スマートものづくり実現のカギは「CPS」
先進事例を基に実践的構築法を議論
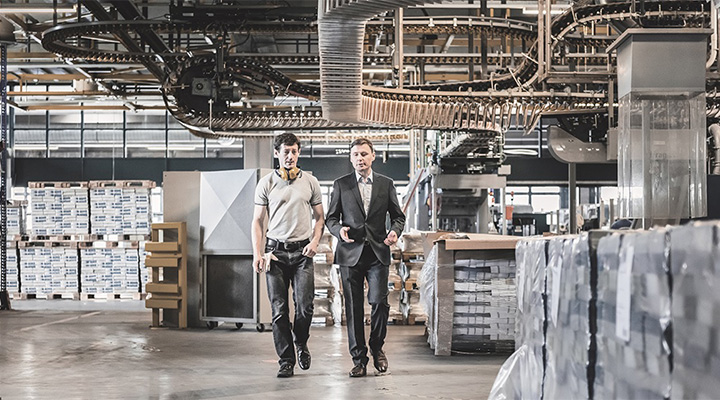
開発・生産などものづくりの過程で生まれるデータをいかに有効活用できるかが、製造業の競争力を左右する時代がやってきました。こうした中で、大きくクローズアップされているキーワードが「CPS(Cyber Physical System)」(注)。データを活用しながら現場のパフォーマンスを高める仕組みの基本コンセプトを指す言葉です。
2019年5月に開催された「富士通フォーラム2019」のプログラムの1つとして開催されたパネル・ディスカッション「製造業における『スマートものづくりの実現』~CPSの実践事例と実現に向けたポイント、今後の展開」では、先進事例を題材にして、CPSに基づく効果的なデータ活用の仕組みを現場に実装し、スマートものづくりを実践するための、具体的なアプローチや勘所について議論しました。ここでは、その概要を紹介します。
- (注)CPS(Cyber Physical System):フィジカル(リアル)領域で収集したデータをサイバー(バーチャル)領域で分析・検証し、その結果をフィジカル領域に反映させ相互に作用しながら課題解決を図る仕組み。
株式会社ITR
プリンシパル・アナリスト
浅利 浩一 氏
このパネル・ディスカッションで、パネリストを務めたのは、企業のIT戦略策定を支援するITRのプリンシパル・アナリストで特に製造業に精通している浅利浩一氏、ネットワーク機器・装置システムの製造を手がける富士通テレコムネットワークス(FTN)執行役員の寺内秀明、富士通 産業ソリューション事業本部 本部長代理の瀧澤健の3人。モデレーターを担当したのは日経BP総研上席研究員の三好敏氏です。浅利氏は、製造業の業界動向に関するエキスパート、寺内はCPS実践のパイオニア、瀧澤は製造業向けITソリューションのベンダーとして発言しました。
プログラムの冒頭で浅利氏が、CPSの概念を解説しました。この中で同氏は「これからの製造業の価値や競争力は、開発・生産を支える『人』『機械』『設備』『企業』『技術』の事業要素をいかにつなげ、効果的かつ効率的なシステムとして機能させるかで決まります。その中核となる情報システムの基本概念がCPSです」と、製造業におけるCPS活用の重要性を強調しました。
次に同氏は、CPSをものづくりの現場で実践するための様々な取り組みが、世界各国で進んでいることを紹介しました。例えば、超スマート社会として定義された日本政府の構想「Society 5.0」の中では、サイバー空間とフィジカル空間との融合が提唱されています。これが、まさしくCPSです。ドイツ政府が提唱している「Industrie 4.0」では、環境の変化に応じて機敏に対応することを重視しており、各種データの自動取得、連携の仕組みを実現するための様々なプロジェクトが進められています。ここで実現を目指している仕組みはCPSの概念に基づくものです。また、米国企業が中心となって設立されたコンソーシアム「Industrial Internet」の様々な活動の1つに、「Smart Fact Web」と呼ばれるテストベッドがあります。ここでは、グローバルに点在している工場を連携させる仕組みの実現を目指していますが、このベースもCPSです。
生産ラインの「ちょっと先の未来」を予見して事前に対処
富士通テレコムネットワークス株式会社
執行役員 寺内 秀明
浅利氏の解説の後、ディスカッションの本編が始まりました。最初に、CPSを自社工場で実践したFTNの寺内が、同社の取り組みとその成果を紹介しました。
最初に同氏が言及したのは、いち早くCPSの実装に取り組んだ背景です。「近年、まずサービスやソフトウエアの開発を進め、決まった製品仕様に後から合わせ込んでハードウエアを開発・生産する例が増えてきました。このような開発形態に対応するには、製品仕様や生産量が定まるやいなや、迅速かつ的確に生産体制を整備する必要があります」。こうした厳しい市場の要求に応えるためにFTNでは、変種変量生産に柔軟に対応できるように生産システムを強化することにしたそうです。同社は、モジュールや機構部品の生産から、PIU(プリント基板ユニット)、シェルフ、装置の組み立てまでを社内で一貫して手がけています。この工程に、CPSの概念を適用することで、それぞれの工程間で融通を利かせながら生産システムを最適化する仕組みを実現し、変種変量生産に対応させることを目指しました。
