- 富士通の製造業
ソリューショントップ - ECMオファリング
- 設計の高度化オファリング
- Fujitsu Development Management for Manufacturing
- Fujitsu MBSE/MBD/CAE Solutions
- Fujitsu 設計製造支援 iCAD Solutions
- NX™ software
- Solid Edge® software
- Teamcenter® software
- Fujitsu Manufacturing Industry Solution COLMINA 技術情報管理 部品表
- Fujitsu Manufacturing Industry Solution COLMINA 製品含有化学物質管理
- Fujitsu Manufacturing Industry Solution COLMINA Design Review 高速リモートデスクトップ
- Fujitsu Product Development Process Management
- 生産準備の高度化オファリング
- Fujitsuデジタル生産準備 VPS
- Fujitsu Engineering Operation and Production Management (EOPM)
- Fujitsu Manufacturing Industry Solution COLMINA 技術ファイル管理 for Manufacturing
- Fujitsu Product Development Process Management
- 製造データ利活用の高度化オファリング
- Fujitsu Manufacturing Industry Solution COLMINA 設備点検
- Fujitsu Manufacturing Industry Solution COLMINA 設備保全管理 PLANTIA
- Fujitsu Product Development Process Management
- 関連オファリング
- SCMオファリング
- 導入事例
- エンジニアリング製造実行ソリューション(SAP S/4HANA® Manufacturing for Production Engineering and Operations(SAP PEO))
- SAP製造実行システム(MES)
- Fujitsu MES Solutions
(旧名称:FUJITSU Manufacturing Industry Solution COLMINA MES)
- Fujitsu Die-Tech Corporation of the Philippines様導入事例対談レポート(PDF)
- Fujitsu Die-Tech Corporation of the Philippines様導入事例対談動画(YouTube)
- 株式会社東振精機様(PDF)
- リスパック株式会社様(PDF)
- ゴールドパック株式会社様(PDF)
- 富士通株式会社(PDF)
- Anaplan
- Fujitsu Die-Tech Corporation of the Philippines様導入事例対談レポート(PDF)
- Fujitsu デジタル生産準備 VPS
- カタログ
- 設計の高度化オファリングに関するご紹介資料
- Fujitsu Development Management for Manufacturing
- Fujitsu 設計製造支援 iCAD Solutions
- Fujitsu MBSE/MBD/CAE Solutions
- 生産準備の高度化オファリングに関するご紹介資料
- 計画の高度化オファリングに関するご紹介資料一覧
- 原価・生産管理の高度化オファリングに関するご紹介資料
- 生産管理の高度化オファリングに関するご紹介資料
- 製造実行管理の高度化オファリングに関するご紹介資料
- 動画(YouTube)
- 計画の高度化オファリングに関する動画(YouTube)一覧
- Enterprise Visualization ~変化に強いポストモダンERPとMES~
- Fujitsu Die-Tech Corporation of the Philippines様導入事例対談動画
- デジタルスレッドで ものづくり変革
- 製造DXを実現するものづくりクラスター
- 富士通の製造DXに向けた取り組み
- 統合計画管理ソリューションPROFOURS~頼れる現場のパートナー~
- 食品製造業様向け統合計画管理ソリューション「GLOVIA smart PROFOURS」
- 計画業務パッケージ「GLOVIA smart PROFOURS」機能ご紹介
- 製造業向け統合計画管理システム「GLOVIA smart PROFOURS」
- 製造業向け統合計画管理システム「GLOVIA smart PROFOURS」
- 原価・生産管理の高度化オファリングに関する動画(YouTube)一覧
- Enterprise Visualization ~変化に強いポストモダンERPとMES~
- Fujitsu Application for SAP® Solutions Actual Costs Templateご紹介
- デジタルスレッドで ものづくり変革
- 製造DXを実現するものづくりクラスター
- 富士通の製造DXに向けた取り組み
- 富士通の考えるマスカスタマイゼーション対応方法
- Fujitsu Application for SAP® solutions Mass Customization Template
- Fujitsu Application for SAP® solutions コンセプトのご紹介
- 見積管理ソリューション~見積業務がこんなに簡単に!
- 手配管理ソリューション~手配業務がこんなに便利に!
