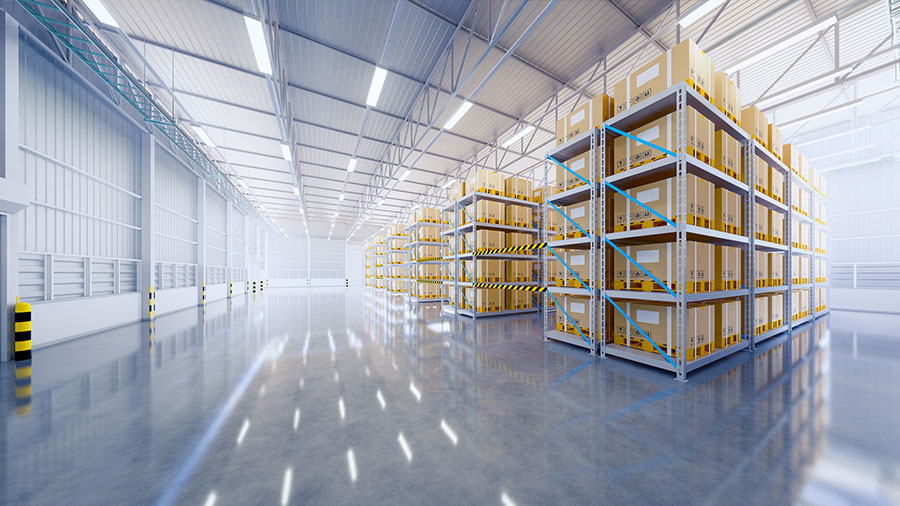
近年の社会的環境の変化と昨今の新型コロナウイルス感染拡大の影響によるニューノーマル時代の到来によって,人々の生活様式やビジネスモデルは一変した。物流業界もその影響を受け,従来からの最適化・自動化へのニーズは更に高まってきた。
本稿では,最適化・自動化へのニーズに応えるべく,倉庫および物流センター内におけるピッキング指示作成業務の最適化にAIを導入する取り組みと,その検証プロジェクト事例について述べる。
1.まえがき
昨今の新型コロナウイルス感染拡大の影響によるニューノーマル時代の到来によって,人々の働き方や生活様式,更にはビジネスモデルも一変した。コロナ禍によって,ECやインターネットサービスの利用者が急増し物流量も増加したが,それ以前からあった物流に対する変革意識が更に強まり,最適化・自動化へのニーズは高まっていた。
これまで物流業界では,倉庫および物流センター内(以下,庫内)の業務改革に長年取り組んできた。入出荷作業を最適化することで,生産性を向上させる改善活動がその一例である。具体的には,人手不足を補うためのプロセス・作業の効率化,人手作業の省力化,設備による自動化を検討・実施してきた。更に,昨今ではAIを導入するという取り組みに注目が集まっている。最適化によって生産性が向上すれば,必要最低限の人員で庫内業務が遂行可能となるだけでなく,密な状態も回避できる。そのため,従来から行ってきた庫内の業務改革と,昨今のコロナ禍の両方の対策につながる。
お客様と富士通のシステム・AIの専門家との共創によるデジタルトランスフォーメーション(DX)から得た知見とノウハウを,上述した庫内業務改革に活用すれば,お客様の業務パフォーマンスを今まで以上に向上できる。これらは庫内業務改革に限らず,付加価値の高いソリューションを提供する富士通のビジネス全般においても有用なものと考える。
本稿では,庫内におけるピッキングの指示作成業務において,AIを用いて最適化する取り組みとその検証プロジェクト事例について述べる。
2.庫内業務最適化への取り組み
2.1 ピッキング作業指示作成の最適化を対象とする背景
前章で述べたとおり,物流業界では庫内業務の改革に長年取り組んできた。しかし,図-1に示したとおり,庫内業務は複数の作業工程があり,取り扱う商品の形態や出荷する単位[1],導入している設備によって作業のバリエーションが多数存在する。そのため,庫内業務におけるボトルネックは,お客様ごとに様々である。これらの問題を,AIを活用して最適化するための検討を進める上で,複数の最適化要素が挙がった。その中から,ピッキング業務を最適化の対象とすることで,省人化と省力化,更には人員の密軽減対策となると考えた。その理由は,様々な業務の中で,ピッキング業務は人的リソースを多く投入しているだけでなく,作業指示の内容によって作業時間と労力が大きく変化するからである。
