- 富士通の製造業
ソリューショントップ - ECMオファリング
- 設計の高度化オファリング
- Fujitsu Development Management for Manufacturing
- Fujitsu MBSE/MBD/CAE Solutions
- Fujitsu 設計製造支援 iCAD Solutions
- NX™ software
- Solid Edge® software
- Teamcenter® software
- Fujitsu Manufacturing Industry Solution COLMINA 技術情報管理 部品表
- Fujitsu Manufacturing Industry Solution COLMINA 製品含有化学物質管理
- Fujitsu Manufacturing Industry Solution COLMINA Design Review 高速リモートデスクトップ
- Fujitsu Product Development Process Management
- 生産準備の高度化オファリング
- Fujitsuデジタル生産準備 VPS
- Fujitsu Engineering Operation and Production Management (EOPM)
- Fujitsu Manufacturing Industry Solution COLMINA 技術ファイル管理 for Manufacturing
- Fujitsu Product Development Process Management
- 製造データ利活用の高度化オファリング
- Fujitsu Manufacturing Industry Solution COLMINA 設備点検
- Fujitsu Manufacturing Industry Solution COLMINA 設備保全管理 PLANTIA
- Fujitsu Product Development Process Management
- 関連オファリング
- SCMオファリング
- 導入事例
- エンジニアリング製造実行ソリューション(SAP S/4HANA® Manufacturing for Production Engineering and Operations(SAP PEO))
- SAP製造実行システム(MES)
- Fujitsu MES Solutions
(旧名称:FUJITSU Manufacturing Industry Solution COLMINA MES)
- Fujitsu Die-Tech Corporation of the Philippines様導入事例対談レポート(PDF)
- Fujitsu Die-Tech Corporation of the Philippines様導入事例対談動画(YouTube)
- 株式会社東振精機様(PDF)
- リスパック株式会社様(PDF)
- ゴールドパック株式会社様(PDF)
- 富士通株式会社(PDF)
- Anaplan
- Fujitsu Die-Tech Corporation of the Philippines様導入事例対談レポート(PDF)
- Fujitsu デジタル生産準備 VPS
- カタログ
- 設計の高度化オファリングに関するご紹介資料
- Fujitsu Development Management for Manufacturing
- Fujitsu 設計製造支援 iCAD Solutions
- Fujitsu MBSE/MBD/CAE Solutions
- 生産準備の高度化オファリングに関するご紹介資料
- 計画の高度化オファリングに関するご紹介資料一覧
- 原価・生産管理の高度化オファリングに関するご紹介資料
- 生産管理の高度化オファリングに関するご紹介資料
- 製造実行管理の高度化オファリングに関するご紹介資料
- 動画(YouTube)
- 計画の高度化オファリングに関する動画(YouTube)一覧
- Enterprise Visualization ~変化に強いポストモダンERPとMES~
- Fujitsu Die-Tech Corporation of the Philippines様導入事例対談動画
- デジタルスレッドで ものづくり変革
- 製造DXを実現するものづくりクラスター
- 富士通の製造DXに向けた取り組み
- 統合計画管理ソリューションPROFOURS~頼れる現場のパートナー~
- 食品製造業様向け統合計画管理ソリューション「GLOVIA smart PROFOURS」
- 計画業務パッケージ「GLOVIA smart PROFOURS」機能ご紹介
- 製造業向け統合計画管理システム「GLOVIA smart PROFOURS」
- 製造業向け統合計画管理システム「GLOVIA smart PROFOURS」
- 原価・生産管理の高度化オファリングに関する動画(YouTube)一覧
- Enterprise Visualization ~変化に強いポストモダンERPとMES~
- Fujitsu Application for SAP® Solutions Actual Costs Templateご紹介
- デジタルスレッドで ものづくり変革
- 製造DXを実現するものづくりクラスター
- 富士通の製造DXに向けた取り組み
- 富士通の考えるマスカスタマイゼーション対応方法
- Fujitsu Application for SAP® solutions Mass Customization Template
- Fujitsu Application for SAP® solutions コンセプトのご紹介
- 見積管理ソリューション~見積業務がこんなに簡単に!
- 手配管理ソリューション~手配業務がこんなに便利に!