- 産業機械製造業における活用シナリオ
- JSUG Conference2019 Fujitsu Speaker Message
- 「JSUG Conference2019」富士通セッションの講演者メッセージ
- 製造実行管理の高度化オファリングに関する動画(YouTube)一覧
- ニュース&イベント
自動車や建築、鉄道関連向けの防音材、制振材、シーリング材の開発・製造・販売を手がけるイイダ産業株式会社様では、2018年に富士通の「COLMINA MES」を導入しました。そこでイイダ産業の代表取締役社長である飯田耕介氏と生産管理部の水谷真也氏、中川健氏、経営企画部の青山航大氏の3人に、導入をサポートした富士通株式会社の吉田直樹と、富士通シニアエバンジェリストの武田幸治が現場での生の声を取材しました。
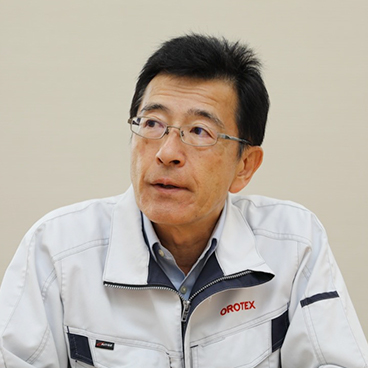
新しいことをやっていかなければ業績は伸びません。当社の製品開発では、常に「何か新しいことをやらなければいけない」という意識があります。
イイダ産業株式会社 代表取締役社長
飯田耕介氏
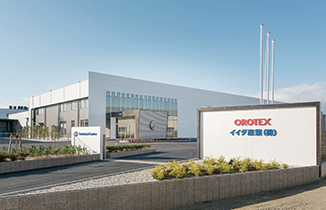
0
出荷遅延件数
160
月の作業削減時間
- 業種: 製造業
- 場所: 愛知県稲沢市
- Customer's website
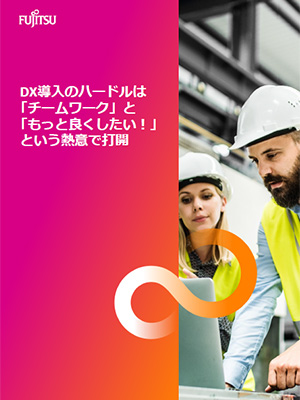
PDF資料ダウンロードで、もれなくプレゼント
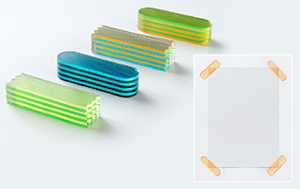
貼ってはがせるジェルテープ(12枚入り)をプレゼント
新しいものを取り入れなければ生き残れない
今回訪れたのは、愛知県稲沢市にあるイイダ産業株式会社です。同社には第一工場のほか、同市内に3つの工場とテクニカルセンターがあります。まずはDX化推進を決断した同社代表取締役社長の飯田耕介氏に、「COLMINA MES」の導入までの背景や会社としての新技術に対する姿勢、そして今後の展望についてお聞きしました。
武田:社長が今回DX化に取り組んだ背景や思いについてお聞かせください。
