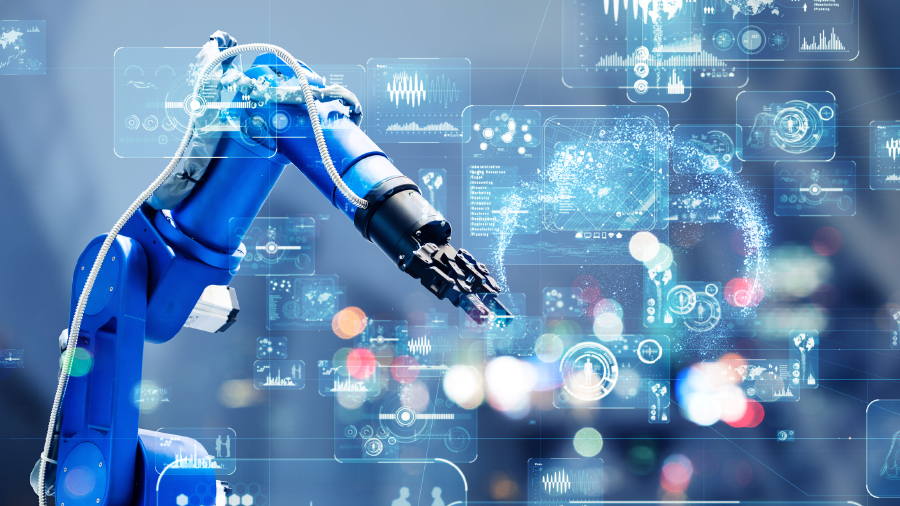
あらまし
本稿では,製造業のデジタルトランスフォーメーション(DX)に向けた富士通のAI技術の研究開発について解説する。高い生産性と優れた品質管理に支えられている製造現場は,労働者人口の減少や作業者の育成の課題に直面している。一方,高い付加価値を提供し,市場競争力を強化するためには,現場ばかりでなく,製造プロセス全体にわたる変革が求められている。これらの課題に対して富士通欧州研究所(FLE)は,AI技術によって現場をデジタル化することに加え,製造業そのものを変革するソリューションの提供を目指している。製造ラインの不具合や多様な素材や部材の製造不良を,高い精度で検出する異常検出技術を新たに開発した。更に,AI技術の応用範囲を設計工程にも拡大し,物理現象を模擬するDeep Learningの応用技術AI Simulatorを開発中である。
1.まえがき
労働力が競争的優位を決めていた時代は過ぎ去り,現在の製造業では,技術が競争的優位を決め,イノベーションの源泉となっている。新機能,耐久性,環境性能などの付加価値を提供する素材,部材,および製品は,これらを実現する工学や製造技術の研究開発成果によって実現されてきた。一方で,実際に製造し,供給するに当たっては,現場での品質管理が重要であると認められている。しかし,製品の高機能化に伴って業務が高度になっているにもかかわらず,依然として品質管理は熟練作業者の目視により実施される場合が中心であり,作業者の負担の増大につながっている。また,労働者人口の減少もこの状況を更に深刻なものにしている。
経済産業省は「2019年度ものづくり白書」[1]の中で,技術のデジタル化と徹底的な省力化によって深刻な人手不足を追い風に変えるために,AIやIoT技術を基軸にした製造業デジタルトランスフォーメーション(DX)を提言した。欧州富士通研究所(Fujitsu Laboratories of Europe:FLE)では,これに先んじて2017年度にAI技術による製造業の変革に向けて研究開発を開始した。我々は,まず非破壊検査を対象としてDeep Learningの応用技術の開発に着手し,最初のステップでは,従来人手で行っていた風力発電機のブレードの製造不良検出作業をデジタル化した[2,3]。これにより,超音波エコー画像の確認作業を劇的に短縮する成果をあげた。
本稿では,非破壊検査に関する技術のデジタル化に続き,製造・検査工程の徹底的な省力化を実現するDeep Learningの新応用技術,およびAI技術の応用範囲を設計・開発工程にも拡大するための,物理現象を模擬するAI Simulator[4,5]を開発したのでこれを報告する。本稿の構成は次のとおりである。2章でこれらの新技術で解決する問題を提議し,3章および4章でそれぞれの技術課題と解決策を示すとともに,適用例と今後の課題を述べる。最後に5章で本稿をまとめ,今後の展望について述べる。
2.製造業におけるDXの課題