- 産業機械製造業における活用シナリオ
- JSUG Conference2019 Fujitsu Speaker Message
- 「JSUG Conference2019」富士通セッションの講演者メッセージ
- 製造実行管理の高度化オファリングに関する動画(YouTube)一覧
- ニュース&イベント
製造業の未来を創る、革新の力となる
富士通の製造業
ソリューション
富士通がご提案する製造DXとは
富士通の製造業ソリューションへの想い
私達が大切にしていることは、お客様にERPを使い続けていただくこと
いまERP/SCMに求められているのは、社会環境の変化や事業の拡大に柔軟に対応できる「変化に強いERP/SCM」であること、そして煩雑になりがちなオペレーションであっても高いユーザビリティを確保した「使いやすいEnterprise Application Solution」であることだと考えます。
そのカギを握るのは「ものづくり知見」
自らが製造業である富士通には、ものづくり企業としての「DNA」があり、長年のERP導入経験により培われた、ものづくり知見を活かした3つのこだわりがあります。
私達が大切にしていることは、お客様にERPを使い続けていただくこと。
私達はものづくり企業ならではのERPベンダーとして、お客様のデジタル・トランスフォーメーションを強力にバックアップいたします。
富士通の製造DXとは
製造DXにおいて重要となる要素は、設計BOM/製造BOMなど、ものづくりの仕様に関わり、かつ仕様変更時の対応が、ものづくりの生産性や品質に大きな影響を及ぼすエンジニアリングチェーンの業務プロセスです。
設計~生産~現場までの業務をカバーしているエンジニアリングチェーンをデジタル情報で一元管理し、ものづくりに係るすべての部門に、いかに伝え、共有するのか、変化に追随していくのかが大きなポイントになります。
富士通は、デジタルスレッド/データドリブン強化の観点から、設計~製造現場までの業務プロセスを同一情報で一貫して繋ぐことにより業務のスピードアップを図ることや、業務プロセスを跨いてデータの有効活用をすることにより、高度な分析やトレーサビリティを確保できることなどが製造DX化のポイントであると考えます。
富士通が考える製造領域におけるDX化・業務プロセス連携・循環イメージ
エンジニアリングチェーンとサプライチェーンを連動することで、ものづくりの世界において重要となる生産性向上や品質向上、そして変化に柔軟に対応するレジリエンスな環境を作り出すことが可能となります。
これらはビジネスリーダーが経営重要事項として挙げているキーワードである「変化への対応力(レジリエンス)の重要性」 と 「データドリブン経営」という部分につながると考えています。
製造DX進め方のStep-by-Step例
DX実現に向けては、自らの現状レベルを把握/ベンチマークすることで、無理のないDX化へのアプローチが重要です。
例えばこちらではお客様はそれぞれ自分たちの業務と業種に合わせたDX化を実現していくための指標として、DX達成度という考え方がStep-by-Stepです。
レベル1からレベル5までをひとつひとつ階段を上るように、デジタル化から、そしてプロセスがつながり、つながった結果から自律的に価値を生み出す、というStep-by-Stepの考え方でレベル定義していくことがポイントであり、このDX達成度に対して、自らの現状レベルを把握・ベンチマークしていくことで、無理のないDX化アプローチが見いだせると考えます。
主要DXテーマと利用シーンレベルMAP例
これまでご説明してきたStep-by-Stepのアプローチは各カテゴリやDXテーマ毎にレベル定義をして、それぞれのレベルにおけるDX達成度を利用シーンという形でまとめ、整理しています。
この「利用シーンレベル」をもとに、お客様毎の現在の状態はどのレベルにあり、今後「どのテーマを」「どのレベルまで」引き上げるのかを共有して、例えば、現状レベル1から、ありたい姿レベル4を定義することで、効果を実感しながら、道筋を毎回改善しながら理想の姿へ近づけていく進め方をとることが、Step-by-Stepアプローチのポイントです。
製造DXテーマと課題解決ソリューション体系