ただし、変種変量生産の管理は極めて複雑です。効率的な生産を行うためには、工場内の全工程の複雑に絡み合ったスケジュールや条件を、リアルタイムで最適化できる仕組みが不可欠です。FTNは、ここにCPSを活用しました。現在のコンベアラインの状況と、次に加工される製品に関する過去の作業履歴を基にして、生産ラインの「ちょっと先の未来」を予測する手法を開発。これを利用して、生産スケジュールの乱れやライン停止の未然防止を可能にし、生産性を向上させました。「かつてFTNでは、1年間にわたる改善活動によって生産性を10%向上させました。ところが、CPSを利用した独自生産方式を実践することで、3カ月間でさらに18%も向上させることに成功したのです。これは驚くべき成果でした」(寺内)。
「ちょっと先の未来」を予測する生産方式の概要(資料提供:富士通テレコムネットワークス)
FTNがCPSの実践に成功した理由はどこにあったのでしょうか。「適用範囲を限定してスモールスタートで始めたのが功を奏しました。目標を高く上げすぎることなく、迅速に課題を洗い出して対策する作業を何度も繰り返して開発を進めたことが、大きな成果につながったと考えています。また強い想いを持つリーダーの下、新たな手法を創造できる人材、実行力があり発展させる力を持つ人材。それぞれの個性を発揮できる協働体制が、システム構築で効果的に機能しました」と、寺内は導入の経緯を振り返りました。
ITとOTを融合させて現場力を最大限まで高める
富士通株式会社
産業ソリューション事業本部
本部長代理 瀧澤 健
事例の紹介を受けて、富士通の瀧澤は、製造業向けITソリューションを提供するベンダーの立場から、CPS導入の現状について語りました。「製造業に関わる多くの企業が、スマートものづくりの重要性は分かっているのですが、本当に成功しているのは一握りです。多くの企業は、PoC(概念実証)の段階で止まっているのではないでしょうか」。
瀧澤は、その原因について次のように分析しています。CPSの構築と運用には、データの中から価値ある情報を抽出して分析するために必要なIT(Information Technology)に関する知見と、現場から収集した質のよいデータを解析して効果的に活用するためのOT(Operational Technology)に関する知見の両方が必要です。ただし、ITとOTの両方に長けた技術者は少ないのが現状で、これがCPSの実践導入の広がりを阻んでいる大きな理由の1つということです。
続いて瀧澤は、こうした現状の問題を解決するソリューションとして、富士通のものづくりプラットフォーム「COLMINA」の概要と特徴、活用法を紹介しました。この中で瀧澤は、COLMINAは、難易度の高いシステム構築と運用のハードルを下げ、CPSを広く活用できるようにするためのサービス基盤だと紹介しています。
COLMINAは、PLM(product lifecycle management)、SCM(supply chain management)、MES(manufacturing execution system)といったITシステムと、現場でデータ収集やロボット、検査装置などの制御を行うOTシステムをつなぐ、ハブの役割を担うプラットフォームです。瀧澤は「COLMINAを活用すれば、お客様自らがデータ取得・分析を容易に行うことができ、生産ラインの課題検知、解決策の発見、実行、結果確認のPDCAをより早く回せます。
これによって、より良い改善策の発見と迅速な現場改善ができるようになります。また、富士通はお客様の現場改善のご支援もサービスとしてご提供致します」と語りました。
また「仕様変更への対応迅速化」「投入計画の最適化」「設備や人の稼働率向上」「品質不良の原因解明」といった製造業でニーズの高い課題に応じたソリューションを実現するために、それぞれの課題に応じたデータ活用方法をまとめた「シナリオ」を用意しています。この「シナリオ」には、自身が製造現場を抱える富士通が社内で培った知見と業種SEが収集した知見に基づく最適なデータ活用方法が反映されています。
「シナリオ」は、ユーザーの用途に応じて数多く用意されており、この中からユーザーが自身の用途に最適な「シナリオ」を選択し、活用することで、効果的かつ効率的にCPSに基づく管理システムが構築・運用できます。2019年2月には、各種の「シナリオ」を搭載した「COLMINA V2」を発売。さらに、2019年4月からは、従来のエンジニアリングコンサルに加え、現場のOT技術・ノウハウを提供するサービスをエキスパートコンサルサービスとして追加しました。