更に,ピッキング方式は,図-1に示したようにシングルピッキング,トータルピッキングに大別され,シングルピッキングを同時にマルチ(複数)に実施する方式がマルチピッキングと呼ばれる。マルチピッキングの場合,作業指示を作業者の判断で組み合わせて実施していたために,属人的であるが故に生産性の向上が課題となっていた。 以上の理由から,マルチピッキング方式のピッキング作業指示の作成を対象に,AI技術を活用した最適化を行うことで,庫内業務の改革を進めることにした。
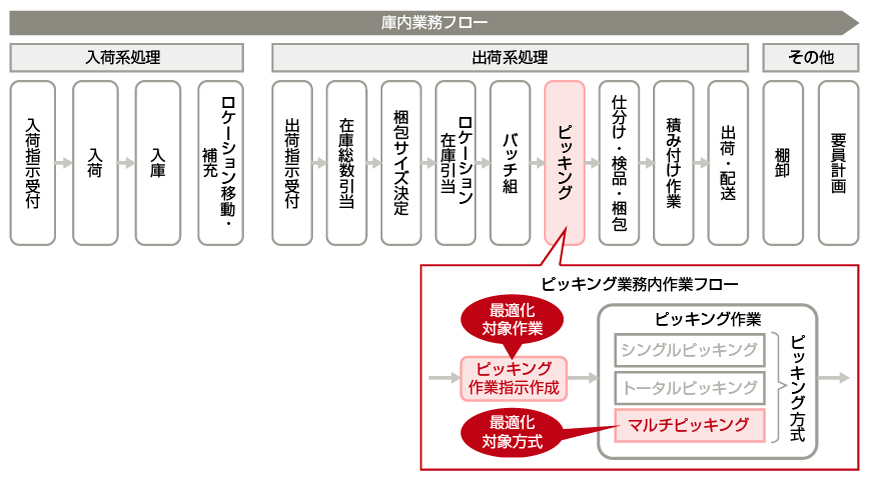
図-1 庫内業務フローと最適化対象
2.2 ピッキング作業指示作成の最適化における従来の技術とその問題点
ピッキング作業指示作成の最適化に用いたAI技術の一つは,従来から存在していた製造現場における作業工程を短縮するための最適化技術である。しかし,庫内業務における制約条件は,製造現場の制約条件と異なっているという問題があった。庫内業務におけるピッキング作業現場の制約条件の例として,以下の様なものがある(図-2)。
- 縦動線は一方通行(赤色の実践矢印)
- 横動線は右方向へのショートカットが可能(赤色の破線矢印)
- 通路は台車2台分の幅があり,追い越し可能
- 搬送コンベアは,1本のみ(青色の破線矢印)
- ピッキング終了後,近くの搬送コンベアにオリコン[2]を流し,その場所で次のピッキング指示を入手し着手する
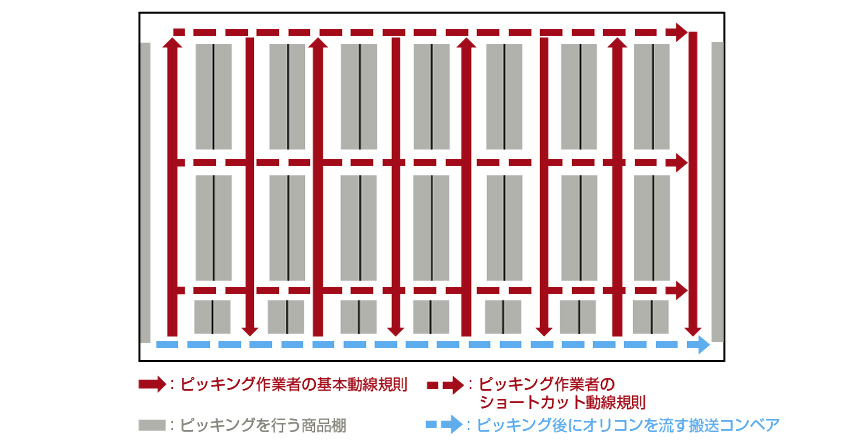
図-2 作業現場の制約条件イメージ
また,マルチピッキング方式における最適化を行う場合は,複数の指示の組み合わせ(マルチ)を複数の作業者が同時に行うという点が,庫内業務に必要な技術要素として不足していた。更に,他の組合せ最適化問題を解決する既存技術は,渋滞の回避や現場の制約条件までも考慮した最適化はできないという問題があった。
問題は技術面だけではない。上述の問題点を解決できるAIを新たに安価に開発することは,投資費用の観点から難しかった。
2.3 採用したAI技術
マルチピッキング作業指示の最適化を行うために,実現性やコスト面を考慮し,富士通(旧富士通研究所)が開発した生産計画用の数理最適化技術(OPTIMILIS:オプティマイリス)を物流用に改良し,更に組合せ最適化技術を加えてカスタマイズしたAIエンジンを開発した。このAIエンジンは,図-3に示したピッキング作業指示の組合せ最適化技術と作業順序最適化技術の二つで構成される。本来,作業順序最適化技術は,本来生産スケジュールを組むための技術であるが,ピッキング作業指示の組合せ最適化技術に応用することで,マルチピッキング作業指示の最適化を実現している。
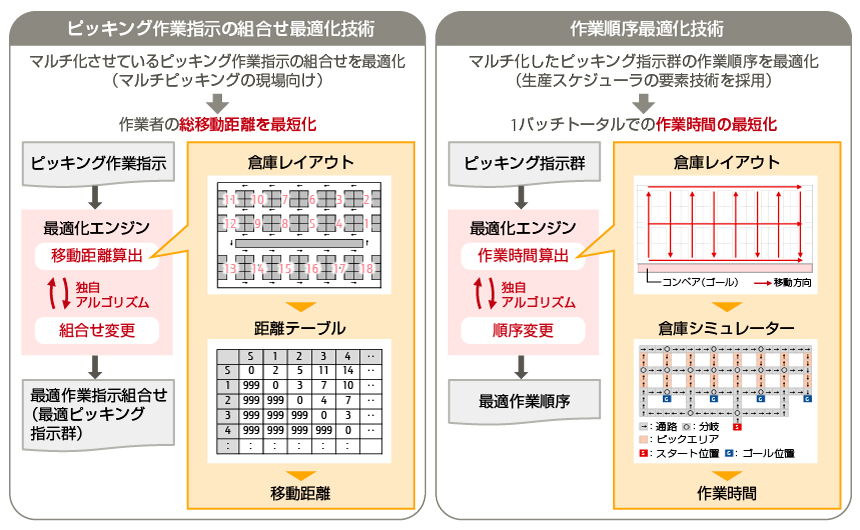
図-3 開発した最適化AIエンジン
(1)ピッキング作業指示の組合せ最適化技術