図-1に,我々のAI技術による製造業DXに向けた研究対象の変遷を示す。前章で述べたように,非破壊検査のうち,これまでは人が時間をかけて行っていた異常箇所の判別作業を,機械が代行するところからスタートした。この業務は,高精度な測定機を利用し,熟練作業者が正確に不良の有無を判断するものである。このような業務は,今日のDeep Learningが得意とする人のノウハウをデジタル化できる顕著な例である。本技術は,既に非破壊検査ソリューション「F|AIR(Fujitsu Advanced Image Recognition)」[3]として製品化済みであり,作業時間を短縮するとともに,判断の正確さを均一化する効果を上げている。
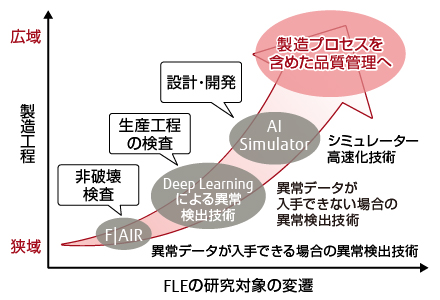
図-1 FLEが目指す品質管理
続いて,我々は生産工程の検査に対するAI適用の拡大を図った。例えば,素材表面のきずや汚れ,あるいは部材の加工や塗装のミスなどを検出するタスクである。生産工程の検査におけるこのタスクの難しさは,不良パターンがあらかじめ想定しつくすことが困難なほど多様であり,かつ発生率も低い点にある。そのため,良品のデータのみを使って良否の判別を実現しなければならないことに加え,不良箇所の特定もできなければならない。この数年間でDeep Learningは爆発的な進化を遂げており,それぞれの課題を解決する個別の技術は研究されていたものの,全てを同時に解決する手法を開発する必要があった。これを実現し,作業者が目視で行うしかなかった作業までも徹底的に省力化することを目指したのが,後述する異常検出技術である。
更に,我々は生産工程から設計・開発工程へAI適用の拡大を図った。従来から設計・開発段階で性能を評価するために,計算機シミュレーションが利用されているが,物理現象を数理モデル化し,精緻に模擬するための計算コストは膨大である。これを,Deep Learningを用いて物理的な条件と現象の関係のみを学習することで,モデルベースの数値計算を代替し,設計・開発作業と性能評価の反復を更に容易にする技術がAI Simulatorである。その実現においては,モデルフリーなDeep Learningで代替する際の,出力の信頼性を評価する技術が鍵になる。
このように我々は,検査工程のデジタル化から,設計・開発工程のデジタル革新へと,品質管理におけるAI技術の適用範囲を拡大させてきた。次章以降では,Deep Learningによる異常検出技術とAI Simulatorについて,更に詳しく解説する。
3.異常データが不要な異常検出技術
本章では,Deep Learningによる異常検出技術について説明する。図-2に本技術の学習・運用時のプロセスを示す。
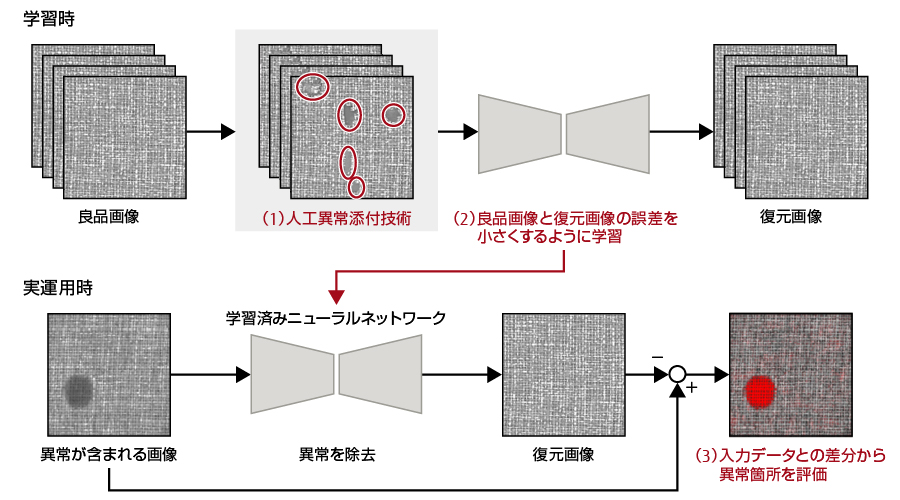
図-2 Deep Learningによる異常検出技術の学習/実運用プロセス
学習時には,まず良品のみを撮像した正常画像データのみを用い,人工異常添付技術によって,正常画像データの一部に人工的に異常を加える。次に,異常を加えた画像から正常画像を復元するようにニューラルネットワークを訓練する。運用時にはこの学習済みニューラルネットワークを用いることで,入力画像に異常がある場合でもない場合でも,異常を含まない画像に変換する。更に,入力画像と変換後の復元画像を比較することで,異常の有無のみならず,その箇所を特定することが可能になる。
