Unlock greater value in your making process
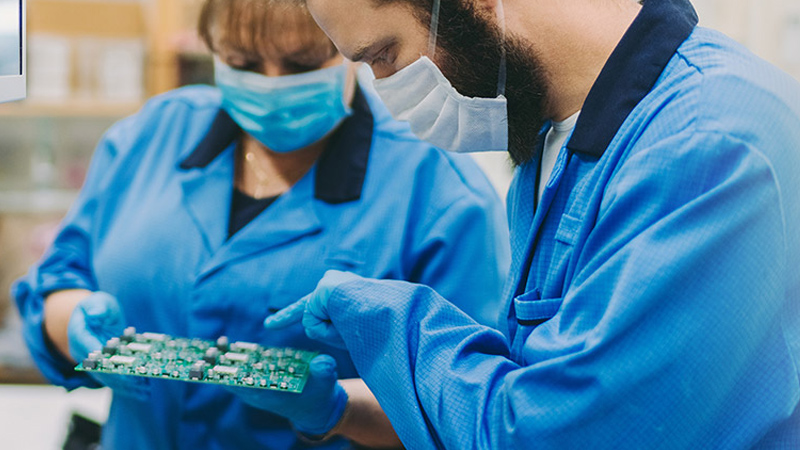
Fujitsu Smart Supply Chain Solutions
COVID-19 and the seismic supply chain shift
Rethink your supply and distribution networks and enable your people to continue making, whatever happens.
The coronavirus pandemic has interrupted global supply and distribution networks in a way we have never seen before, with material shortages bringing production lines to a standstill.
To stop this happening again, manufacturers need to perform a ‘factory restart’ on their inbound supply chains and outbound logistics – giving teams the insight they need to maintain productivity in all circumstances.
Anticipating disruption and reacting quickly right through supply and distribution networks will empower your makers to deliver continuous value, whatever is happening in the world.
Connected manufacturing - anticipate disruption, liberate making
Smart factory technologies empower manufacturers to work and make in a complex world. But to truly thrive in an unpredictable market, these solutions must deliver value beyond your factory floor.
The fastest way to energize your most important asset – your people – is to build a smart supply and distribution network.
An intelligent, connected network transforms makers into changemakers. Every decision they make is based on real, timely information, liberating their talent.
With a 360-degree view of the entire manufacturing operation and value chain, your makers can constantly adjust to changing conditions and develop sustainable models.
6 ways smart supply chain and distribution networks empower your makers
- gives people the data visibility they need to make the best decisions
- provides a 360-degree view of material supplies, warehousing and distribution
- maximizes end-to-end efficiency and drives ROI
- prioritizes productivity, in all circumstances
- enables complete traceability and transparency, both internally and for the customer
- puts the focus on service delivery and great customer experiences
The circular economy: a (supply) chain reaction
It’s not just market forces driving supply chain transformation. Your customers are pushing for change; for greater sustainability and accountability in your choice of materials, suppliers and manufacturing processes.
Smart manufacturers are moving away from vertically integrated supply chains and linear take-waste-use production models. Instead, they are adopting an approach that repairs, re-uses and recovers.
It’s called the circular economy – and it’s a huge business opportunity.
By rethinking your supply and distribution networks, you can prove the origin of all your assets and materials, and encourage sustainable, secure ways for your key people and partners to collaborate.
Most importantly, you can use the circular economy as a catalyst for stronger, value-driven customer communications, with changemakers’ talent at the heart of all relationships.
