サントリーと富士通は、流通業界における梱包段ボールの汚破損に起因する社会ロス削減を目指し、流通業界全体を巻き込んだ段ボール汚破損判定基準の初の標準化に取り組んでいます。
後編では本プロジェクトの発起人であるサントリーホールディングス(株)サプライチェーン本部 サプライチェーン改革推進部 専任部長の上前 英幸氏と、その想いにテクノロジーで応えた富士通(株)Uvance本部データサービス事業部 新サービス開発部でデータサイエンティストとして活躍する吉田 孟弘に流通業界全体を巻き込んだ社会課題解決を目指す前例のない取り組みがどのようにして生まれたのか、その開発秘話を伺います。
- 目次
流通業界全体を巻き込み社会課題解決を目指す前例のないプロジェクト
――お二人は本プロジェクトの発起人と伺っておりますが、流通業界を巻き込んでの梱包段ボールの汚破損判定に取り組もうと思われたきっかけを教えてください。
上前氏: 私は、サプライチェーンマネジメント部門で現場改善関連の担当をしています。流通業界における梱包段ボールの汚破損判定の問題は、かねてから解決すべき社会課題として悩んでいましたが、具体的な解決策が見えずにいました。
というのも、梱包段ボールの汚破損による持ち戻り・返品が引き起こす社会ロスについては、社内でも意識はされてはいるのですが、通常のシステム開発のようにROI(投資対効果)が明確でないことや、現場の状況がデータ化されていないため、マネジメント層からの理解を得づらいといった課題があり、なかなかプロジェクトを推し進められずにいました。
そんな中、たまたま富士通様にこの課題についてお話したところ、「AIを使ったソリューションが作れそうだ」ということになり、具体的にプロジェクトを進めていく形になりました。
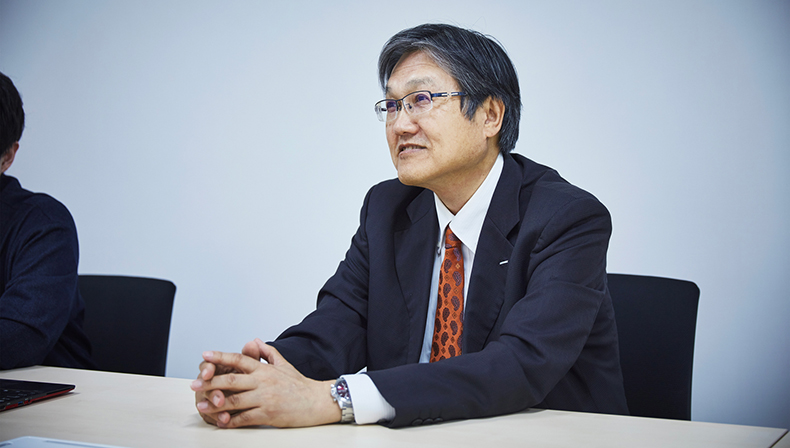
吉田: 私はデータサイエンティストとしてAIによる社会課題解決に関心があり、今回の案件は、まさにそこに当てはまるものでした。
しかし、日本ではROIの懸念から、AIプロジェクトへの投資が極端に少ないのが現実です。段ボール汚破損による返品が引き起こす金銭的なロスを考えれば数千万円以上の開発費は出てもいいはずなのですが・・・
――その壁を、どのようにして打ち破ることができたのですか?
吉田: 梱包段ボールの汚破損に起因する社会ロスは、流通サプライチェーン全体を巻き込んで取り組むべき社会課題です。そこで、まずはエコシステム全体のビジョンを描くところから始めました。
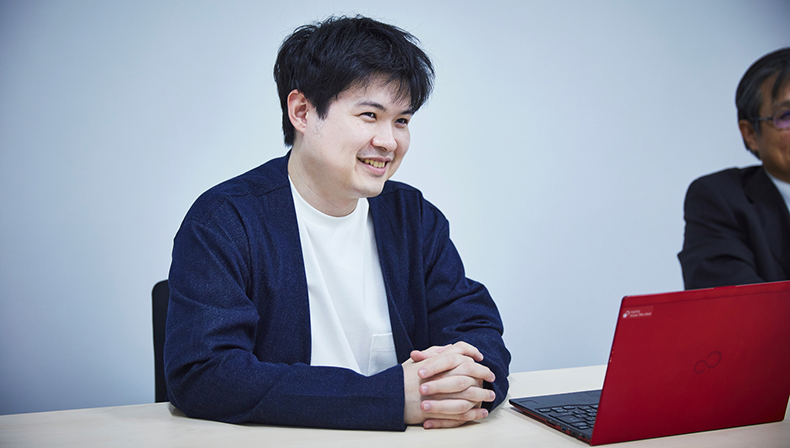
上前氏: 具体的には、単に段ボールの汚破損判定のためだけでなく、業界を巻き込んでさまざまな状況をデータ化して貯めていくことで、広く流通業界の関係者の個々の判断を標準化・統一化していく、「流通業務全体のDXにつなげていく全く新しい仕組みをつくるんだ」というストーリーです。これまでにない仕組みづくりのため、富士通様とはクライアントと開発者の関係ではなく、共同開発の形でプロジェクトを進めていきました。
梱包段ボールの汚破損判定には日本特有の文化や美意識も関係するため、国内事情やSDGsの取り組みに精通し、業界全体を巻き込む力にもなる富士通様は、心強いパートナーでした。
吉田: この仕組みは一社で完結するものでなく、流通業界全体に広まってたくさんのデータが集まることでやっと完成するものだと考えています。業界の巻き込みに関しては上前氏を中心に各団体や企業と交渉を進めていただいたのですが、経産省主催の「サプライチェーンイノベーション大賞2020」(※)において、優秀賞の受賞や積極的な広報活動により賛同者を増やしていく、その手腕は学ぶべき部分だらけでした。
- ※「サプライチェーンイノベーション大賞」とは、サプライチェーン全体の最適化に向け、製・配・販各層の協力の下、優れた取り組みを行い、業界を牽引した企業に対して、製・配・販連携協議会がその功績を表彰するもの。
AIと人の協調による汚破損判定
――具体的には、どのように段ボールの汚破損判定が行われるのでしょうか?