ものづくり領域の経営改革を実現する製造DXテーマと課題
富士通では、経営改革テーマである「設計の高度化」「生産準備の高度化」「計画の高度化」「原価・生産管理の高度化」「製造実行管理の高度化」「製造データ利活用の高度化」のカテゴリにわけ、その中の課題を主要な製造DXテーマを設定し、システム化・業務改革における道標をご提供しています。各テーマの実現に向けて必要となるソリューション群を活用、業務プロセスモデルを構築することでお客様の製造DX化を実現します。
ものづくりECMプロセスの課題解決ソリューション
設計の高度化オファリング
市場から低コスト・高品質なものづくりが求められる中で、品質を維持しつつ効率化を進めることは容易ではありません。また、製品のライフサイクル全体にわたる環境影響を考慮した設計も求められています。さらに、これらを担う設計者には高度なスキルが必要ですが、労働人口減少による人材の確保・育成が大きな課題となっています。
「設計の高度化オファリング」では、設計から製造、更に保守サービスまで、全ての領域で共通のデータを活用し、ものづくりプロセスの革新を実現します。また、設計データへのノウハウの蓄積と自動化による省人化により、高度な設計技術の伝承を可能とします。
3D設備装置設計
3D機械設計
- ものづくり情報の連携・共有
設計から製造、組立まで、一元化したデータで情報を連携し、新たなものづくりプロセスを実現します。
また、データに機械・電気・制御の設計情報を蓄積することで、設計だけでなく、製造・保守サービスでの検討・検証におけるデータの活用を可能とし、環境負荷を低減した設計にも貢献します。 - 設計ノウハウをデジタル化
パラメータ入力による設計の自動化により大幅な時間短縮と省人化を行い、設計業務の効率化を実現するとともに、高度な設計技術の伝承を可能とします。
部品表(BOM)
ニーズの多様化とライフサイクルの短命化から、新製品の設計~生産の更なるスピードアップは製造業の重要な課題となっています。部品表(BOM:Bill of Material)は、製品を構成するユニットや品目等の諸元情報であり、これに変更仕様、コスト、CAD・技術文書など、製品に関する技術情報を紐づけて管理します。この情報を設計から生産へ伝達するデジタルスレッドにより、ものづくり全体のリードタイム短縮とコストダウンを実現します。またBOMを中心とした技術情報の蓄積は、製品の問題発生時のトレーサビリティの確保や、深刻化する若手への技術継承といった課題を解決します。
設計シミュレーション
製品開発の初期段階で製品の性能を予測し、問題点を早期に発見することで、製品の品質(Q)・コスト(C)・納期(D)を最適化します。昨今では従来のCAEに加え、HPCによる高度計算、モデルベースによる素早い組合せ検証、AIを活用した事前予測などにより、さらなる時間とコストの大幅な削減を実現します。
化学物質管理
含有化学物質対応に関する情報を一元管理し、業務の脱属人化や業務負荷軽減、業務品質の向上だけでなく、変化する環境法規や業界動向へのタイムリーな対応に貢献します。また、製品LCA/CFP情報の開示要求への対応や、自社製品のライフサイクルで発生する環境負荷の分析・評価・削減施策の策定に貢献します。
生産準備の高度化オファリング
市場ニーズの多様化により、多品種少量生産や自動化の推進、品質の向上など、ものづくりへの要求はますます複雑化し、人の知識や労力に頼った生産準備業務は限界が来ています。「生産準備の高度化オファリング」では、「製造の5M」を関連づけたデータモデルであるBOP(Bill of Process)を作成・管理することで、散在する生産情報を一元化し、設計と製造をスムーズにつなぎます。これにより、実機製作前からデータによる検討の前倒しを実現、計画変更や品質トラブルなど、変化発生時に影響確認を即座に行い、対策をシミュレーションしながら意思決定を行う変化に強いものづくりを実現します。
デジタル生産準備
3DCADデータやE-BOM等の設計情報を取り込み、 「製造の5M」を関連づけたデータモデルであるBOPを作成することで散在する生産情報を一元化し、上流から下流、製造現場までを一元的につなぎます。バーチャルライン検証やバーチャル設備によるデジタル検証を行い、VRを使用した体験型の検証により問題点の早期発見と改善を図ります。また、BOPを核に、M-BOM、MES等のシステムと連携し、生産準備から量産までの全体最適化に貢献します。