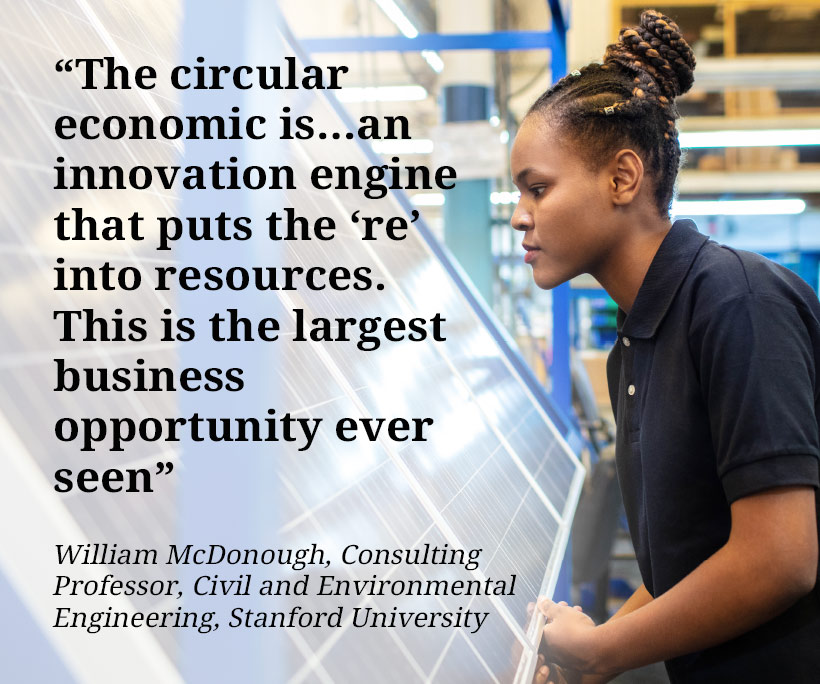
Empower your makers with a transformative 21st Century toolbox
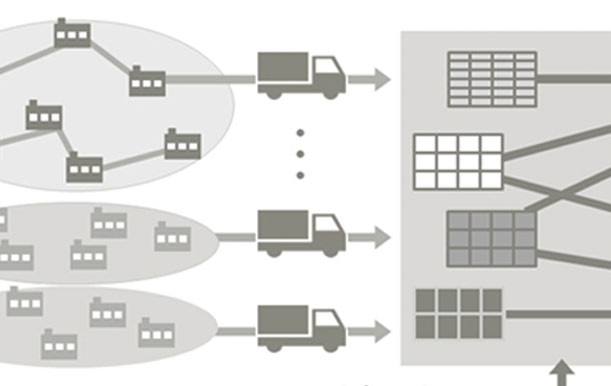
HOW TO CUT THROUGH SUPPLY CHAIN COMPLEXITY
Make better decisions by quickly optimizing supply chain logistics using Quantum-Inspired Optimization Services
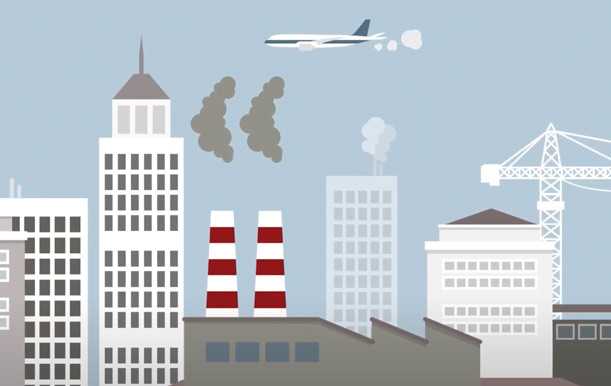
HOW TO BRIDGE THE CUSTOMER EXPERIENCE GAP
Elevate customer experience by integrating all your business processes – from sales to fulfilment
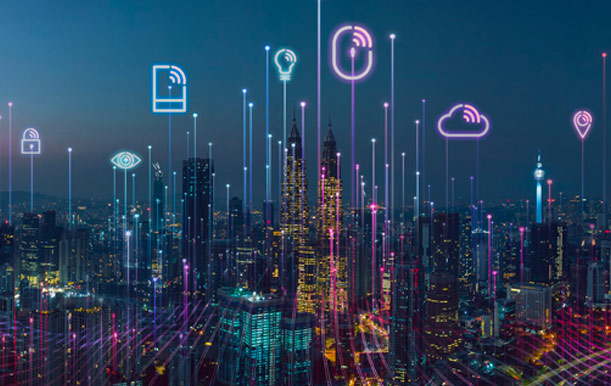
HOW TO IMPROVE VISIBILITY OF YOUR ASSETS
Easily track, manage and report on your manufacturing assets - supporting multiple applications through RFID and sensor-based technology.
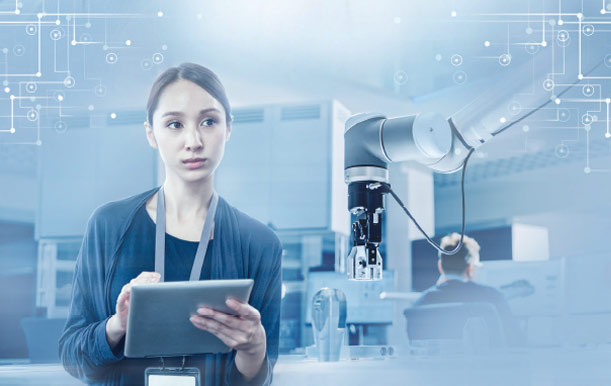
HOW TO REIMAGINE CUSTOMER EXPERIENCE
How to reimagine customer experience and meet demands and requirements in the new normal
Visit the Knowledge Hub to browse our full ‘How To’ library »
Fujitsu manufacturing supply chain management - trust a manufacturer to transform a manufacturer
Fujitsu is an ideal choice as your strategic manufacturing technology partner. We’re manufacturers too with ‘making’ part of our heritage, it’s our passion and is integral to our nature and identity.
Digital transformation is a path best walked one step at a time, and we believe it’s time to take your first step.
Unlike our competitors, our approach is to build direct relationships with your makers. We observe them, listen to them, question them and learn from their answers – before empowering them to meet customer demand by connecting the end-to-end supply and distribution process.
Let us work together to co-create a roadmap to smarter manufacturing. We can help you to use digital transformation technology as part of your 21st century makers’ toolbox. Fill out our contact form and we’ll get in touch.
Thank you.
Customer story

The challenge
Nilfisk relied on disparate spreadsheets to monitor the location and condition of thousands of on-loan tools. This led to time-consuming data entry, duplication of effort and lack of real-time visibility across its inventory. It needed a flexible asset management solution to streamline its supply chain.
Read More
The solution
Nilfisk selected Fujitsu based on our deep experience with ServiceNow to deploy Nuvolo, an enterprise asset management (EAM) platform. Nuvolo provides a seamless digital workflow, a single system of record, and integrates seamlessly with existing enterprise resource planning (ERP) and service desk platforms.
Nilfisk and third-party vendors can now track the location and condition of tools in real-time, enabling better customer service. Predictive maintenance ensures maximum uptime and productivity. The company benefits from total visibility of inventory and richer data enables smarter decision-making. Repairs are also more efficient, with tickets automatically generated through ServiceNow.