つまり,本技術は(1)人工的に異常を添付する処理,(2)異常を含まない画像を学習する処理,および(3)入出力画像の差分から異常箇所を評価する処理を,合目的に機能させたことがポイントである。また,学習の入力に良品の画像データのみを使うため,比較的少量のデータで学習することができ,短期間で現場へ導入できる利点を有する。
製造業における異常検出タスクを想定したベンチマークデータを用いて,本技術を評価した。その結果,素材,部材,製品のいずれにおいても,画像からの異常検出タスクで好成績を収める他大学,他企業の先行研究成果に比べ,平均精度を大幅に改善することに成功した。現在,鉄鋼,飲料,食料品,自動車などの分野で,複数のパートナー企業と技術実証を展開している。その一つである製造ラインのトラブルを検出するタスクにおいては,データ受領から2週間で高精度な結果を示し,本格的なシステム導入に向けてカスタマイズを実施中である。この他にも,橋りょう,舗装路,鉄塔などのインフラの老朽化点検業務など,画像を使用した異常検出にも適用を見込んでおり,運用時の処理の軽量化・高速化などの改良を行う予定である。
4.物理シミュレーターの高速化技術
本章では,物理シミュレーターを高精度かつ高速に近似する技術AI Simulatorについて説明する。図-3に示すように,AI Simulatorは,物理シミュレーターの入力であるジオメトリ情報をボクセル化により3次元空間上の小領域上で表現する。そして,物理シミュレーターが数理モデルに則って計算した出力をこの入力に対する正解データとして学習させることで,物理現象を模擬するように生成ニューラルネットワークを訓練する。例えば,熱流体シミュレーションの場合であれば,ジオメトリ情報とは物体の配置,密度,熱伝導率などであり,これらの情報から熱伝達分布を計算する。
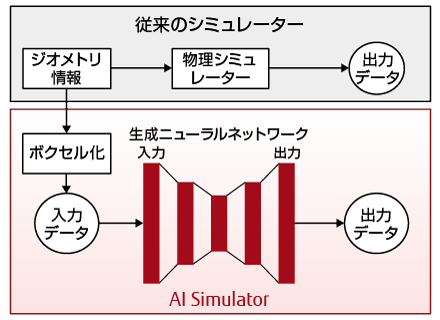
図-3 AI Simulatorの構成
図-4に,AI Simulatorを流体解析や荷重解析に適用した例を示す。(a)は流体計算の熱伝達分布,(b)は構造計算の変位分布を示している。どちらの結果も,物理シミュレーターと比較して遜色ない精度であることが確認できる。
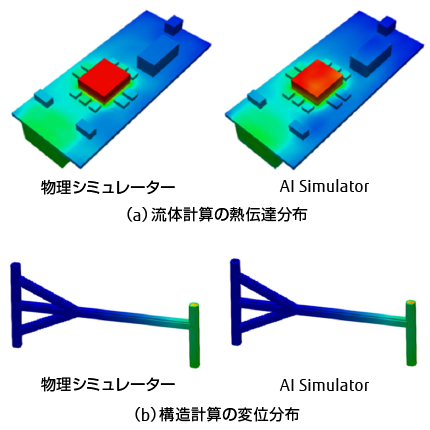
図-4 AI simulatorの適用事例
物理現象を模擬するためには,大規模な生成ニューラルネットワークを利用する必要がある。また,高い精度で物理現象を模擬するよう訓練するとともに,出力の信頼性を評価する手段が必要になる。本技術では,(1)ジオメトリ情報を適切なボクセル形式に変換する,(2)大規模な生成ニューラルネットワークを精度よく訓練する,および(3)出力の不確実さを評価する,という三つの課題を解決することによって,これを実現することができた。特に,今日のニューラルネットワークが得意とするボクセル形式をそのまま使ってしまうと,計算コストが膨大になってしまうという問題があった。我々はこの問題を,出力に強く依存する領域のみを対象に計算を行うことによって克服した。このような先端的な技術と,産業応用の大きな可能性が評価され,本技術はIntel DevMesh AI Spotlight Award[6]を受賞した。
