Shift to a New “Monozukuri” Style Appropriate for the Design Environment of the “New Normal” Era
Release date: June 30, 2021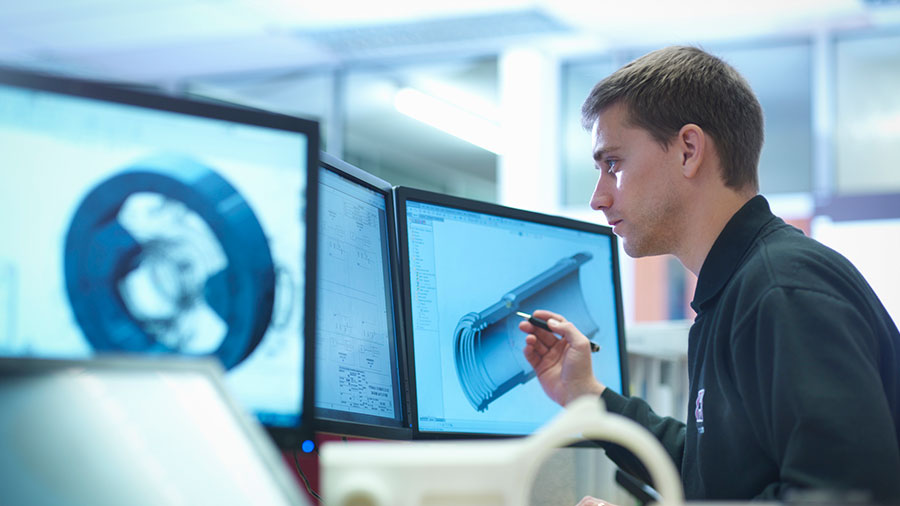
The COVID-19 pandemic has accelerated the shift to telework at many businesses. Design and development departments, which play an important role in monozukuri (manufacturing), are no exception and face various problems due to restrictions on the movement of employees and the necessity of telework. This article introduces Fujitsu’s in-house practices for realizing a remote environment and the high-speed display technology Remote Virtual Environment Computing (RVEC) used in these practices, along with a proposal for a shift to a new style of “monozukuri” using 3D models.
- 1. Introduction
- 2. Issues in switching to telework at design and development sites at Fujitsu
- 3. Toward overcoming issues in remote design environments
- 4. Toward a smooth communication environment
- 5. Toward the realization of a new style of monozukuri
- 6. Conclusion
1. Introduction
Owing to the COVID-19 pandemic, telework is becoming established as a new work style in the “new normal” era. Telework was originally promoted with the aim of “securing a workforce” and “increasing labor productivity” in an aging society with a declining birthrate. Today, however, the work style is changing from the “collective style” of work at the office to the “distributed style” where each person chooses where to work. Moreover, the lifestyles of employees are also changing, and telework is becoming increasingly common. These changes can also be seen in the manufacturing departments in charge of “design and development”, and there is a pressing need to resolve the issues presented by remote environments.
This article introduces Fujitsu’s efforts to realize a secure and stress-free remote environment and a smooth communication environment for the design and manufacturing processes that are important for monozukuri, based on Fujitsu’s internal practices, and introduces the high-speed display technology and similar 3D shape search technology that support these efforts.
2. Issues in switching to telework at design and development sites at Fujitsu
This section describes issues in switching to telework at design and development sites.
2.1 Identification of issues in switching to telework
Fujitsu has launched “Work Life Shift” as a concept of a new way of working in the new normal era. Employees were given questionnaires and interviews with the aim of sincerely addressing and responding to the voices of workers in the process of implementing reforms.
At manufacturing departments, issues were found at various levels in promoting telework and remote operations in design and manufacturing sites.
2.2 Issues related to remote work environments
Questionnaires and interviews with employees made it clear that there are various issues in each process, from conceptual design to detailed design, production equipment design, and manufacturing. Among other things, the respondents indicated that “3D data cannot be viewed due to poor Virtual Desktop Infrastructure (VDI) response,” “data cannot be accessed safely from the outside due to security reasons,” “on-premise systems in the office cannot be used,” “home PC specifications are low,” and “downloading takes time.”