生産準備データ管理
図番単位で作成するBOPデータを複数図番でシステマティックかつセキュアに管理し、情報の信頼性を確保した運用を支援します。PLMシステムとのデータ連携により設計から製造間のスムーズな情報連携を実現します。
製造データ利活用の高度化オファリング
設備保全管理
製造設備の突発的故障や計画外停止の影響は非常に大きく、これらのトラブルを未然に防ぐためには、日々の保全記録や設備データの活用が重要です。
設備からデータを収集し可視化するだけでなく、蓄積したデータを分析することによる異常の早期発見や効率的な原因分析などにより、設備の安定稼働や品質向上、保全業務の改善活動を支援します。
ものづくりSCMプロセスの課題解決ソリューション
計画の高度化オファリング
予測不能なVUCAの時代において、人による調整型の計画業務には限界があります。変化にすばやく気づき、迅速に対応するためには、計画の高度化(仕組みづくり)が重要です。「計画の高度化オファリング」では、企業間・企業内の計画業務をつなぎ、サプライチェーン全体で意思決定を迅速化する仕組みを実現します。
財務計画
トップダウンとボトムアップの双⽅向でのコミュニケーションを⾏いながら、会社全体として整合性をもった財務(予算)計画を立案し、日々のオペレーション計画と連動させたシミュレーションを実現します。企業全体における効率的な情報連携と、経営-現場間で整合性を保ったKPIの可視化により、収益の最大化に貢献します。
需給+製造計画
製品だけでなく仕掛品/中間製品も含めた需給バランス調整と、現場制約を考慮したより詳細な製造計画を相互に連携し、需要変化や現場トラブルなどの状況変化に対するスムーズなシミュレーションを実現します。本社-現場の効率的な情報連携により、変化に対する迅速かつ最適な意思決定に貢献します。
需給調整(PSI)
販売・在庫・生産・調達のデータを一元管理し、状況変化に対するワーニングをリアルタイムで可視化します。工場負荷、倉庫のキャパシティ等の制約を考慮しながら、在庫バランスを保った生産・調達計画の自動/手動のスケジューリングを実現します。状況変化を即時反映した需給調整による在庫適正化、変化に対する迅速かつ柔軟な対応力の向上に貢献します。
現場作業スケジューリング
業種ごとに異なる細かい製造制約や、担当者固有のノウハウを集約し、制約やリソース(人・工場・設備負荷)を考慮した自動/手動のスケジューリングを実現します。情報・ノウハウの一元管理による属人化解消や、計画の自動化による業務負荷軽減、計画立案スピードの向上に貢献します。
原価・生産管理の高度化オファリング
VUCA時代を生き抜く製造業において、データドリブン経営を行えるしくみと体力を備える製造DXの実現が企業生き残りのカギです。また経営層・管理層・現場が必要とする実データをデジタル共有でき、即座に分析・実行できる生産プロセスのオペレーション(設計・生産・調達・手配など)を一気通貫で実現することが高度化となります。それにより、現場実績を設計へフィードバック可能とし、不具合の撲滅、生産実績の見える化とタイムリーな変動対応が可能となります。
データドリブン経営
プロセス産業では、ナフサの高騰や輸入原材料などの「原材料価格の変動」や、季節変動などの製造条件により「製造指図が実績が不一致」、逆ツリー型生産による「複雑な生産工程」への対応等、市場変動への対応や業界特性を考慮した原価・損益管理が求められています。経営に直結する原価・損益管理を起点に、お客様のデータドリブン経営を支えます。
マスカスタマイゼーション
製造業のお客さまの煩雑な業務を解消し、マスカスタマイゼーション実現を支援するソリューションです。SAP ERPとの統合型製造業ソリューションにより受注繰り返し生産から受注仕様生産・受注設計生産などさまざま生産モデルのお客さまに、「業務効率化」「ユーザビリティの向上」「最新テクノロジー利用」といったメリットをご提供します。
製造実行管理の高度化オファリング
