The smartest factories liberate makers
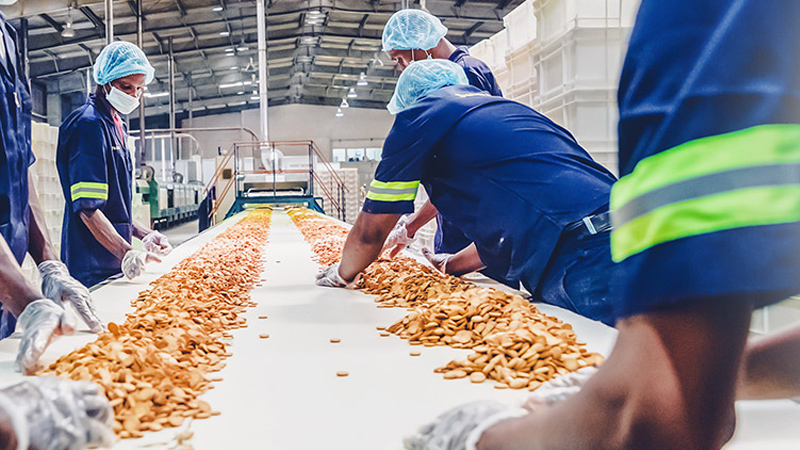
Fujitsu Smart Factory Transformation
Transforming your shop floor to keep pace with today’s highly demanding and ever-changing customer
Shopfloor transformation has always been on the radar for manufacturers, but the seismic impact of COVID-19 has turned it from tomorrow’s nirvana to today’s needs-must.
In the coronavirus-changed economy, customer expectations are changing fast – and your people, whatever their level of expertise, must be ready to rise to the challenge.
Give your makers the smart factory technologies they need to shine; designing and developing products around customer demands, to build trusted, long-lasting relationships.
By uniting makers and machinery, your business can drive operational excellence from the shopfloor, securely connecting your end-to-end supply chain and enabling innovation around on-demand availability, customization and personalization.
Industry 4.0 - accelerating innovation, automation and driving operational excellence
People have always been, and will always be, your most powerful asset. Digital transformation will energize them to focus on high-value tasks and deliver outstanding customer experiences.
As the beating heart of your business, the shopfloor is central to your smart factory journey.
Industry 4.0 is unleashing new technologies that accelerate automation, connect data and drive operational excellence on the shopfloor, to unlock the true mastery of your makers.
7 things your makers can achieve with smart factory technology
- better, faster, cost-effective production of goods
- on-demand availability, including small batch production
- customized designs, materials and delivery
- complete traceability of all parts, ingredients and materials
- the opportunity to develop services and experiences, not just products
- sustainable models that reuse, repair and repurpose – moving from linear production to a circular economy
- qualify as a trusted partner in your digital supply chain by implementing cyber security as a key quality characteristic of your production process and the goods you produce
Fujitsu manufacturing solutions - accelerating innovation, one change at a time
The transformative potential of smart factory technology is vast. But Rome wasn’t built in a day. Successful manufacturers are tackling digital transformation one step at a time, providing people with a logical, achievable roadmap that generates incremental but highly effective change.
For immediate value, your business needs to optimize the people, products, services and process you have right now – so your makers can create goods seamlessly and cost-effectively, without compromising on quality. Then comes the exciting part.
The smart factory – transforming to data-driven enterprise
At the heart of Industry 4.0 is the smart factory, where data enables your makers to respond to disruptive trends, enter new markets, deliver better products, and get ahead of operational challenges such as equipment maintenance and factory downtime.
Building a smart factory enables you to leap forward from traditional automation to a fully connected, flexible system, where valuable data flows securely throughout your business.
A narrow focus on data generated within the factory will slow digital transformation. It is vital to think about the entire end-to-end data pipeline – from supply chains to distribution networks and customer outcomes. Within this model customers are driving change and data enables your makers to respond more rapidly to their evolving needs.
Visible, usable data will empower your makers to reach better decisions quicker, and innovate across key shopfloor areas:
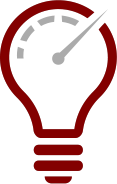
GAINING BETTER INSIGHTS
Use technology to connect assets and systems in real-time, in order to enhance production performance monitoring.
Taking action...
Retrofit legacy machinery with Internet of Things (IoT) sensors to increase data flows
Deliver services using IoT, rather than just producing physical goods
Use digital twin technology to virtually replicate machinery and model potential problems
Gain insights into existing processes by aggregating and visualizing machine data
Visualize data systematically across departments and factories in a hierarchical manner
Gain insights from data context using classic IT systems (e.g. ERP and CRM systems)
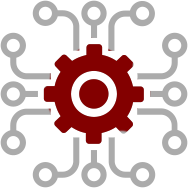
OPTIMIZE PRODUCTION
Use data to empower makers so they can optimise processes and make sustainable recommendations.
Taking action...