本技術は,1回のピッキング指示で抽出されるマルチ指示の組み合わせで,最適解を算出するための技術である[3]。目的変数[4]は全作業の総移動距離,前述の制約条件下において逐次最適化させるシミュレーション技術をベースに,小規模問題の解法として総当たりとする手法を用いている。そのため,1つのマルチピッキング作業に割り当てるピッキング指示の組み合わせを1つずつ確定させ,移動距離の総和がより短いものから先に探索する。この手法を用いることで,従来の技術だけでは不足していた部分が補完され,庫内業務におけるピッキング作業現場の制約条件下でも適用可能となった。
(2)作業順序最適化技術
本技術は,前述のとおり生産スケジュールを組むための要素技術であり,庫内の渋滞回避などを考慮した作業時間の短縮に効果的な技術でもある[3]。目的変数は全作業の作業完了時間,および逐次最適化がベースで,小規模問題の解法は遺伝アルゴリズム手法を採用している。遺伝アルゴリズム手法とは,まず初期解群を生成し,各解の評価(点数付け)および点数に基づく選択淘汰を行う。次に,進化オペレーションによる解の変化から得られる各解の評価(点数付け)を一定回数繰返し(世代交代),最終世代の最良解を最終的な解答とする手法である。また,独自開発の時間駆動型の離散事象シミュレーター[5]を活用し,1商品あたりのピッキング時間や歩行速度,作業員の人数などを設定することで,渋滞を加味した作業完了時間の算出が可能となった。これによって,従来の技術では対応できていなかった庫内業務への適用を可能としている。
3.ピッキング作業指示の最適化検証プロジェクト事例
本章では,AIによるピッキング作業指示の最適化に成功したA社のプロジェクト事例について述べる。
3.1 プロジェクト概要
本プロジェクトの対象のピッキングエリアは縦50 m,横140 m,作業人員は最大で110人という比較的大きな物流センターにおいて実施した。ピッキングに使用するオリコンは10 L,20 L,40 Lという3種類で最大6個まで搭載可能なピッキング検量台車を使用して,マルチなピッキング作業を実施している。
本プロジェクトは,プレ検証とPoC検証の二つのフェーズに分けて進めた。以下に,各検証フェーズについて説明する。
3.2 プレ検証フェーズ
(1)プレ検証条件の確認
プレ検証フェーズでは,1日分のデータの中で,6つのピッキングを組み合わせて行う6マルチピッキングの実績データのみを対象とした。その理由は,組み合わせが最良であればあるほど,移動距離が短くなるため,最も高い効果が見込めるからである。
(2)最大37.1%の作業時間短縮に成功
この検証条件下で行ったプレ検証では,作業者の1回のピッキング作業時間が,従来比7.7~37.1%短縮という幅のある結果となった。そこで,作業者の時給などを考慮して費用対効果を試算し,ピッキング作業時間を10~15%短縮することを目標に,PoC検証フェーズへの移行をA社に提言した。
3.3 PoC検証フェーズ
(1)PoC検証条件の確認
PoC(Proof of Concept:概念実証)検証フェーズでは,実際の運用に近い制約条件に変更し,6マルチピッキング以外も含むすべてのデータを7日分用いて検証した。変更した制約条件は二つあり,一つは,ピッキング指示データ項目内の区画縛り条件の撤廃を行った。もう一つは,作業者のピッキングアイテム数(作業負荷)の偏りを防ぐために,組み合わされた6つの作業指示内のピッキングアイテム数の上限を,運用上現実的な80に制限した。