飯田氏:常に新しいことをやっていく、新しいことに挑戦していくという姿勢につきますね。既存品はどんどん値下げしていかざるを得ないですし、周囲との競争も激しくなっていきます。新しいことをやっていかなければ業績は伸びません。当社の製品開発では、常に「何か新しいことをやらなければいけない」という意識があります。今回はシステム導入ということですが、具体的に「何をやるか」は、担当者たちがいろいろと考えてくれました。
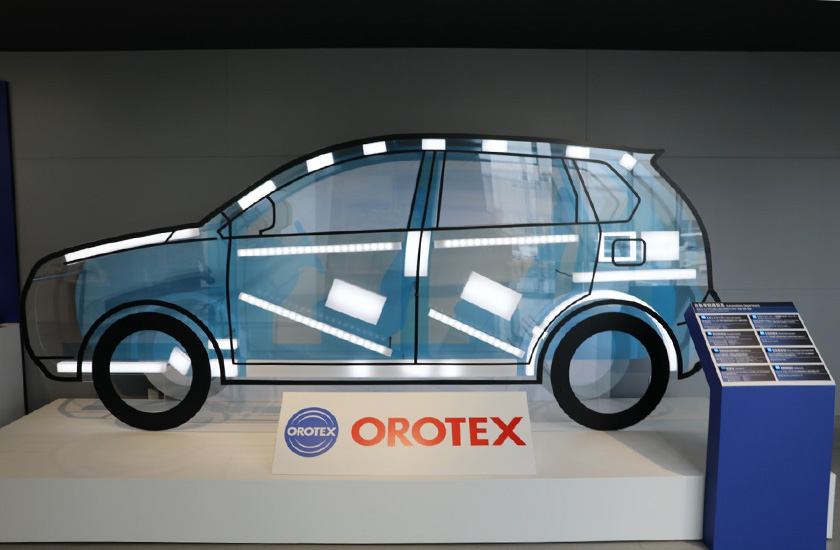
武田:DXは大企業がやるものという意見も多いですし、ゴールが見えないからやりにくい、予算が取りづらいという話もよく聞きますが、その辺りはどのように判断されたのでしょうか。
飯田氏:詳しいことは後で3人の担当者に聞いて欲しいのですが、私自身は当然DXに詳しくないですし、どんなことでも「やれ」とはいいません。確かに期限が見えない、予算が分かりにくいという側面はありますね。特に今回の目的は業績を伸ばすためではなく、社内的なコストを下げる目的でしたから企業規模に関係なくやるべきことだと思っています。競合他社も取り組んでいるだろうし、負けないためには自分たちもやっていかないと世の中についていけないのではないでしょうか。
武田:DXに限らず、新しいものは積極的に取り入れることを社長ご自身が心がけているのでしょうか。
飯田氏:DXについては、当社はプロジェクトチームを立ち上げ、元々システム部隊もあったので、予算も含めて彼らに任せました。もちろん私も勉強はしています。セミナーや展示会に出かけて新しいことは勉強し、常に興味・関心を持つように心がけています。例えば最近はChatGPTも勉強していますよ。ただ、実際に導入するかは別です。私は好奇心旺盛ですが慎重な部分があるので、友人や経営者仲間の事例などを聞いて、実際の良し悪しをリサーチしてから必要なら取り入れます。
武田:社長と社員の方々の間に強い信頼関係を構築する社風はどのように築かれているのでしょうか。
飯田氏:当社では企業理念、行動規範として「愚直に感性豊かに元気よく」と掲げています。社員には「仕事以上に一生懸命になれるものがないと務まらない」とよく話しています。私自身、合気道や少林寺拳法を長くやっていますが、力のぶつかり合いではなく上手に「かわす」、「流す」といった物事への向き合い方、考え方が仕事にも活きています。さまざまな考え方を理解し、人とは違う考え方で相手を制すわけですが、仕事でそのような発想を活用できるようになりますね。