Map production schedules to actual execution time, to assess productivity
Measure energy expenditure and costs to look at where reductions can be made
Optimize planning with Digital Annealer, which has been shown to reduce production time by up to 30%
Minimise impact on production by swiftly analysing restart options following a production outage
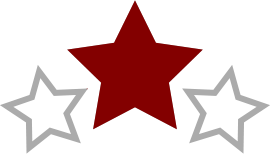
IMPROVE QUALITY
New, predictive maintenance approaches to maintenance are using industrial IoT technologies to solve problems, that haven’t yet occurred:
Taking action...
Forecast production requirements using machine learning algorithms
Detect abnormal conditions, so engineers can anticipate repairs
Reduce annual cost of machine failures and cut unexpected downtime
Build an infrastructure and configuration register for the future while securing production assets and processes. Benefit from cutting edge and proven technologies - edge computing, cloud systems and private 5G network.
Empower your makers with a transformative 21st Century toolbox
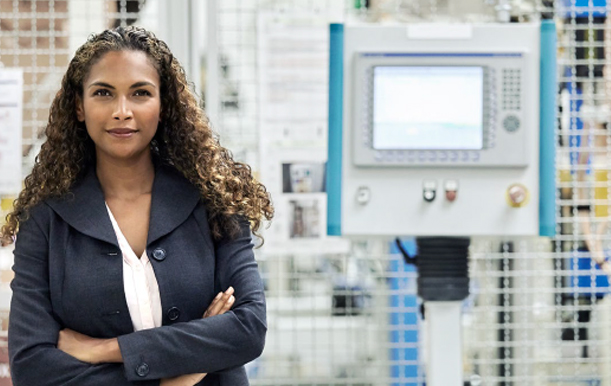
HOW TO BE ALWAYS OPTIMAL
How to achieve the highest levels of manufacture using Fujitsu’s Quantum-Inspired Optimization Services
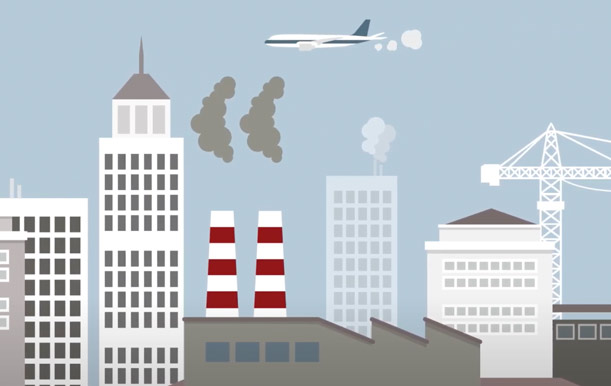
NORMALISE THE EXCEPTIONAL
Improve the quality and consistency of your inspection processes using artificial intelligence
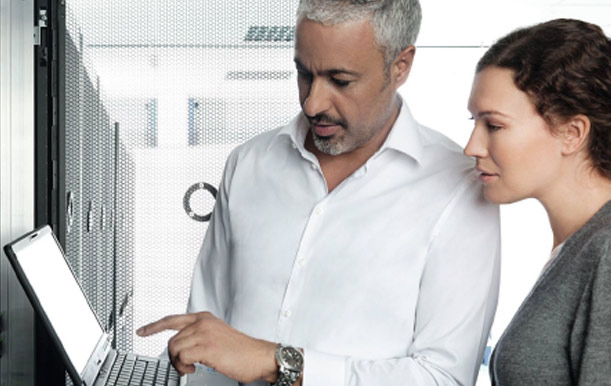
HOW TO SECURE OT ASSETS
Constantly monitor and protect your business-critical operational technology using Fujitsu’s Cyber Security Services
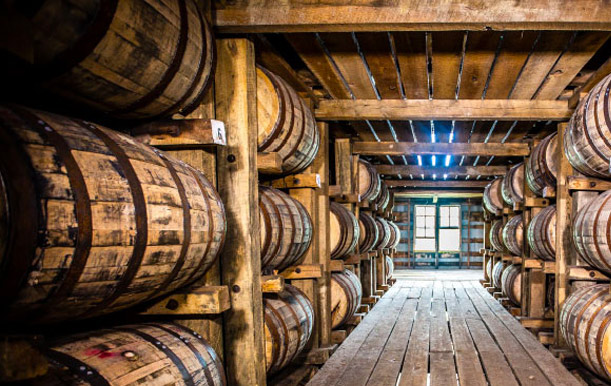
HOW TO REIMAGINE EVERYDAY OPERATIONS
How to build on the momentum you achieved during lockdown and stay resilient in times of change
Visit the Knowledge Hub to browse our full ‘How To’ library »
Customer story

The challenge
Logoplaste is a leading packaging manufacturer with more than 60 plants in 18 countries. The company’s goal is to partner long term with blue-chip clients serving markets such as food and beverage, personal care, household, healthcare, oil and lubricants.
Logoplaste faced major challenges bridging an employee skills gap and ensuring experts could quickly attend its factories to fix production issues. These challenges triggered extended production downtime and a skills deficit among employees.
The solution
Fujitsu’s solution helped to enable Logoplaste’s makers to “see” how challenges could be overcome using assisted reality smart glasses. Experts no-longer need to attend factories and employees can learn new techniques remotely, which results in a reduced down time, decrease of travel costs and the ability to adapt and grow during the global pandemic.