Jマテ.カッパープロダクツ株式会社と弊社(富士通フロンテック)は、ものづくりDXの実証実験を実施致しました。実証実験ではものづくりDXによる工場の可視化によって、Jマテ.カッパープロダクツ様の抱える課題の解決ができるかについて検証しました。
更に今後、製造業の持つ課題に弊社のものづくりDXで価値を提供していくことを目指します。本記事ではこの実証実験での取り組み内容をご紹介致します。
施策内容
タブレットによる工数データ収集・検査データのデジタル管理
セル生産ラインの各設備にタブレットを設置し、作業開始・完了をチェックすることで、作業に関連するデータを取得できるようになりました。
- 設備毎の着手~完了の時間取得
- 出来高
- 作業手順・注意事項指示
アンドン(異常表示灯)との連携・対応状況の管理
問題発生時にはアンドンと連携。原因と対応状況を入力することで、ラインで発生している問題の状況把握、管理ができるようになりました。
- 1日あたりのアンドン発生回数
- 問題対応に要した時間
ダッシュボードによる可視化
収集した各種データを、ダッシュボードに表示。
これにより、生産進捗状況、機種別工数、障害状況など、現場状況をリアルタイムで可視化。
実証実験結果
現場把握にかかっていた工数が大幅減少(1ラインあたり)
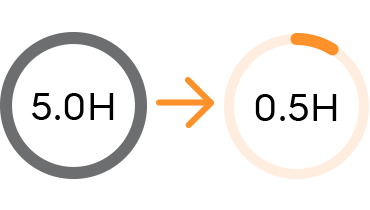
遠隔地からもリモートで現場状況を把握可能
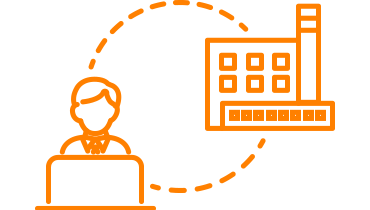
現場の改善すべきポイントを素早く発見
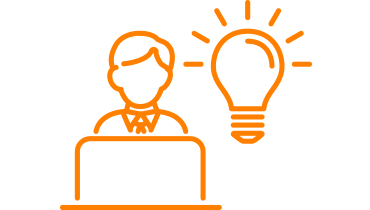
モデルラインにおける業務は
1時間あたりの出来高が向上
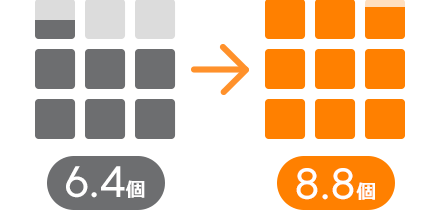
作業効率が37%向上し、残業削減と生産性向上に寄与
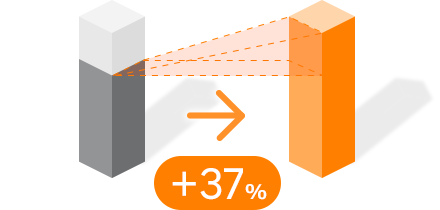
他工場(クビキ工場・産機工場)にもそれぞれモデルラインを追加
3工場に拡大して実施中
ものづくりDX実証実験のご紹介動画
インタビュー
ものづくりDXに取り組んだ経緯や取り組み内容についてお伺いしました!
Jマテ.カッパープロダクツ 株式会社
加工部 精機工場統括 副部長 小川 剛 氏
ものづくり改善やDXについてどういった課題がありましたか。
小川:生産活動をしながらの改善活動となります。
当然、過剰に人がいるわけでもありませんので改善する時間は時間外作業となってしまいます。
改善して楽にしていくはずですが、逆に改善に疲れてしまうことが課題でした。
貴社としてその課題解決に向けて取り組まれたことは何ですか。
小川:改善するには改善ポイントを把握することから始まります。
その問題点を見つけることにも労力を必要としますので、そういった部分を、今回の富士通フロンテックとの取り組みにより問題点が見つけられるようになりました。
弊社(富士通フロンテック)と共同で取り組むことにされた理由は何ですか。
小川:同じTPS(注)ベースでものづくりを行なっていたため、同じ目線、感覚で取り組みができるのではないかと思ったためです。
(注)TPS=Toyota Production Systemの略で、「トヨタ生産方式」を指します。生産ラインのムダを徹底的に排除するために確立された生産方式です。
今後どういった姿を目指していく予定ですか。
小川:この取り組みを定着化させ、人の活人化を目指し、製造部門、間接部門が一繋ぎになるような会社を目指していきたいです。
今後、弊社に期待されることはありますか。
小川:製造業といっても多種多様な工場があります。いかにその工場がやりたいことを実現できるかを一緒に考え、マッチしたシステムを構築していただきたいです。
もっと詳しく知りたい方、ご興味のある方は是非お問合せください!
Jマテ.カッパープロダクツ株式会社 様
本社所在地 | 新潟県上越市大潟区土底浜2024-1 |
---|---|
設立 | 2005年4月1日 |
事業内容 | 銅合金連続鋳造品・遠心鋳造品・押出品の製造加工販売、銅合金地金の製造販売、上水道配管部品、産業機械部品 |
代表者名 | 代表取締役社長 山本 耕治 |
ホームページ | https://www.jcp.joemate.co.jp/ |