Case study
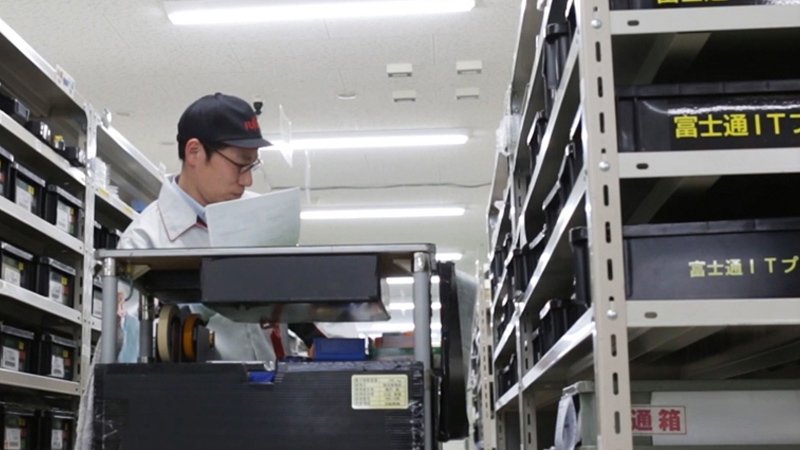
Travel distance for parts pickup operations reduced by up to 45%
Digital Annealer can find the shortest possible route instantly
Fujitsu’s Digital Annealer can solve combinatorial optimization problems instantly using a digital circuit design inspired by quantum phenomena.
The advancement of ICT technology and the realization of Artificial Intelligence (AI) today means that there is a necessity for computers to be able to carry out complex calculations in an instant, with the expectation that the knowledge gained will then be applied to various fields of business such as manufacturing, distribution, retail, automotive and finance, to name a few.
This case study introduces how Fujitsu IT Products Limited deployed Digital Annealer and succeeded in dramatically improving the efficiency of in-warehouse operations.
An opportunity while pursuing efficiency
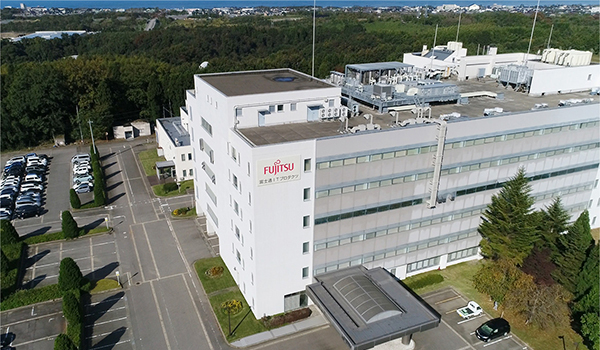
Fujitsu IT Products Limited
Fujitsu IT Products Limited has been a key manufacturing facility of Fujitsu’s computer systems, storage systems and medium to large servers such as mainframes, UNIX servers, mission critical IA servers and supercomputers. Since being established in 2002, production styles have been moving forward with the integration of manufacturing organizations that advocate for improved customer satisfaction in pursuit of QCD (Quality, Cost, and Delivery) for large variety and small quantity production.
Executive Officer Kazuyuki Niwa said, “Manufacturing facilities are required to constantly produce high quality products efficiently. Also, due to diversifying market needs, it is important to produce a wide variety of products in low volume.”
Kazuyuki Niwa
Executive Officer
Fujitsu IT Products Limited
“This environment means that we are always researching better ways to raise production levels. A main area of focus has been to find and implement the most optimal routes inside our factories, including warehouses. As a part of our production improvement research, we discovered Digital Annealer and its strength in solving combinatorial optimization problems. We thought this could be utilized at our factories.”
Digital Annealer uses a digital circuit design inspired by quantum phenomena, a new technology that can solve complex combinatorial optimization problems that classical computers cannot solve in a reasonable amount of time. In order to understand what a combinatorial optimization problem is, consider the following traveling salesman problem example. A salesman needs to visit several cities. The goal is to find which route offers the shortest total distance, visiting each city only once. In the case of 30 cities, the total number of possible routes is to over 2.65x1032. Digital Annealer can solve this problem within a second.
Parts Pickup Procedures No Longer Require Experienced Workers
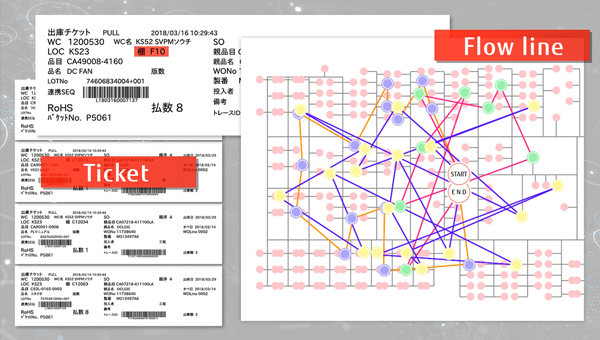
Complex Routes: Shelf Number, Part Names on Storage Ticket, and Pickup Time
Warehouse employees leverage Digital Annealer technology to increase efficiency. Warehouse operations are first given delivery requests for parts from each of the production lines. After the requests are received, a list of the parts (delivery ticket) is generated from within the warehouse. Workers collect the parts listed on the ticket from the warehouse shelves and deliver. On the delivery ticket, the name of the part and the shelf number for where it is stored are described.