武田:もの作り企業としてこれからどのように対応していこうとお考えでしょうか。
飯田氏:自動車はさらに伸ばしていきたいですし、建材は建材で、第二の柱じゃないですけど、もっと拡大していきたいと思っています。自動車の方はEVになると、今までエンジン音で目立たなかった異音が余計に聞こえるようになるので、当社の防音材や制振材は、ますます必要とされるビジネスチャンスだと捉えています。30年前は「こんな製品を作れない?」とお客様からご要望をいただくことも多かったのですが、今は自分たちで探すしかありません。そういう中でさまざまなエッセンスを集め、仮説を立て、組み立て、それを作って形にして、フィードバックしていく。常に手探りで泥臭いやり方で愚直に進んでいくしかないと思います。
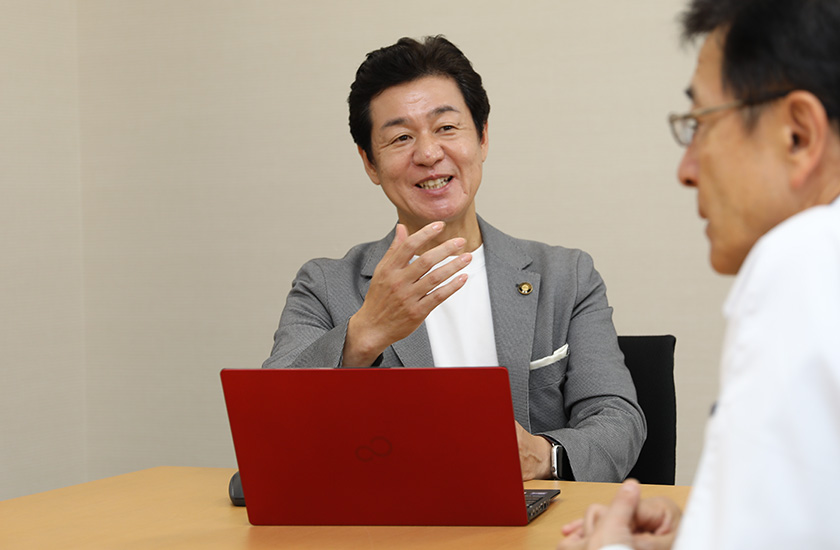
風通しの良い社風こそDX導入の大きな土台に
続いて2018年のDX導入時に現場でシステムを運用した、イイダ産業株式会社 生産管理部の水谷真也氏、中川健氏、経営企画部の青山航大氏の3人からDXを導入する上での自社の強みや導入に際して学んだこと、苦労したことなどをお聞きしました。
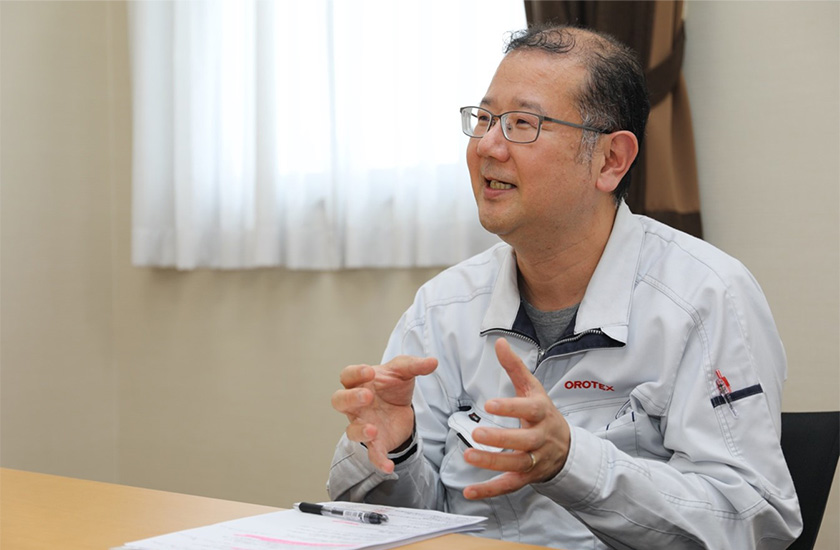
武田:ではDX導入について具体的なお話を実際に現場で動かれている3人にお伺いしたいと思います。皆さんは主に生産管理やシステム導入などをされていると伺っていますが、仕事をする上で、どんなことを大切にされているのでしょうか。
水谷氏:私は生産管理なので俗にいう「QCD」を最も大切にしています。特にお客様に対して納期遅れが起こらないよう、日々管理することを重視しています。
中川氏:私もQCDを意識しつつ、1つプラスするなら「時間短縮」を意識しています。そしてマンパワーの削減についても考えながら仕事をしていますね。
青山氏:私は会社のシステムを預かっているので、システムを止めないことやバックアップ体制を整えておくこと、仮に止まっても最短で復旧させることを重視しています。
武田:実際のところ、納期を含めQCDの実践はうまくいっているのでしょうか。
水谷・中川氏:自分たちはできていると思っています(笑)。
青山氏:私は逆にまだまだだな、と思っています。
武田:実際に現場で働いている3人から見て、貴社の強みはどんなところだと思われますか?