2.3 Communications-related issues
As telework spread, various issues came into view. Communications-related issues were found to be particularly numerous. These included things such as “it’s hard to ask questions casually like in the office,” “it’s hard to change the topic during online meetings,” “it feels like people just talking one way,” “the lack of back-and-forth exchanges is unsettling,” and “there’s no sense of unity in the organization.”
1) Changes in communication culture
Japan is one of the most high-context communication cultures in the world, relying on the context of shared knowledge, experiences, and values fostered by being in the same place and time. However, the change from the traditional collective way of working to the distributed way of working through telework is causing a shift from context-dependent communication to a language-dependent, low-context culture.
2) Monozukuri in a low-context culture
Monozukuri through feedback-rich, fine-grained teamwork, which is one of Japan’s strengths, is premised on high context.
However, in the new normal era, monozukuri in a low-context culture requires a new efficient communication environment that minimizes miscommunication.
3. Toward overcoming issues in remote design environments
This section describes Fujitsu’s proprietary high-speed display technology that solves the various issues in remote environments for design and manufacturing sites described in the previous section.
3.1 Technology for stress-free image display
By using Fujitsu’s proprietary high-speed display technology (RVEC: Remote Virtual Environment Computing) [1], which has a proven track record at Fujitsu’s in-house design departments, on-premise systems can be used remotely without stress.
One way to reduce latency during remote image display is to reduce the image quality of the entire image, but this does not allow high-quality image transfer. By contrast, RVEC’s original compression technology identifies areas where screen updates occur frequently at high speed and performs video compression with a high compression rate in those areas, as shown in Figure 1. For other areas where screen updates are infrequent, still images are compressed to reduce the processing load on the server-side, and images are transferred only when the screen changes, thereby achieving high-speed display as a whole. Compared with other image transfer technologies, this technology reduces bandwidth consumption to about 1/6 to 1/10, as shown in Figure 2.Moreover, by optimizing video compression to the images of design tools, it enables image transfer while maintaining high image quality, and by reducing the amount of image transfer required and the number of transfers, it eliminates unnecessary processing and improves response. This enables remote display of high-quality images with high response time. In remote environments that use RVEC, operations such as rotation, enlargement, and part placement of the 3D models can be done smoothly with a high degree of responsiveness. By providing a CAD environment that does not interfere with the designer’s thinking, high design efficiency can be maintained even in the new normal era of telework.

Figure 1 Outline of RVEC compression technology.
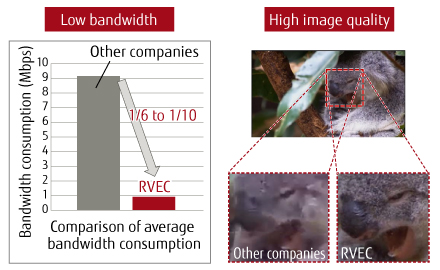
Figure 2 Effectiveness of RVEC.
3.2 Support of 4K through continuous performance improvement
Fujitsu pursues technology innovation for continuous performance improvement of RVEC as shown in Figure 3 in order to successfully meet conflicting requirements for high image quality, low bandwidth, and low latency. Along with making this RVEC technology, which has been under development since 2012 to consolidate in-house design environments in the cloud, work for an increasing number of use applications, Fujitsu has been working to make it support video compression standards with higher compression rates while increasing its performance for environments with high network latency. The 2021 GPU version has achieved sufficient performance for 4K images through GPU offloading to reduce the CPU load while also reducing the bandwidth.
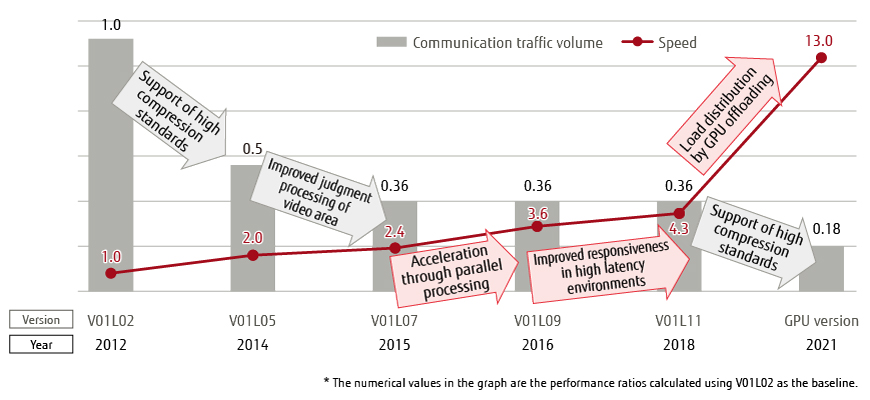
Figure 3 Efforts to improve the performance of RVEC.