労働人口減少やニーズ多様化といった課題を始め、不確実性な時代の中で製造現場は経営と生産活動をリンクさせた取組みにより様々な課題に取り組んでいく必要があります。社内外のリアルタイムな現場情報を収集、分析、フィードバックできるような、企業全体でのPDCAを回すデータドリブンなものづくり環境を構築することが製造実行管理の高度化に繋がります。経営判断のもととなる「標準化された情報」と様々なものづくり形態に合わせて最適化された「リアルな情報」を融合することで変化に追従できる製造実行管理実現をサポート致します。
構内物流
製造にかかわる全現場(自社工場・社外工場など)の『もの』(部材/中間品/完成品)の所在管理を行い、リアルタイムな実在庫情報を管理できるようになることで、工場全体の在庫最適化や製造に合わせた構内物流の高度化へ導きます。また、製造に伴った『もの』の移動を行うことで、作業現場のスペース確保やピッキングミスなどの人的ミスを防ぎ、ものづくりに集中できる環境を提供します。
製造実行
サプライチェーン、エンジニアリングチェーンを支える製造情報を収集、蓄積を行い、紐づけを行う根幹部になります。設計情報や作業情報を作業者にタイムリーでわかりやすく指示を出し、負担をかけない形で実績を収集することが現場デジタル化、更には製造実行管理高度化の一歩目となります。
工場見える化
製造で蓄積された実績データを経営層、管理層、現場層とそれぞれの立場に合わせた見える化を実現します。現場の進捗確認にとどまらず、改善活動や分析に繋げます。
トレサビリティ
重工業やエンジニアリング業のお客様においては受注から設計・製造・実績まで一気通貫でのものづくりマネジメントが必要です。また製造工程においては、さみだれ設計や設計変更、工程不良・リワークなどさまざまな対応も必要とされています。これら複雑なものづくり環境においても、設計から生産・製造における品質の作り込みにより確保された安全性・機能性・有効性の製品シリアルでの証明(トレース)を実現します。
経営改革を実現する製造DXテーマとソリューション体系
ものづくりECMプロセスの課題解決ソリューション
ものづくりSCMプロセスの課題解決ソリューション
製造DXテーマ別オファリング
設計の高度化オファリング
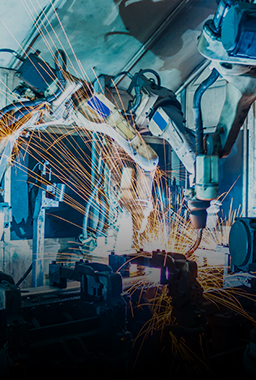
オファリング
製品ページ
- Fujitsu Development Management for Manufacturing
- Fujitsu 設計製造支援 iCAD Solutions
- Fujitsu Manufacturing Industry Solution NX
- Fujitsu Manufacturing Industry Solution Solid Edge
- Fujitsu MBSE/MBD/CAE Solutions
- Fujitsu Manufacturing Industry Solution Teamcenter
- Fujitsu Manufacturing Industry Solution COLMINA 技術情報管理 部品表
- Fujitsu Manufacturing Industry Solution COLMINA 製品含有化学物質管理
- Fujitsu Manufacturing Industry Solution COLMINA Design Review 高速リモートデスクトップ
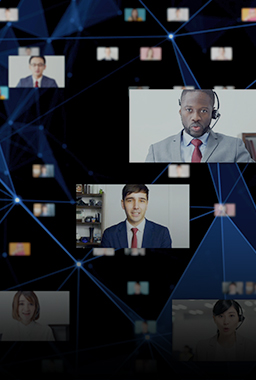
- 現在お知らせする情報はありません
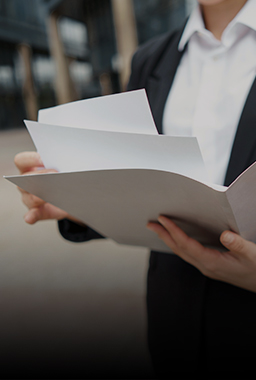
- 設計の高度化オファリングに関するご紹介資料一覧
Fujitsu Development Management for Manufacturing
Fujitsu COLMINA CAE 設計者向け構造解析
Fujitsu 構造解析ソフトウェア Jupiter-Designer
Fujitsu 構造解析ソフトウェア Jupiter-Post
Fujitsu 構造解析ソフトウェア Jupiter-Pre
Fujitsu 設計者向け熱流体解析ソフトウェア Autodesk CFD