水谷氏:当社は製造業ですが、小回りの利く対応ができるのが強みだと思います。例えば車なら、急に何かのトラブルが起こった場合、すぐに設計し直してものを作れる体制があるのは強みだと思います。
中川氏:アットホームで風通しの良い会社なので今、水谷が話していたような小回りの利いた動きができるのだと思います。
青山氏:確かに社内では私のように直接製品に携わっていない社員の声もしっかり聞いてくれますし、裁量権や決裁権も与えてくれて、社長との距離も非常に近いので仕事がしやすい社風が強みだと思います。
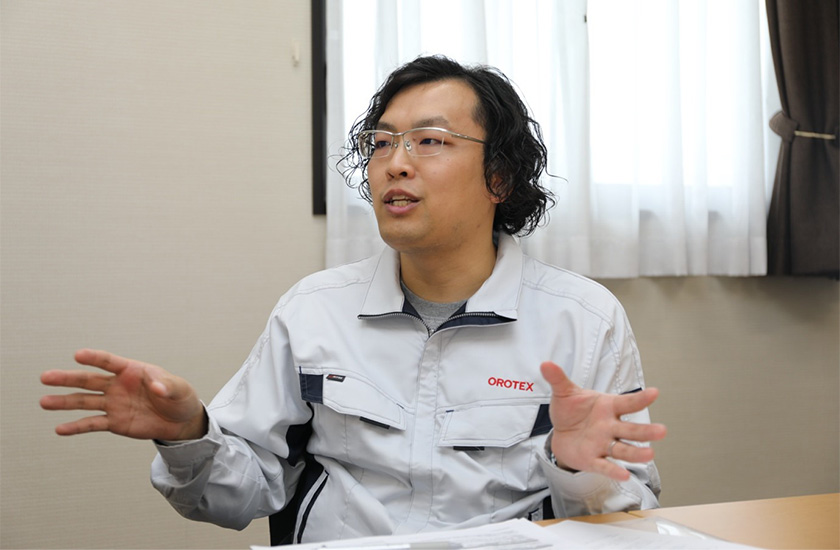
DXの導入、まずは国内外自社工場からスモールスタート
武田:MESを導入した話に移っていきたいのですが、DXシステムを導入しようと考えた経緯を教えていただけますか。
水谷氏:背景として、2016年頃から当社の子会社(タイ)と日本とでほぼ同時にシステムを導入するという話が上がっていました。ものが入ってくる「材料受入」と「製品出荷」のところにシステムを入れようという話です。タイでは2017年に入出庫システムを入れることができて、その効果が分かりました。タイで入れたシステムを日本で横展開できるかといえば、そう簡単な話ではありませんでした。日本ではタイよりも扱う材料や製品数が多く、複雑な状態でした。そこで会社から「しっかりと予算をつけるから改善するように」というミッションを与えられ、「物流プロジェクト」が立ち上がりました。最初は本当に手探りで展示会や勉強会に参加して情報収集をするところからスタートしました。
武田:いろいろなベンダーさんともお話をされたのでしょうか。
水谷氏:はい。いろいろなベンダーと打ち合わせを重ねる中で「予算内で」、「一番困っていることが解決できて」、「効果が大きいもの」に決めよう、という方向性が決まりました。当社では直接製品になるものはほとんど困っておらず、それよりも半分製品化して、それを外部に委託したものについて、管理の工数が非常に複雑だという課題も改めて明確になりました。
中川氏:補足すると、外部に委託した製品が今、どういう状態なのか、リアルタイムで把握できていませんでした。ですからどこから手をつけて、どこをデータ化すればいいのか、どこを在庫化すればいいのかというところも手探り状態で、本当に雲をつかむような状態でした。
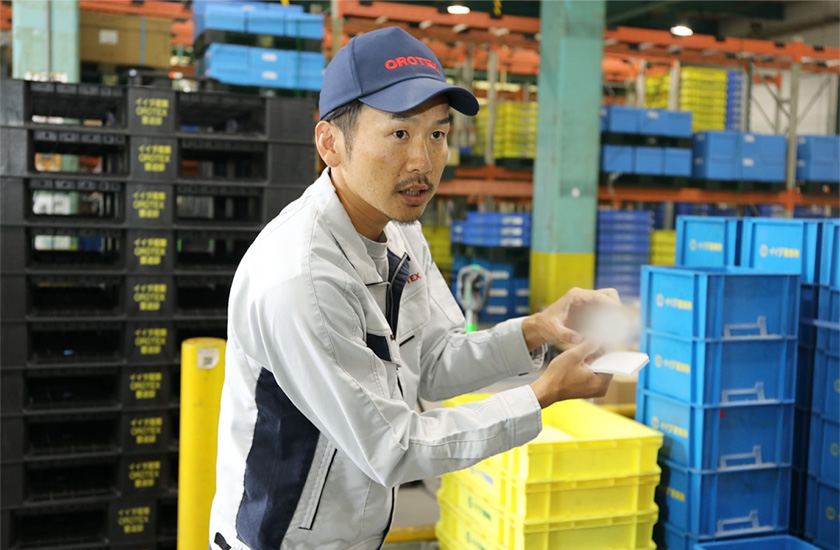
水谷氏:いろいろなベンダーさんと話をしても、正直、こちらのやりたいことがうまく伝わらなかったり、話がかみ合わなかったりで、なかなかシステムの導入には至りませんでした。そんなときに、富士通さんから「フリーコンサルで作業を見ます」、「何に困っているのか一緒に探りましょう」とご提案いただき、実際に中に入ってもらって業務の全行程を見ていただきました。そして「イイダさんなら、MESというシステムを入れて在庫管理すれば、課題が解決できるはずです」とおっしゃっていただき、それに納得できたので2018年3月に導入となりました。
DXへの拒否感はプロジェクトチーム自らが学ぶ姿勢で打開
武田:私たちがお客様からよく聞かれるのが「具体的にDXをどうやって進めるのか」ということです。例えば生産管理部門と情報システム部門では見方が違い、改善したいポイントも異なると思いますが、そんな中で優先順位づけはどのように行なったのでしょうか?