本技術は,エネルギーや自動車分野での技術実証に向けて,より大規模で複雑な構造を持つ対象を扱うための技術改良を行っている。また,物理シミュレーションには,流体や構造を扱うのに適したモデルばかりではなく,それ以外の数理モデルを扱うものがあるため,これらに対応することで応用範囲を拡大していく予定である。更に,AI Simulatorで培った生成ネットワーク技術は,品質検査を含む他の課題に対しても有用であり,製造業における他の業務にも活用を進めていく。
5.むすび
本稿では,製造プロセスまで含めた品質管理を目指して,生産工程での検査業務および設計・開発業務に焦点を当て開発した技術であるDeep Learningによる異常検出技術とAI Simulatorを解説した。両技術は,製造業における共創ビジネスでの技術活用に続き,FUJITSU Human Centric AI Zinraiのソリューションの一つとしての提供と,ものづくり事業ブランドCOLMINA[7]への提供を目指し,様々な顧客との技術実証と技術拡張を行っている。今後は,製造業における品質検査業務や設計・開発業務の分野で,更なるニーズを捉えた技術開発を継続することに加え,全製造プロセスを視野にAI技術の活用と導入を通じて,製造業のデジタル化とデジタル革新に貢献する。
本稿に掲載されている会社名・製品名は,各社所有の商標もしくは登録商標を含みます。
参考文献・注記
- A. Al-Jarro et al.:“DeepSim-HiPAC: Deep learning high performance approximate calculation for interactive design and prototyping.”ICHPC,USA,2018.本文へ戻る
- A. Al-Jarro et al.:“DeepSim-HiPAC: Deep learning-based platform converts physics-based simulators into real-time AI simulators.”In NVIDIA GPU Tech,USA,2019.本文へ戻る
著者紹介
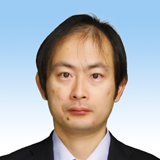
Artificial Intelligence Research Division
人工知能・数理技術の応用研究・開発に従事。
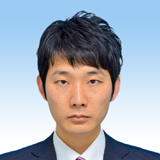
Artificial Intelligence Research Division
人工知能・数理技術の応用研究・開発に従事。
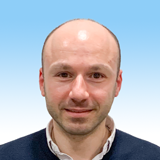
Digital Annealer Research Group
人工知能・数理技術の応用研究・開発に従事。
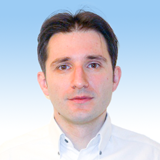
Digital Annealer Research Group
人工知能・数理技術の応用研究・開発に従事。