Digital Transformation in Manufacturing: Top challenges CxOs face and proven solutions
Part 3: 4 ways CxOs can overcome manufacturing challenges
In part 3, we summarize the findings of this study mentioned in Part 1 and Part 2.
While the progress of Industry 4.0 or smart manufacturing over the past decade has not been as strong as expected, in the two-plus years since the pandemic began, expectations of manufacturing DX have expanded beyond productivity gains and customer value creation to improvements in resilience and sustainability as well as solutions to societal challenges. Of course, digital technology cannot solve all economic, environmental, and societal problems, but we must recognize the need to leverage it to help solve societal problems.
In Part 3, we present four recommendations that CEOs should address immediately, based on the challenges posed by smart manufacturing and the initiatives implemented by leading companies to date.
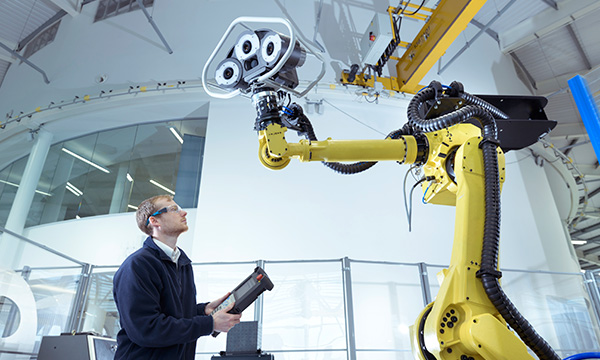
Growing expectations of digital manufacturing
Figure 3 illustrates the growing expectations placed on manufacturing DX. The push for smart manufacturing was initially expected to improve efficiency and total experience, and create flexibility and new business, as shown by the dotted circular line in the figure. Currently, as the diagram’s outer circle shows, the area denoting expectations has expanded to include implementation of sustainability, supply chain resilience, human centricity/workforce engagement, and corporate governance.
Figure 3 The breadth of functions required for manufacturing DX
As described above, the functions to be delivered through manufacturing DX and the demands (needs) made by the economy and society are changing, but digital technologies will remain as core enablers for Industry 5.0. It will therefore be important to determine how to fulfil new economic and social needs and values. The fundamental debate here does not revolve around naming conventions such as Industry 4.0, Industry 5.0, SX (Sustainability Transformation), or RX (Responsible Transformation), but rather, that the use of digital technologies for building new solutions requires a solid approach.
Composable architecture as a common platform for manufacturing DX
As already mentioned, in an era that calls for resilient and agile management, composable thinking is a key requirement for manufacturing DX. IT systems and OT systems (mechanical products and manufacturing processes) must both therefore have composable architectures. This will not only accelerate the pace of integration of IT and OT, but also promote low-cost smart manufacturing, as well as meet the societal demand for human-centricity.
As mentioned above, the concept of modular architecture originally existed in the IT field for both hardware and software products. In recent years, especially since the start of the pandemic, composable thinking has developed and applications have shifted in a composable direction. Manufacturing DX is not simply a matter of focusing on digital technologies. It is important to implement composable architectures for everything involved in smart manufacturing, including the design and manufacture of physical production systems and production technologies that apply digital technologies, as well as the corporate organization. The challenge here is how to componentize physical products and production equipment on the production floor, something that has been considered difficult until now. In essence, it is critical to use such a composable approach to develop common infrastructure for all IT and OT in smart manufacturing.
Taking advantage of economies of scale and network effects
In applying digital technology, it is essential to consider economies of scale and network effects. ‘Economies of scale’ means that by gathering many similar items together, a greater result can be achieved than with a single item. In business and management, it can be expected to improve management efficiency, reduce costs, and expand production volume. The ‘network effect’ is linked to Metcalfe's Law, in that the expected effect can be maximized by forming an E2E ecosystem along the value chain.
The individual WEF-designated Lighthouses mentioned above have deployed around 15 to 30 use cases, and some Lighthouse companies have already realized economies of scale and network effects through widespread deployment to additional manufacturing sites. Their approaches and use cases are likely to serve as a useful reference.
Combining smart manufacturing IT infrastructure with use case-enabled applications
As discussed, manufacturing DX must provide new value the more the global environment changes, so with each change comes a new name, such as SX, RX, Industry 5.0, and so on. Meanwhile, as made clear by the abovementioned six technology areas supporting Industry 5.0 in the EU, digital technologies continue to occupy a central role as enablers. In the push for smart manufacturing, the IT infrastructure underlying smart manufacturing is indispensable to any transformation.
