Technologies to Improve Quality in Manufacturing Organisations
Improving quality can be a key competitive differentiator for manufacturers. While it can reduce costs and improve output, quality assurance can also ensure that the finished product receives positive customer reviews. In the age of social media and instant opinion-sharing, it’s never been more important to ensure that customers are fully satisfied and impressed with the products they buy.
Therefore, quality can be more important than price or speed for many manufacturers. Improving quality can be a legitimate game changer for those manufacturers that can deliver a high-quality product at the right price, fast.
Using smart factory technologies, manufacturers can improve quality through better traceability, inspection, analysis, real-time monitoring and visualisation. Automated inspections with increased accuracy can dramatically reduce defect rates. This also minimises costly manual processes and the time wasted in rectifying defects.
Furthermore, these technologies can provide tangible data for analysis, letting factories further improve their quality assurance processes, keep equipment working according to calibrated standards, and reduce costly downtime.
How Fujitsu can help improve the quality process through automated inspections
Fujitsu offers smart factory tools that can help automate and digitalize inspection processes. Using a combination of cameras, microphones, vibration sensors, and existing data sources such as thermal imaging or X-rays, the Fujitsu solution can inspect any-size components and automatically detect defects. Even subtle defects will be picked up, letting factories move towards a zero-defect approach.
By catching production errors early, Fujitsu’s solution avoids the risk of delays caused by rework in subsequent manufacturing stages. Importantly, the time saved on manual inspections means that manufacturers can inspect 100 per cent of their products instead of taking a sampling approach, which increases the risk of defects slipping through.
Fujitsu has worked with manufacturing customers around the world to significantly benefit their quality assurance processes.
Defect detection for concrete panel manufacturers
Concrete panels used by the construction industry need to be defect-free otherwise the integrity of the panel could be compromised and it may not perform according to specifications. Therefore, it’s essential for concrete panel manufacturers to carefully examine each panel for any defects before the panel leaves the plant.
However, this can be complex as the concrete panels are designed according to specific requirements and can include ducting, electrical conduits, sockets and more. Therefore, the inspection process involves making sure each panel has been assembled correctly as well as ensuring there are no other defects.
For one manufacturer, using a visual inspection approach meant that defects could go unnoticed and there was no foolproof detection method. When a staff member found defects, they recorded them manually in a spreadsheet or other recordkeeping form. This made it difficult for the manufacturer to get a clear view of its defect rates, including how much defective products cost the organisation and whether there was a systemic issue that needed to be addressed.
Using a smart defect detection tool from Fujitsu, this manufacturer automated the inspection process using image recognition technology. Now, when the system detects a defect, it displays an alert and the information is retained in a database so that the organisation can get important insights into the numbers and types of defects, when they occur, and even why they occur. This makes it much easier for the manufacturer to dramatically reduce the number of defects, saving both time and money.
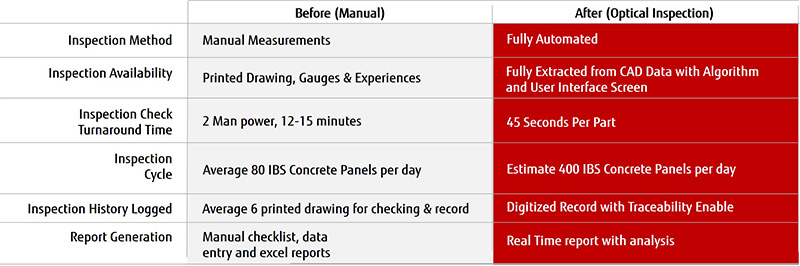
Quality inspection for automotive manufacturers
With so many components making up modern automobiles, the process of checking for defects is naturally complex and error-prone. A manual quality control process requires significant amounts of manual labour and, even then, usually means the manufacturer can’t literally inspect every component. Instead, they have to conduct random sampling to find defects.
Even with random sampling, it took one automotive manufacturer 90 seconds per part to conduct defect checks and the turnaround time was 45 minutes per part for the random sample check.
After implementing an inspection solution, which is a fully automated quality control solution that checks 100 percent of parts, the time to inspect each part was reduced to just 45 seconds. Importantly, no manual labour was required, which meant that there was no turnaround time required for random checks, greatly improving efficiency.
Real-time automated reporting highlighted specific defective areas, letting the manufacturer address these issues in a timely fashion. Consequently, the defect rate percentage decreased from 14 per cent to two per cent in just two months after installing the solution.
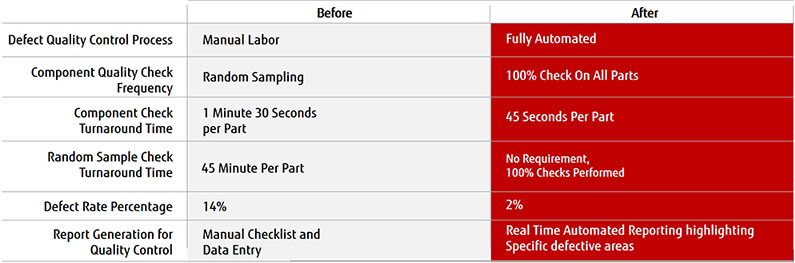
For more information on how Fujitsu can help your manufacturing firm transform into a smart factory, contact us today.