4. Toward a smooth communication environment
This section describes a smooth communication environment using 3D models for communication among related parties such as participants performing design reviews as part of design work.
By introducing an information sharing mechanism using 3D models, it will be possible for multiple parties to share product images and communicate smoothly. Some examples of Fujitsu’s efforts and the technologies for utilizing the collected information are presented below.
4.1 Example of information sharing centered on 3D models
This section describes an example of Fujitsu’s efforts and technologies for communication using 3D models.
1) Design review between multiple departments using 3D models
Figure 4 shows an example in which related departments such as design, quality assurance, manufacturing, and maintenance use 3D models to conduct design reviews and share the findings gained therefrom as knowledge, in order to improve product quality before trial production.
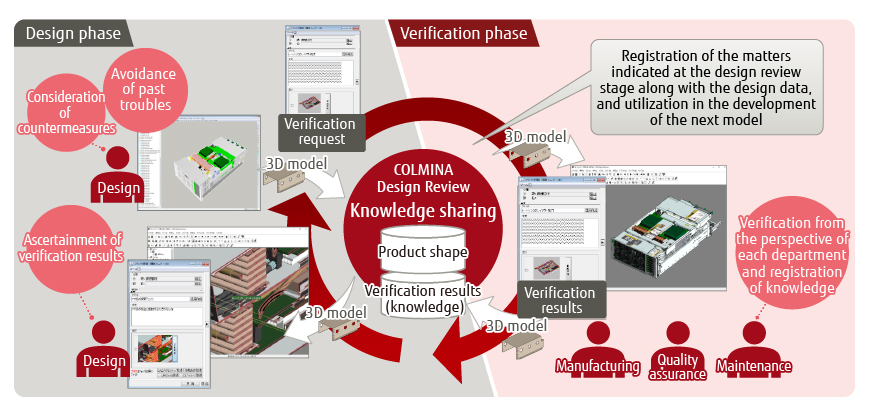
Figure 4 Example of design review between multiple departments using 3D models.
In this example, the cycle starts with a verification request from the design department. The related divisions perform verification from their respective perspectives, and the design division then makes changes accordingly and notifies the related department about the results. The information generated in each related department during this cycle is linked with the 3D model and shared as knowledge, which will be utilized in subsequent development work.
In this example, “FUJITSU Manufacturing Industry Solution COLMINA Design Review, Knowledge Sharing” is used as the mechanism for knowledge sharing.
2) Successful shortening of the development period by 25%
In the past, when indicated matters such as suggested changes or concerns were communicated to the designer as a result of the verification in the form of text or images, the designer had to identify the indicated parts of the product while manipulating the 3D model before considering how to respond.
In this example, we were able to reduce the development time by 25% by linking the indications with the 3D model, which allowed us to start considering how to respond immediately and thoroughly verify the results on a virtual machine. Further, by utilizing past knowledge, we were able to reduce the number of serious indications, such as requests for design changes, that could cause major rework after the prototype was manufactured.
4.2 AI-based similar 3D shape search technology
This section describes the search technology that efficiently utilizes the information linked with the 3D model, introduced in the previous section.
Linking information with a 3D model makes it possible to search for information related to a selected 3D model without having to memorize keywords. However, since the shapes of parts change product by product, a function to search for similar shapes is required instead of searching for the same shape.
Fujitsu has developed a proprietary similar 3D shape search technology [2] for finding similar 3D models using AI. Technology to search for 3D models based on shape similarity has been under development since 2008, but as shown in Figure 5, the search accuracy of the conventional algorithm-based method without AI varies greatly depending on the shape of the part, and there was the problem that a new algorithm had to be developed each time a part that could not be successfully searched was found. The introduction of AI in 2017 did reduce shape-dependent variations in search accuracy, but the search accuracy using only AI in the public domain was only on the order of 60%, which was not satisfactory. Therefore, we developed a proprietary technology for the generation of images from 3D models for AI training that do not cause data set quality degradation when repeatedly used for learning. In addition, various tunings were added to the Deep Learning neural network, including setting the number of layers in the middle layer to obtain optimal accuracy. The result was similar 3D shape search technology that achieves a high search accuracy of about 90% regardless of shape type.
