of SAP
Fujitsu Application for SAP® Solutions
Mass Customization TemplateAn ERP solution for Assembly Manufacturers Realize Mass Customization through Product Configuration Management
Fujitsu Application for SAP® Solutions
Mass Customization Template (SIEMENS)Provided by Fujitsu
SAP Engineering Manufacturing Execution Solution
SAP S/4HANA® Manufacturing for Production Engineering and Operations (SAP PEO)Solutions to manage all multiple parallel planning, development, and investment projects
SAP® Portfolio and Project Management (SAP PPM)Fujitsu’s SAP Manufacturing Solutions
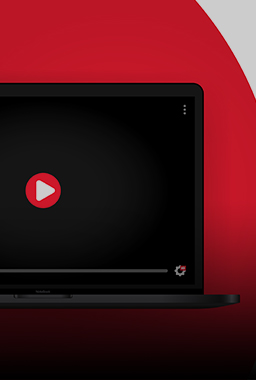
Fujitsu Manufacturing DX journey to the best
Fujitsu Application for SAP Solutions makes mass customization for manufacturing possible
Fujitsu Application for SAP® Solutions Mass Customization Template
~Product Concept Version~Fujitsu Application for SAP® Solutions Mass Customization Template
~Quotation Version~Fujitsu Application for SAP® Solutions Mass Customization Template
~Order Navigator Version~Fujitsu Transforming the future of manufacturing
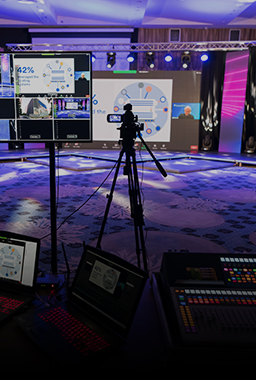
Manufacturing Execution Management Sophistication Offering
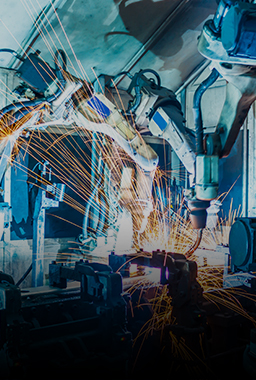
Sophistication
Offering Official
Website
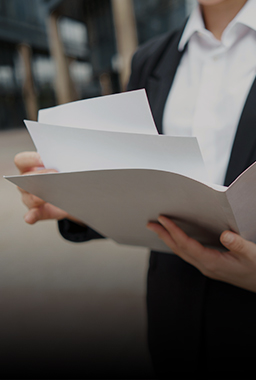
- List of introductory materials on Upgradation of production Offering
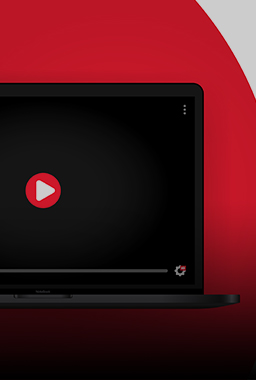
Fujitsu Manufacturing DX journey to the best
How to keep manufacturing operations compliant
Smart Manufacturing Customer References with COLMINA and SAP Offerings ”Collaboration with SEMENS”
FNC uses Fujitsu SAP to build the factory of the future
Reimagine your business with Fujitsu and SAP : KAWASAKI case study
Transform your manufacturing to next generation with Fujitsu SAP Industry 4.0
SAP® Manufacturing Integration and Intelligence (SAP MII) Solution proposed by FUJITSU
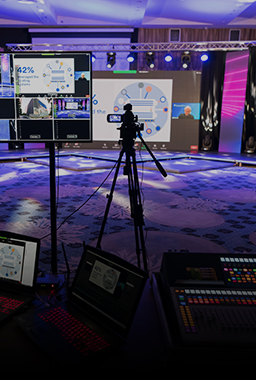
- Under Construction
Customer Voice
Fujitsu's approach to Manufacturing DX
Our SDGs Initiatives
As a Digital Transformation (DX) company, Fujitsu announced seven focus areas in April 2021 to accelerate growth with our customers, starting with addressing social issues. One of these areas is Sustainable Manufacturing, where we propose achieving a circulate and sustainable manufacturing. This aligns with the ecosystem approach to achieving the SDGs.
Fujitsu's mission is to deliver manufacturing solutions that address future uncertainties and diverse needs.
Our Capabilities
With our deep know-how and strengths as a manufacturing company, Fujitsu helps customers improve their business by leveraging its "manufacturing knowledge" in areas where it has extensive experience, such as optimizing business process in manufacturing shop floor.
Capabilities of SCM/ERP/MES solutions for manufacturing
- Manufacturing-specific knowhow Over 20 manufacturing locations in Japan
- Manufacturing (Design~Production~Result)
Develop business process application internally
Sole vendor in Japan - Our manufacturing solution implementations exceed 10,000