Fujitsu 樹脂射出成形解析ソフトウェア Autodesk Moldflow
Fujitsu 樹脂流動解析ソフトウエア 3D TIMON®
Altair® HyperWorksご紹介カタログ
Altair® Unlimited Virtual Applianceご紹介カタログ
富士通 設計製造支援 iCAD SX
富士通 設計製造支援 iCAD MX
生産準備の高度化オファリング
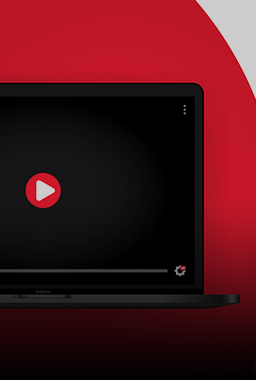
- 現在お知らせする情報はありません
製造データ利活用の高度化オファリング
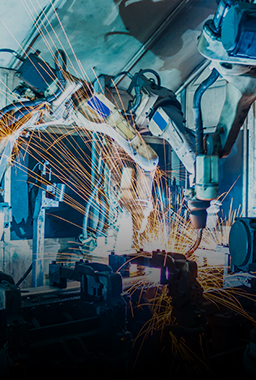
高度化オファリング
製品ページ
- Fujitsu Maintenance Solutions
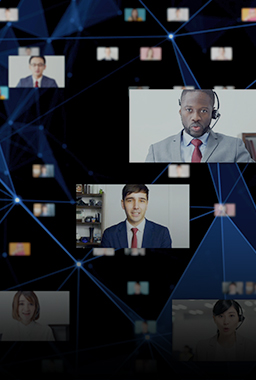
- 現在お知らせする情報はありません
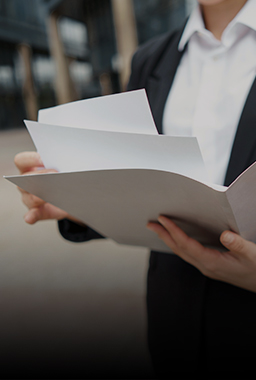
- 現在お知らせする情報はありません
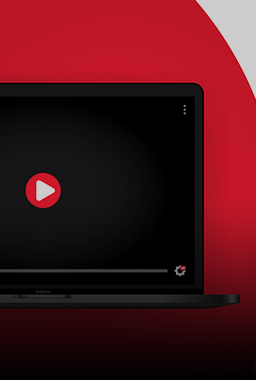
- 現在お知らせする情報はありません
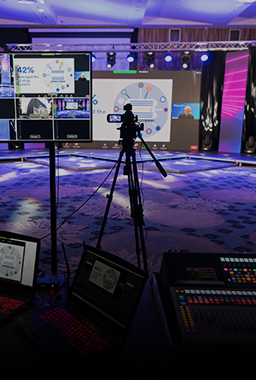
- 現在お知らせする情報はありません
計画の高度化オファリング
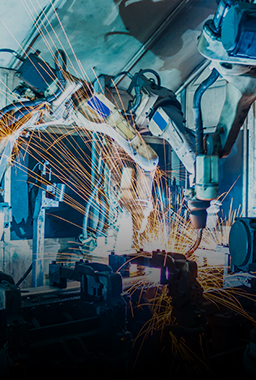
オファリング
製品ページ
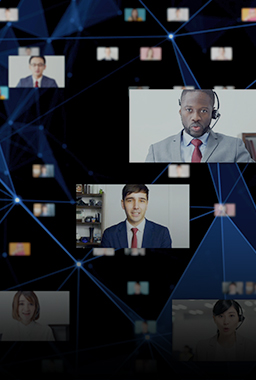
- VUCA時代にコスト低減や業務効率化を達成-社内実践からお客様のビジネス変革を支援
- 【富士通 社内実践】Anaplanで実現するWorkforce Planning (ショートバージョン)(YouTube)
- 【富士通 社内実践】Anaplanで実現するWorkforce Planning (フルバージョン)(YouTube)
- Fujitsu Die-Tech Corporation of the Philippines様導入事例対談レポート(PDF)
- Fujitsu Die-Tech Corporation of the Philippines様導入事例対談動画(YouTube)
- 株式会社東振精機様(PDF)
- リスパック株式会社様(PDF)
- ゴールドパック株式会社様(PDF)
- 富士通株式会社(PDF)
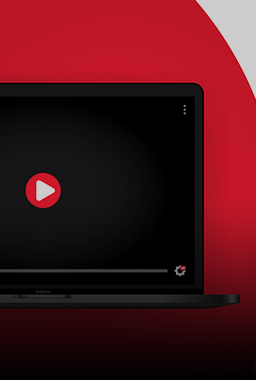
【富士通 社内実践】Anaplanで実現するWorkforce Planning (ショートバージョン) (YouTube)
【富士通 社内実践】Anaplanで実現するWorkforce Planning (フルバージョン) (YouTube)
Fujitsu Application for SAP® Solutions Detail Scheduling Template(生産計画)のご紹介
Enterprise Visualization ~変化に強いポストモダンERPとMES~
Fujitsu Die-Tech Corporation of the Philippines様導入事例対談動画
デジタルスレッドで ものづくり変革
製造DXを実現するものづくりクラスター
富士通の製造DXに向けた取り組み
統合計画管理ソリューションPROFOURS ~頼れる現場のパートナー~
食品製造業様向け統合計画管理ソリューション「GLOVIA smart PROFOURS」
計画業務パッケージ「GLOVIA smart PROFOURS」機能ご紹介
製造業向け統合計画管理システム「GLOVIA smart PROFOURS」
製造業向け統合計画管理システム「GLOVIA smart PROFOURS」
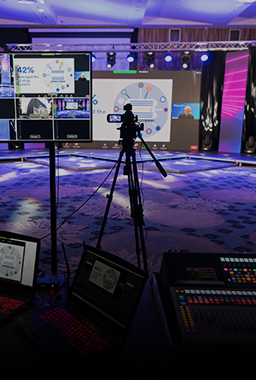
- 【開催終了】【Anaplan Connect 】変化に強いSCMの実現に向けて -東レ・メディカル様 調達計画における取組事例
- 【開催終了】【ET & IoT West 2022】製造現場における製造DX推進とは?