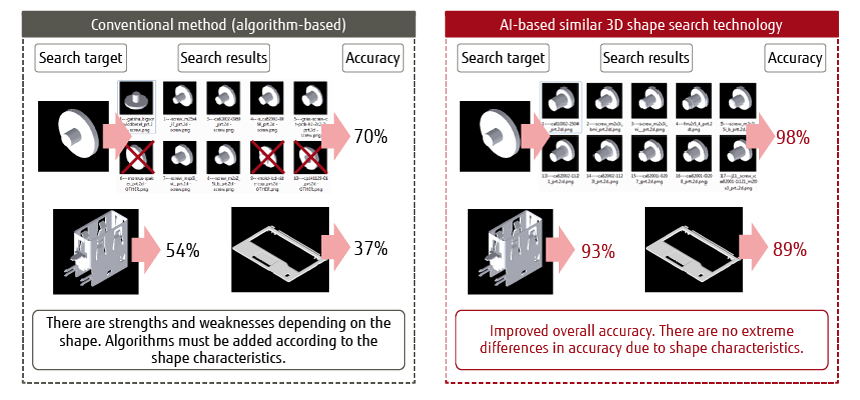
Figure 5 Comparison of conventional method and AI-based similar 3D shape search technology.
The AI used by this technology is trained on a large number of 3D models accumulated by Fujitsu. As a result, this technology achieves search speeds that can withstand practical use even for vast bodies of data on the order of one million parts, regardless of the industry, making this technology suitable for a wide range of applications, including general-purpose use.
5. Toward the realization of a new style of monozukuri
So far, we have introduced Fujitsu’s design and development solutions in the new normal era for the realization of a new style of monozukuri. With a view to the creation of new collaborative environments that will drive innovation in the future, we will expand our security solutions such as digital encryption, cyberattack countermeasures, and capture prevention, as well as global solutions such as global information management, enhanced governance, and GDPR compliance. By combining these solutions, we aim to support the diversification of work styles and open the way to new ways to collaborate and innovate.
Further, the technologies for the high-speed display technology and similar 3D shape search technology introduced in this article are being used not only within the Fujitsu Group but also by many customers in the manufacturing industry as “FUJITSU Manufacturing Industry Solution COLMINA Design Review, High-speed Remote Desktop and “FUJITSU Manufacturing Industry Solution COLMINA Design Review, Similar 3D Shape Search
,” and there has been an upsurge in inquiries due to the COVID-19 pandemic. We will continue to work to meet the needs for global design by further strengthening the functions we offer.
6. Conclusion
This article has described the internal practices of Fujitsu, which is working toward the realization of design and development environments in the new normal era, the technologies that have been developed for these practices, and a proposal for a new style of monozukuri.
Going forward, we will continue to bring the digital transformation to the manufacturing industry by utilizing the know-how and reliable technologies we have cultivated through in-house practices designed to fit the changing environment. In so doing, we aim to meet the expectations of our customers for a new style of monozukuri and earn their trust in the process.
All company and product names mentioned herein are trademarks or registered trademarks of their respective owners.
References and Notes
- H. Hayashi et al.: A Study on Structural Design Case Search Method Using 3D Shape as Key. Information Processing Society of Japan GN Study Group (2016) (in Japanese).Back to Body
About the Authors
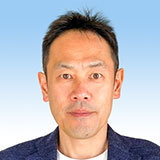
Mr. Yamaura is currently engaged in the development of PLM solutions for the manufacturing industry.
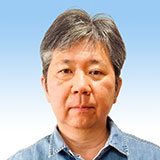
Mr. Nozaki is currently engaged in the development of PLM solutions for the manufacturing industry.
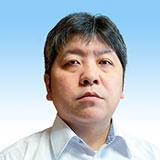
Mr. Suzuki is currently engaged in the development of PLM solutions for the manufacturing industry.
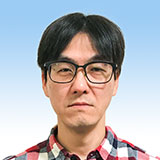
Mr. Furumoto is currently engaged in the development of PLM solutions for the manufacturing industry.