Remote operation center
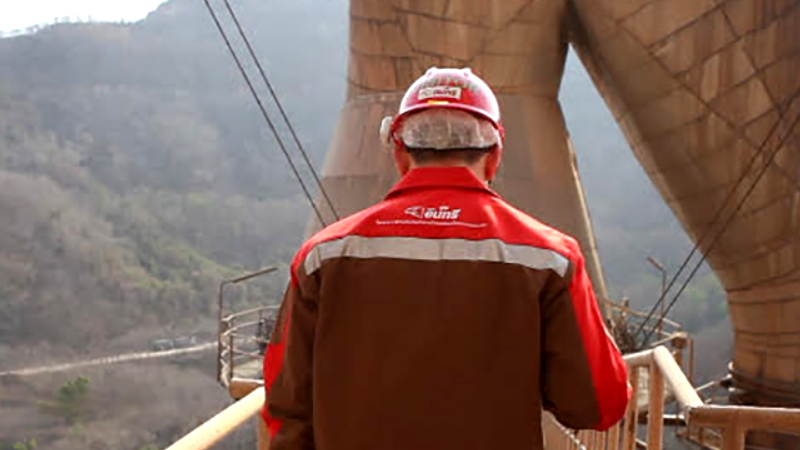
Smart Factory Remote Operation Center
At the heart of Fujitsu’s Smart Factory is the remote operation center – the plant’s veritable command center, enabling senior managers and engineers to monitor all of the facility’s critical machines and data and connecting the senior staffers with employees and contractors inside and outside of the plant.
The remote operation center integrates IT and OT data across the entire plant. Data collected from sensors on the plant equipment, along with information from digitalized inspections and activities of contractors, flow into the operation center, where senior staff can view the data on computer monitors and video wall displays. There they also can keep track of the location and work performance of contractors and plant employees. In addition, senior managers and staff have access to resources outside of the operation center.
Directing operations from a centralized point
“The remote command center is basically where we are connecting the world to the machines,” says Alfee Lee, DX Officer (DXO) ASEAN+I (India). The operation center forms the nexus of the Smart Factory Fujitsu rolled out for the Siam City Cement Co., or SCCC, situated on a sprawling 5-square-kilometer factory campus in Thailand.
The benefits of the remote operation center are obvious, Lee says. Senior engineers and managers can direct operations from a centralized point, assigning junior staffers and contractors in the field to check on potential problems with machines and other plant equipment. The senior staffers can monitor and advise the junior engineers and contractors in the field from the operation center via a video or other data link.
“The senior engineer can be in the command center, directing the junior engineer to go to the ground,” Lee says. “And also, this remote operating center will be connected to second-level and third-level expertise outside of Thailand, which is a partner located in Switzerland.”
Whereabouts of contractors
The remote operation center is integrated with a location tracking system, which enables managers to know the whereabouts of contractors in real time. There is also contractor geo-fencing data that gets fed into the operation center.
“This remote command center knows where the contractor is, and what they are doing at the site and how long they stay there,” says Lee. “And this remote operating center also controls when the contractor wants to enter the location at the security (checkpoint).” The integration of the operation center with another component of Fujitsu’s Smart Factory technologies, the contractor management system, enables plant managers to know “who is checked in, and whether they are moving to a restricted zone,” he says.
The operation center also has access to CCTV and predictive analysis data. And video conferencing is available, too.
Digital connected factory
Underpinning the operation center is a pervasive network set up by Fujitsu, which in the SCCC plant in Thailand is anchored by 375 Wi-Fi access points. This network forms the foundation of the digital connected factory, linking people, devices and machines across the 5-square-kilometer plant.
The operation center itself is a room that can accommodate around 10 senior managers and engineers, and the plant must set up new procedures, workflow, KPIs and appoint a new team to staff the center. This requires commitment from top management to fully support this transition, says Fujitsu.
In the end, creating a command center to monitor data and direct operations of the Smart Factory will result in less downtime and lower maintenance costs for the machines and will bring about greater efficiency in the operation of the entire facility.