- 【開催終了】【NANO OPT Media Online (ナノオプト・メディア オンライン)】製造業におけるDX推進とは ? スモールスタートから始める製造DXの実現~Manufacturing DX Journey to the BEST~
- 【開催終了】Planning DX 2021|day2:Anaplan+ものづくり知見による製造DXへの貢献– 変化に強いSCM実現 –
- 【開催終了】SIEMENS Realize LIVE 2021 Japan ご案内(7月14日講演動画再配信中)
- 【開催終了】食品・化学・CPG産業様向けAIを活用した生産計画・製造実績管理ソリューション
- 【開催終了】<mcframe連携ソリューションセミナー>【販売・生産・調達の計画がつながる!】統合計画管理システム「PROFOURS」のご紹介
原価・生産管理の高度化オファリング
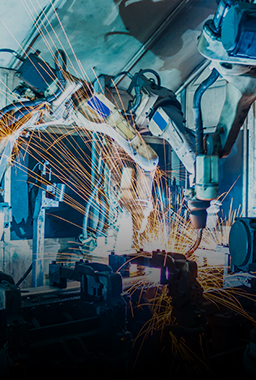
高度化オファリング
製品ページ
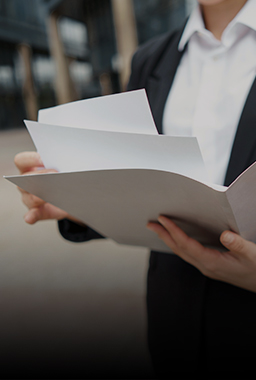
- 原価管理の高度化オファリングに関するご紹介資料一覧
- 生産管理の高度化オファリングに関するご紹介資料一覧
複数の並行して進行する企画、開発、投資プロジェクトの全てを管理するソリューション
SAP® Portfolio and Project Management(SAP PPM)SAP エンジニアリング製造実行システム(SAP S/4HANA® Manufacturing for Production Engineering and Operations(SAP PEO))
マスカスタマイゼーションを実現する構成管理ERPソリューション
Fujitsu Application for SAP® Solutions Mass Customization Template(SIEMENS連携)マス・カスタマイゼーションを実現する構成管理ERPソリューション
Fujitsu Application for SAP® Solutions Mass Customization Template富士通のSAP製造業ソリューション
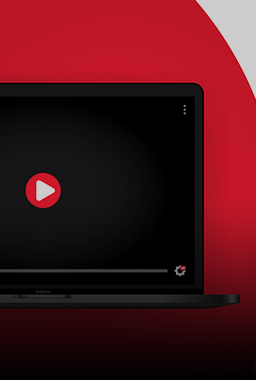
Enterprise Visualization ~変化に強いポストモダンERPとMES~
Fujitsu Application for SAP® Solutions Actual Costs Templateご紹介
デジタルスレッドで ものづくり変革
製造DXを実現するものづくりクラスター
富士通の製造DXに向けた取り組み
富士通の考えるマスカスタマイゼーション対応方法
産業機械製造業における Fujitsu Application for SAP® Solutions Mass Customization Templateの活用シナリオ
Fujitsu Application for SAP® Solutions Mass Customization Template~コンセプトのご紹介~
FUJITSU Application for SAP® solutions Mass Customization Template~見積管理ソリューション~
Fujitsu Application for SAP® solutions Mass Customization Template~手配管理ソリューション~
JSUG Conference2019 Fujitsu Speaker Message
「JSUG Conference2019」富士通セッションの講演者メッセージ
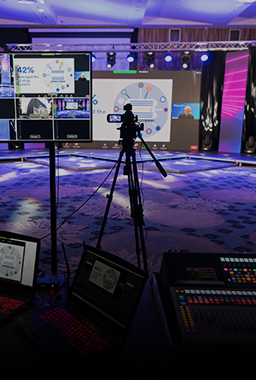
- 【開催終了】【NANO OPT Media Online】SAPを補完する原価テンプレートと製造実行MESシステムのご紹介
- 【動画配信終了】【製造業DX World Conference 2022】製造現場における製造DX推進とは?
- 【開催終了】【ET & IoT West 2022】製造現場における製造DX推進とは?