水谷氏:物流プロジェクト立ち上げ時のメンバーは4名で、とにかく話し合いを重ね、一番時間がかかっている「外部委託者の管理」と、できていなかった「受け入れ品の現物チェック」を優先的に片付けようと決めることができました。もちろん誰に相談していいかも分からず、自分たちでやっていたので大変ではありました。
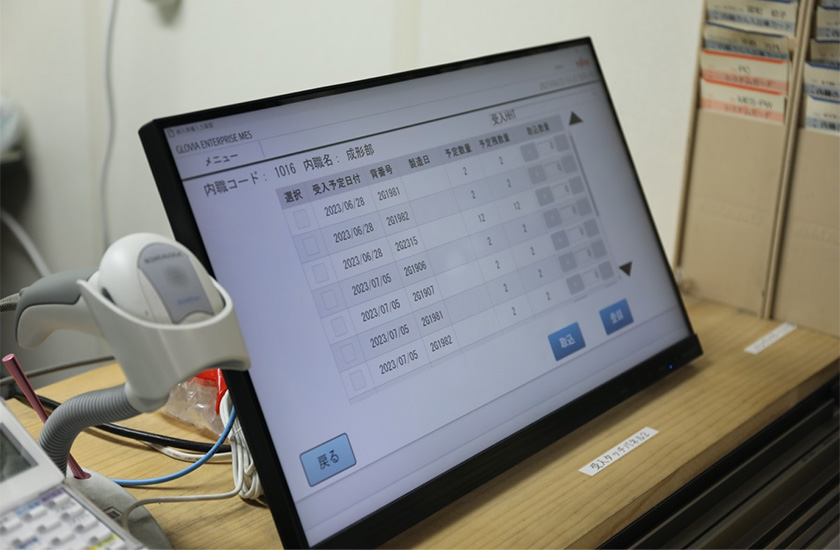
武田:システムをインストールしてからのお話もお伺いしたいのですが。
青山氏:私は導入検討のメンバーではなく、インストールの直前にアサインされたのですが、水谷が当時、管理者の立場でありながら、実際に現場に降りて新しいシステムの使い方を一から学び直している姿を見て、またそれを中川などほかのメンバーも目にして、皆でそうやって学びながら進めていったことがとても印象に残っています。
吉田(富士通):導入初日に水谷さんがシステムを使えず、私自身「人員を増やして欲しい」とお願いしてしまったのですが、翌日にはもう別人のようになっていて、前日にできなかったことがすべてできるようになっていたことは、本当にすごいと思いました。私もそのような努力する姿が社内に広まったと思います。
武田:私たちはスモールスタートという言葉を使っていますけど、そこからどんどんカスタマイズして、自分たちのものにするまでにはどんなご苦労がありましたか?
水谷氏:やはり、物流プロジェクトのメンバー以外は新しいことに対する抵抗感があったと思います。それを説得するのは苦労しました。
武田:そういった周囲の新しいものに対する拒否感をどう乗り越えていったのですか?