続いて浅利氏が、CPSをものづくりの現場に効果的に実装するために押さえるべきポイントとして「3つのW」について解説しました。
「CPS構築・運用の目的を明らかにすること、つまり、『どこで』の『Where』、『何を』の『What』、そして一番重要だと思うのが、『誰に対して』の『Who』です。この3つを最初からしっかり見据えていくことです。そのうえで、どうやって、どのテクノロジーを使うのかという『How』を押さえることが大切です」(浅利氏)。
さらに、今後はものづくり工程の生産性を上げるだけではなく、その前工程となる研究開発や設計工程をCPSの仕組みの中に取り込んで、ものづくり全体をライフサイクルで高度化することを目指すべきだとアドバイス。「できることから始めるだけではなく、今後、自分たちは、どのようなものづくりのライフサイクルを構築するのかを明確にし、これを関係者の間で共有することが大切です。『着眼大局・着手小局』だと思います」(浅利氏)。
生産現場の人とつながる、消費者とつながる将来のCPS
浅利氏は、「これからは大量生産・大量消費だけでは成り立たない時代がやってきます。そして、需要やニーズに応じた変種変量生産が拡大していくでしょう」と述べました。ただし、現在まで製造業が蓄積してきた知見やスキルは、大量生産・大量消費の要求に適合するためのものがほとんど。また、市場に直接つながって稼働する工場も現存しないと指摘しました。このため、「これからは市場や消費者の動きに合わせて、開発と生産の体制を機敏かつ柔軟に変えられるという新たなものづくりの強みを再構築する必要があります。市場と製造業の開発現場、生産現場をデータでつなぐCPSの役割はますます高まるでしょう」と方向性を示唆しました。
寺内は、「どんなにテクノロジーが進化しても、生産ラインのすべての作業を自動化できるわけではありません。また、匠の技が求められる作業、つまり簡単に情報化できない工程が確実にあります。こうした人手に頼る作業の負担を減らしながら、作業を通じて人の能力を高めていける仕掛けをCPSに盛り込みたいと考えています」とコメント。さらにFTNでは、将来のCPSを用いた新たなものづくりを『ヒューマンセントリック スマートものづくり』と呼んでいることを明らかにしたうえで、「人のスキル・技能を新たな企業価値とし、生産性向上だけでなく、働く人たちの幸福感も高める考えです」と語りました。
瀧澤は、「現在のCOLMINAは、見える化ができるようになり、やっとその先に踏み込む足掛かりができた段階です。生産ラインの最適化や制御技術の高度化を推し進めていくのはこれからが本番です」とソリューションの現状について話しました。これからは、生産品の品質が変化する予兆を察知して不良発生を未然に防ぐ、品質予兆監視の実現を目指すとしています。実現すれば、品質改善のためのPDCAサイクルを加速させ、生産時の不良発生を劇的に削減できるでしょう。また、熟練者の動きをデータ化し、継承や自動化に活用できるようにしたいという考えから、センシング技術、画像AI、骨格検出など上肢認識や行動分析技術を駆使して、熟練作業をデジタルモデル化するための技術開発を進めており、既にグループ工場で実証試験を実施していることを明らかにしました。
ノウハウを継承するために熟練者の動きをデジタル化し、その情報を利活用する仕組み
最後に、このセッションの締めくくりとして3人のパネリストが、CPSを実践する局面を迎え、それぞれの立場から今後の活動に向けた抱負を述べました。浅利氏は、「客観的な視点から、効果的で効率的なCPSの実現に向けてお手伝いしていきたい」とコメント。寺内は「CPSは、生産現場以外にも適用可能であり、特に人が関わる業務などへの適用に注力していきたい」と語りました。瀧澤は、「ものづくりの現場力とテクノロジーの相乗効果で日本の競争力を最大化したい」と力強く語りました。
概念が先行したCPSを巡る動きは、いよいよ実践の局面を迎えました。今回のパネル・ディスカッションでは、その状況が明確になったのと同時に、CPSを現場に実装するための具体的なアプローチが浮き彫りにされました。具体的な進化を遂げ、スマートものづくりの実現を目指す、あるいはスマートものづくりを意識しているオーディエンスに、有意義な情報が多くもたらされたのではないでしょうか。
この記事に関するお問い合わせ
-
入力フォームへ
当社はセキュリティ保護の観点からSSL技術を使用しております。