Put another way, the IT infrastructure for smart manufacturing is IIoT platform, but in some respects, individual manufacturing companies have difficulty building a smart manufacturing IT platform on their own due to ROI issues. For this reason, it is anticipated that industry-wide smart manufacturing IT infrastructure will be established. Service vendors for smart manufacturing IT infrastructure would then play a significant role.
Meanwhile, solutions to support new needs could be addressed by individual use cases (applications). In Fujitsu's approach described earlier, common functions and modules are provided as services on a platform. A framework for enabling reuse of components is also required.
Figure 4 illustrates the combination of IT infrastructure for smart manufacturing and use case-enabled applications. It is divided into two layers: the common IT infrastructure that supports smart manufacturing and the application part for each manufacturer. For the development of the application pool in the upper layer in Figure 4, it will be important to utilize the ecosystem to attract outstanding startup companies that specialize in various fields. Alternatively, manufacturing companies themselves could develop and implement their own solutions (applications) in the future. Vendors providing IIoT platforms will be required to further leverage the ecosystem by adding enablers on top of the platform and co-creating with partners.
Figure 4 Image of IIoT supporting smart manufacturing
Using a solid approach with a clear vision
The expectations placed on digital innovation to solve societal challenges are currently rising and expanding. Meanwhile, the promotion of smart manufacturing has not progressed as expected and we are therefore facing a variety of challenges. Digital innovation as an enabler is also lagging behind expectations, giving rise to many problems when the real world and digital systems do not mesh. In particular, because human-centricity and governance are wrapped up in value judgments when solving societal challenges, social consensus-building and institutional design are in some ways more important than digital technology.
The industrial world and CEOs engaged in manufacturing DX therefore need to raise their outlook, formulate a vision, and develop medium-to-long-term business strategies. Further acceleration of both digital and real innovation is also necessary, and this requires a solid approach.
References
- John Dyck (October 2021). Robot revolution & industrial IoT initiative - Partnering to drive interoperability and harmonization.
- METI (December 2020). DX Report 2 (Interim Report)
- BMWi (October 2019). 2030 Vision for Industrie 4.0 - Shaping digital ecosystems globally
- Molex (2021). The state of Industry 4.0: A survey of industrial manufacturing stakeholders
- METI Japan (2022). FY2021 Fact-finding survey on core manufacturing technologies: Challenges and responses in Japan's manufacturing industry
- WEF (January 2019). Fourth Industrial Revolution: Beacons of Technology and Innovation in Manufacturing.
- BMWi (November 2020). Sustainable production: Actively shaping the ecological transformation with Industrie 4.0
- CESMII (May 2022). 2022 Smart Manufacturing Market Survey
- European Commission (January 2021). Industry 5.0: Towards a sustainable, humancentric and resilient European industry
- European Commission (December 2021). Industry 5.0: A Transformative Vision for Europe. ESIR Policy Brief No. 3
- John Dyck (October 2021). Partnering to Drive Interoperability and Harmonization
- McKinsey Global Institute (May 2022). Securing Europe’s future beyond energy: Addressing its corporate and technology gap
- McKinsey & Company, ACCJ (February 2021). Japan Digital Agenda 2030
- Monika Sinha (2021). The Gartner 2022 CIO Agenda: Make Composability Your Superpower
- WEF (September 2021). Global Lighthouse Network: Unlocking Sustainability through Fourth Industrial Revolution
- WEF (March 2022). The Global Lighthouse Network Playbook for Responsible Industry Transformation
- METI Web (2022). Material from Study Group Working toward the Transformation to a Digital Industry
About the author
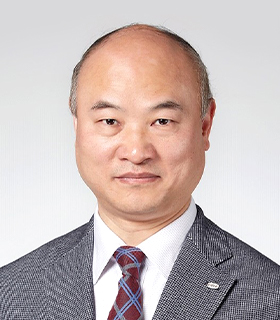
Dr. Jianmin Jin
Chief Digital Economist, Marketing Transformation Division, Global Marketing Unit.
Dr.Jin is engaged in mega trends insights of global political, economic, social and technology (PEST), and the research and analysis of advanced cases of digital innovation / digital transformation (DX).
Dr.Jin’s latest book is "Towards the Creation of the Japanese Version of Silicon Valley: Ecosystem Innovation Learned from Shenzhen" (Co-authored).