水谷氏:「DXをやると、こういうことが良くなる」、「今より良くなる」と、どんどんアピールしました。とにかくメリットをひたすらアピールして受け入れてもらえるように努力しました。
中川氏:私は対社内より、システム構築のオーダーの方が大変でした。例えば、結構考えて作ってもらったタッチパネルでも実際の運用ではうまくいかなかったり、データの抽出も実際にやってみると足りていない部分が出てきたり。いかに結果を想定してシステム構築を依頼するかが一番苦労しました。富士通さんには改善を重ねていただき、その最中にもいろいろな意見も出てきますので、それを集約しながら進めていますね。
青山氏:私はやはり現場からの声が一番多く寄せられる立場なので、いかに現場の意見に寄せるか、ということに苦心しました。それとシステム導入によって、現場からはカスタマイズのスピード感を求められるようになりました。
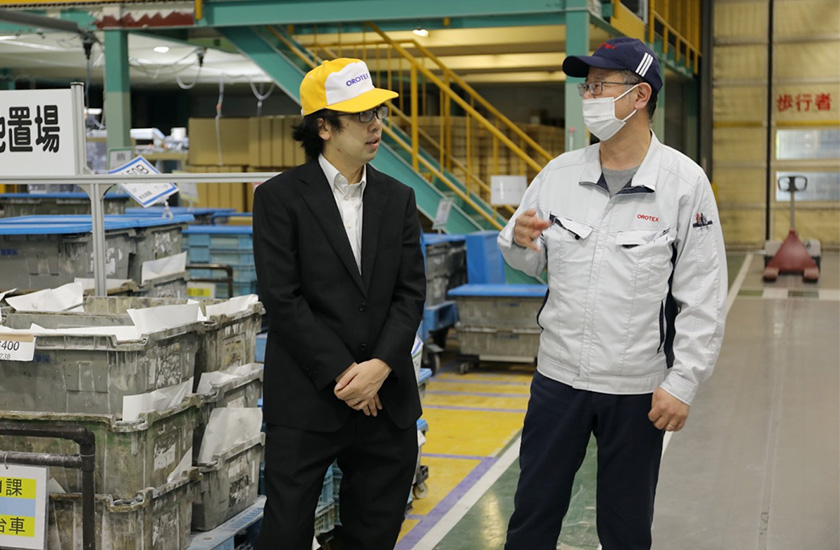
DX導入後、働き方改革の実現に
武田:プロジェクトの現体制と今後の推進計画についてもお聞かせください。
水谷氏:最初は半製品の在庫が分かるようにして、次に製品の在庫がMESで分かるようにしました。今年は生産計画を立てるところまで。その後は副資材などに展開し、将来はそれを生産計画や出荷計画のところまでつなげたいというビジョンがあります。それを富士通さんと一緒に毎年少しずつ進めていければと考えています。
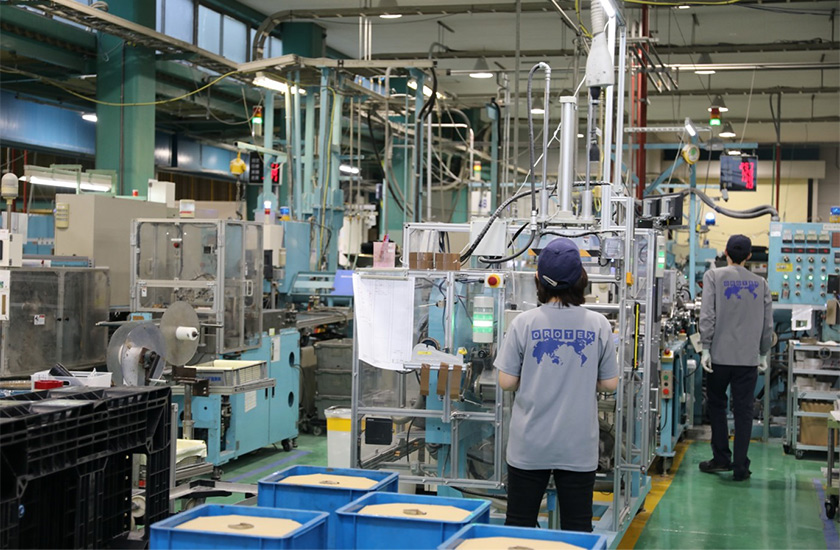
武田:導入して実際に得られた効果についてもお伺いしたいです。
水谷氏:まず在庫管理の精度が格段にあがりました。例えば外部委託者の場合、受け入れ作業の入力もなくなり、人的ミスによる出荷ミスが大幅に削減できました。製品のチェックもできるようになり、間違いや出荷遅延もなくなりました。MESを導入したことで外部委託者との伝票を廃止し、自動レシートが出るようにしました。月締めのときは請求書が1枚出てきて、それで間違いなくやれるようになりました。
武田:システム担当者の視点ではいかがでしょうか。
青山氏:元々情報がなかったところからスタートしていますが、DXによって情報が出来上がっているおかげで、どの半製品がどこにあるかなど、問い合わせの内容についてすぐに提示できるようになりました。製品の状態はこうですよ、と即時にリストアップできるなど、情報化されていることでさまざまなニーズに応えられるようになりました。
武田:富士通側として感じている効果や手応えはありますか?