Director Kenji Miyata mentions that “finding parts could be thought of as an easy job that anyone can do. However, good collecting required experienced workers.”
“At this time, warehouses making use of the Digital Annealer command about 1000 square meters of space, with about 3,000 stored products. Workers look at the ticket and collect the parts. Before implementing Digital Annealer, the parts listed on the delivery ticket did not have the order of part shelves included, and because the shelves with the parts themselves were not in alphabetical order, it was not an environment designed for workers to systematically collect parts. For workers with very little experience, if they could not find the shelves with the parts, then they would spend a lot of time wandering around the warehouse trying to look for them, and therefore take a lot of time to collect the parts.”
Kenji Miyata
Department of General
Manufacturing and Technology
Fujitsu IT Products Limited
Recently, as a result of small production quantities with many varieties, there are many types of parts being delivered. Before implementation of Digital Annealer, the collection of parts required experienced workers.
“At the beginning, incoming and outgoing delivery of parts was outsourced. But 2 years ago, we started recruiting all warehouse workers in-house. When the in-house team first began the work of collecting parts, the situation they encountered was that it had taken time to learn and memorize the storage place for parts, and so gathering parts would take a lot more time than when it was outsourced. With the new in-house team, we had to rely on the experienced workers to do the parts pickup work. Even as the new staff’s expertise grew, we still had to put procedures in place to use experienced workers to guide the parts collection.
While dealing with these circumstances, when Digital Annealer was being discussed, it hit us that if this could solve the traveling salesman problem, it could be utilized with the shelves and parts.” (Executive Officer Kazuyuki Niwa).
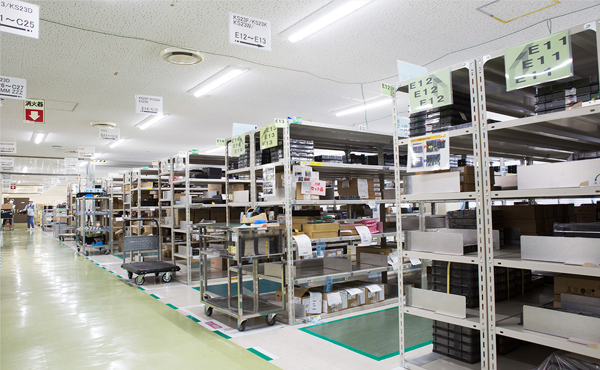
Fujitsu IT Products’ Warehouse.
Several thousand types of parts occupy a 1,000 square meter area.
Display of the optimum picking route in an instant
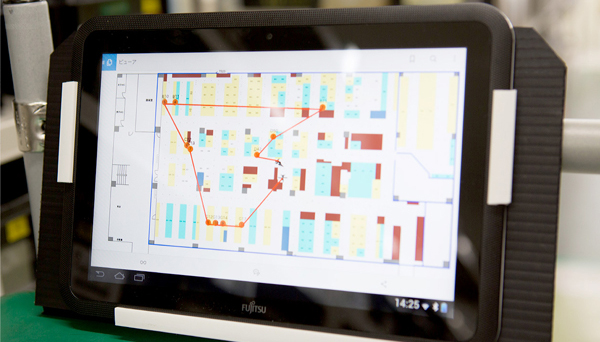
The optimum pickup route displayed on a tablet, allowing workers with little experience to follow the shortest route.
Digital Annealer was up and running in just 3 months.
“From warehouse selection to consultations, it took just a few months to introduce the Digital Annealer into operations. We decided to use the Digital Annealer Cloud Service to support our original system of tickets. It was not confusing and went quite smoothly,” explained Director Kenji Miyata.
The system is very simple to use, and the storage information for delivery, along with the placement of parts to be sent out means the Digital Annealer provides the most efficient system for anyone to understand and navigate.
With the introduction of Digital Annealer, the system displays maps on tablets for the shortest route, and it is easy for workers to collect parts.
“As expected, being able to visualize routes was key. To pickup parts, you would go here and there inside the warehouse. But now it has become a one-stroke sketch. Confirming that with our own eyes was a wonderful thing,” according to Executive Officer Kazuyuki Niwa.
“Another spectacular thing was the speed,” said Director Kenji Miyata. “Up until now we had relied on experienced workers, and people would worry about how to make the best of their work. Now in an instant we do not need to rely solely on experienced workers; rather, junior workers are able to carry out the tasks easily.”
With the achievements of an improved flow, it was possible to consider the optimum position of each part. Parts are placed on shelves close to where they are most often needed on the production line. With just one change, the route is shortened and results in more efficient work.
“Improving efficiency requires those in the workplace to get a sense or feeling for it to move forward. Just talking about it will not make the routes shorter. Visualization helps make this happen. We know this effect thoroughly, and by raising the efficiency, we can change the way of thinking for many of the workers.”
According to Director Kenji Miyata, “It is projected that the traveling distance for gathering parts will decrease by 20% each month. In addition, changing the location of the shelves could possibly lead to a 45% reduction, which is a real possibility.”
Executive Officer Kazuyuki Niwa continues, “The system was rolled out and trialed at one warehouse first. Once we saw the results, we thought we could expand this to other warehouses. We now expect to benefit from other production improvements resulting from the implementation of Digital Annealer, such as warehouse employee shift optimization and the ordering process for products.”
Digital Annealer Services
We offer three of Digital Annealer Cloud Services, Digital Annealer On-Premises Services and Digital Annealer Technical Services