(2)総移動距離は平均30.3%,作業時間は平均19.7%の短縮に成功
(1)で確認した条件を追加して検証した結果,ピッキング作業者の総移動距離が平均30.3%,作業時間は平均19.7%と大幅な短縮に成功した(表-1)。
更に,このPoC検証で得られた効果だけではなく,AIが計算に要した処理時間(検証日別AIエンジン別に0.2秒~11分の幅あり)も併せて検証結果としてA社に報告し,実装化に向けた検討材料とした。
表-1 PoC検証結果
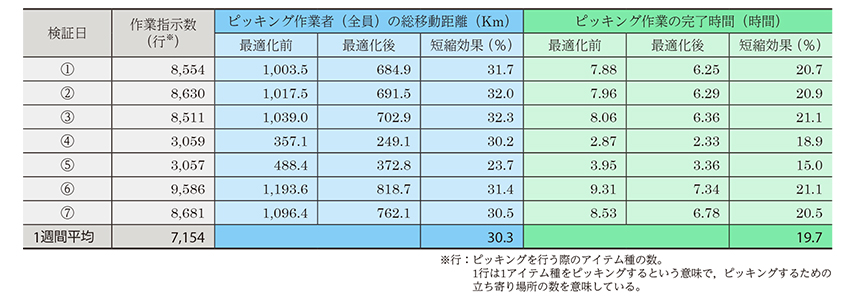
3.4 実装化に向けた課題
検証フェーズにおいて,新たに見つかった課題は二つあった。一つは,実装時に最適化された効果を確認するための機能の追加である。PoC検証では検証用データを用いて,業務で遂行した結果(実施作業時刻)が記載されたデータを基に最適化前と最適化後(理論上)の比較検証を実施している。一方,実運用で使用するデータは,最適化後の作業指示データとなり,効果の比較結果を目で見えるかたちに出力する必要がある。もう一つは,AIの計算処理時間を実運用上の許容範囲内まで短縮することである。
これらの課題を解決するためには,作業指示の予定データと最適化後のデータを比較して,効果を集計する機能と,AIの計算処理時間の短縮施策を加えて再度検証する必要がある。そうすることで,実際の運用条件に近い検証が可能となり実装化に向けて大きく前進する。
5.むすび
ニューノーマル時代の到来やニーズの多様化によって,新しいビジネスモデルが生まれ,従来のサプライチェーンスキームは変革時期を迎えている。人手不足による業務改善の限界は,業界全体で抱えている問題である。そのような問題に直面しているお客様に対して,富士通が持っているイノベーティブな技術だけでなく,必要に応じて他社技術とのコラボレーションを行いながら,庫内業務の最適化,更には物流業務全体のDX化を行うことで貢献していく。そうしてお客様から得られた信頼を元に,富士通の物流ビジネスを拡充させて持続可能な社会を目指していく。
本稿に掲載されている会社名・製品名は,各社所有の商標もしくは登録商標を含みます。
参考文献・注記
著者紹介
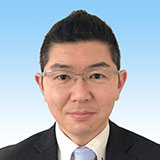
CP&S事業本部
流通系DX事業に従事。
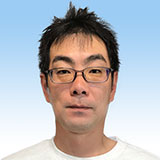
CP&S事業本部
流通系DX事業に従事。
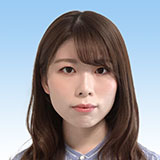
CP&S事業本部
流通系DX事業に従事。
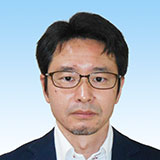
研究本部 ICTシステム研究所
数理最適化技術の研究に従事。