- 【開催終了】【NANO OPT Media Online (ナノオプト・メディア オンライン)】製造業におけるDX推進とは ? スモールスタートから始める製造DXの実現~Manufacturing DX Journey to the BEST~
- 【開催終了】SIEMENS Realize LIVE 2021 Japan ご案内(7月14日講演動画再配信中)
- 【開催終了】組立加工産業様向け マス・カスタマイゼ―ションを実現する構成管理ERPソリューション
製造実行管理の高度化オファリング
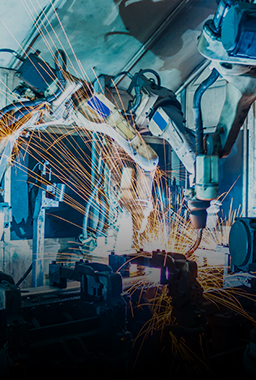
高度化オファリング
製品ページ
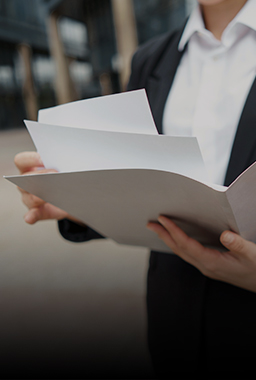
- 製造実行管理の高度化オファリングに関するご紹介資料一覧
SAP エンジニアリング製造実行システム(SAP S/4HANA® Manufacturing for Production Engineering and Operations(SAP PEO))
SAP製造実行システム(SAP® Digital Manufacturing(SAP DM))
製造DXを実現するものづくりクラスター
富士通のSAP製造業ソリューション
Siemens製造オペレーション管理システム Siemens Opcenter Execution Discrete
Siemens製造オペレーション管理システム Opcenter Execution Process (EX PR)
Siemens製造オペレーション管理システム Opcenter Execution Core
Fujitsu Engineering Operation and Production Management
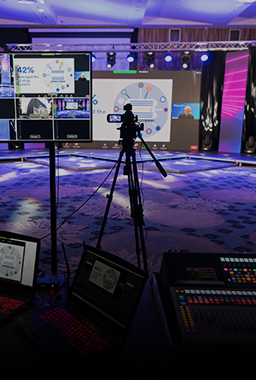
- 【開催終了】【NANO OPT Media Online】SAPを補完する原価テンプレートと製造実行MESシステムのご紹介
- 【動画配信終了】【製造業DX World Conference 2022】製造現場における製造DX推進とは?
- 【開催終了】【ET & IoT West 2022】製造現場における製造DX推進とは?
- 【開催終了】【NANO OPT Media Online (ナノオプト・メディア オンライン)】製造業におけるDX推進とは ? スモールスタートから始める製造DXの実現~Manufacturing DX Journey to the BEST~
- 【開催終了】低収益のアナログ工場から脱却!最短3カ月から始めるクラウドMESを活用した製造DXアプローチ
- 【開催終了】スモールスタートから始める製造DXの実現 - 製造DXのビジョンを元に推進する製造現場DX化へのStep-by-Stepアプローチ
お客様の声
富士通の製造DXに向けた取り組み
SDGsへの取り組み
当社はDX企業として2021年4月、社会課題を起点にお客様と共に成長を加速していくための7つの重点注力分野を発表し、その中の1つに、Sustainable Manufacturingという、循環型で持続可能なものづくりの実現に向けた取り組みをご提案しております。 この循環型で持続可能なものづくりの考え方は、エコシステムによるSDGsの達成に向けた取り組みへも通じてます。
将来の不確実性やニーズの多様化への対応など、ものづくりのソリューション提供に活かしていくことが富士通の使命です。
富士通のケーパビリティ
富士通は、自らがものづくりDNAを持った製造業の一員であるノウハウ・強みをもとに、豊富なリファレンスをもつ業務領域(製造現場向けの業務改善)において、“ものづくり知見”を生かしてお客様に貢献します。
- 製造業ならではのノウハウ
国内20ヶ所以上 - ものづくり(設計~生産~実績)
業務アプリケーションを自社開発
国内唯一ベンダ - ものづくり系ソリューションの
提供実績
10,000社以上
富士通の製造業ソリューションに関するお問い合わせ
当社はセキュリティ保護の観点からSSL技術を使用しております。
お電話でのお問い合わせ
0120-933-200
(通話無料)
受付時間:平日9時~17時30分(土曜・日曜・祝日・当社指定の休業日を除く)