吉田(富士通):2018年当時、水谷さんは本当にお忙しそうでしたが、今はもう残業せずに帰られていると聞いて、MESが入って水谷さんのお役に立てているのかなと感じます。
水谷氏:私だけでなく、部下たちも助かっていますよ。さまざまなことが数値で可視化されるようになり、結果として働き方改革というところまで効果が波及しています。
武田:今後の展望についてもお聞かせいただけますか。
水谷氏:まずはMESの在庫を使って「計画指数」を出す改善をします。さらにそれを製品だけではなく、副資材とか原材料にも展開していき、最終的には受け入れから出荷までの「完全見える化」を計画しています。それに必要な基幹システムなども富士通さんにあると思いますので、それらを活用しながらDX化を進めていきたいですね。
中川氏:水谷と同じイメージで、入ってくる副資材や原材料なども一元管理し、そこからさまざまな自動計算ができることが理想です。そして誰がやっても同じ数字が出るシステムに育てていきたいですね。そうなれば需要予測などにも対応し、より正確に前もって動けるようになります。特に自動車業界では「内示」と呼ばれる予定数がありますが、どうしても人の感覚頼りなので、この辺りもDXで可視化し本当に必要最低限の在庫で回せるシステムにしたいと考えています。
青山氏:私は情報化や数値化、データ化、可視化できるようになった成果をいかに利用者が見やすい形にするのか、スピード感を持って対応したいと考えています。そうなるとBIツールまでいくのかなと思っています。
「もっと良くしたい!」という熱意が新しいものへの抵抗感の払拭に不可欠
武田:デジタル化推進について「二の足を踏んでいる」方へのアドバイスをお願いします。
青山氏:今までのやり方とデジタルでは、ギャップが大きいので勉強は必要でしょう。水谷もまったくできなかったところから使えるようになるまで勉強する姿は、周囲に大きな影響を与えたと思います。
中川氏:まずはやってみることですね。抵抗や怪訝、不信といった批判的な意見は必ず出ますが、それでもやってみることで結果が出ますので、そこを見せていくことが大切です。
水谷氏:新しいことに挑戦する抵抗感をなくすのが一番大変ですね。どうしても今までのやり方が一番だし、何かを変えるには、それなりの労力がかかりますので、それを超える力が必要です。その力は「もっと良くしよう、良くしたい!」、「後輩たちに良いものを残したい!」という熱意ですね。
武田:では最後に富士通に期待することを教えてください。
中川氏:私は提案していただくことが本当に嬉しいです。このシステムでほかにどんなことができるのか、分からないことも多くあります。「こんなことできますか?」、「あんなことできますか?」とこちらから質問することも大切ですが、何か提案していただけるとすごく助かります。
青山氏:最初のコンサルではこちらのボトルネックをピンポイントで見つけていただきました。まだ残っている課題をぜひ見つけていただいて、1つずつ改善していけるようなご提案があるとありがたいです。
水谷氏:自分が今回システムの導入に携わってから富士通側は吉田さんがメインで担当してくれましたが、的確なアドバイスがあったからこそ今までお付き合いさせていただいています。やはり自分たちでは気づけないこともありますので、これからも並走していただければと思います。
武田:ありがとうございます。今いただいたコメントを持ち帰りきちんと精査したいと思います。
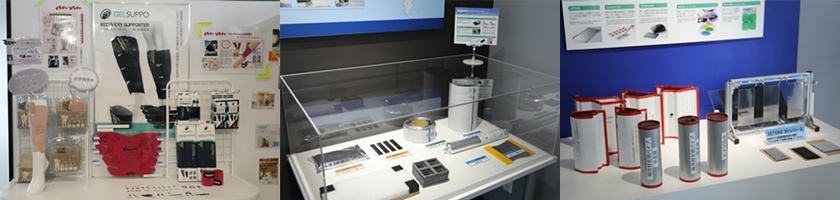
[ 2023年10月掲載 ]
わたしたちと製造実行管理の高度化を実現しませんか?
無料カタログのダウンロードはこちらから
-
製造現場を見える化し、課題を解決する富士通のソリューションのカタログのご請求はこちらから。
カタログをダウンロードされた方には、オンラインイベントや製造業向けSCM/ERP/MESソリューションに関するお得な情報をご紹介します。
富士通の製造業ソリューションに関するお問い合わせ・ご相談
当社はセキュリティ保護の観点からSSL技術を使用しております。