吉田: これまで現場の作業員の方が実施していた段ボールの出荷可否判断を、ディープラーニングにより自動化します。
具体的には、スマートフォン用の汚破損判定アプリを使い、現場の担当者に段ボールを撮影してもらいます。すると、画像解析により①破れや破損、②多湿時に側面が歪む胴膨れなどを分類します。
その結果をAIのレコメンドモデルで過去データと照らし合わせることで、過去の出荷可否判定結果が付随した5枚の類似画像をレコメンドします。
ただし、過去の担当者の判断のバラつきから、レコメンドのうち、3枚が出荷可、残り2枚が出荷不可と表示されることもあります。その場合には、撮影された写真と最も類似している画像を現場担当者が選定し、その判断結果をもとに出荷可否を判定するわけです。
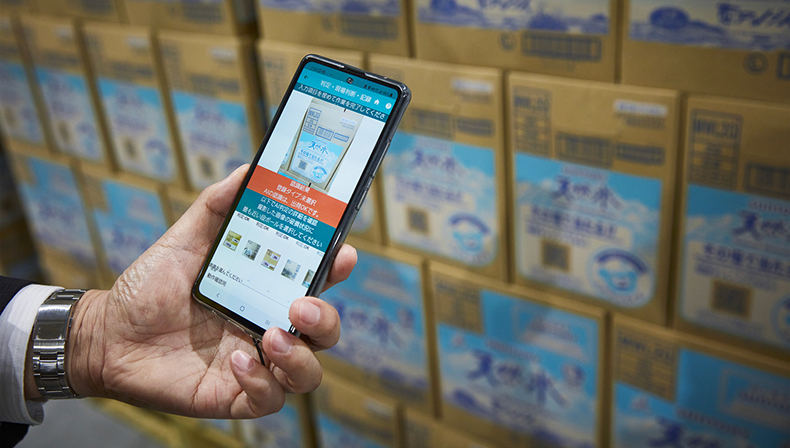
――AIの判定のみに頼るのではなく、人の判断も加えるということですね。
上前氏: AIの判断は過去の人間の判断がベースですから、厳しい担当者の判定が多ければAIによる判定も厳しくなりがちです。そこで、常に人間の判断を入れてAIの基準が更新されるようにしました。
吉田: 破損した段ボールの画像に加え、出荷にかかわる業務記録なども蓄積できるので、現場が抱える問題の見える化にもつながっています。
最終的には判定を完全自動化するにしても、そのための判定データは可能な限り多く蓄積しておく必要があります。AIと人が協調して判断する仕組みにしたのは、積極的な判定データ入力の動機付けにもなるからです。
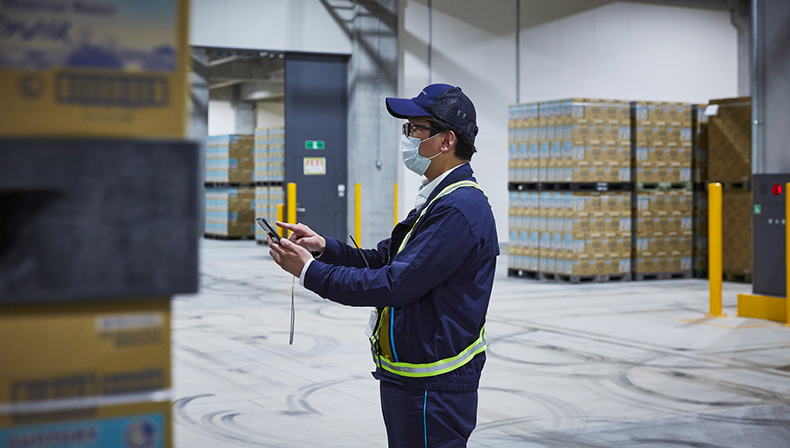
アジャイルな共同開発で現場を巻き込みPDCAをまわしていく
――仕組みづくりにあたり、どのような開発手法を採られたのでしょうか?
上前氏: 現場の状況をデータ化して関係者全体で客観的にPDCAが回せることや、メーカー間、流通企業間の判定基準の差などの種々の視点からの要望が出てくるという前提での開発でしたので、前例のない仕組みを作っていく必要がありました。そこで、ベンチャー的かつアジャイルな開発手法を採りました。これは、開発側と利用側で意見を順次加えながら開発を進め、アイデアをすぐに採り入れて、開発、試用、改善していくというものです。
吉田: とにかく試作アプリを作っては現場での使われ方を見ながら素早く改良していくというやり方を徹底し、PDCAサイクルの速度を落とさないよう心がけました。
現場から上がってくる不満点は、業務フローのデザインやアプリ全体のユーザービリティの改善にもプラスとなりました。
上前氏: 会議開始時にリクエストしたことが、会議終了時にはすでに実装されていた時には驚きました(笑)吉田氏との密なやり取りが欠かせなかったので、チャットでも頻繁にコミュニケーションを行い、アイデアをお互い出し合っては改善していきました。また、我々ユーザー側でもシステムテストを行うことで、テスト期間も圧縮できました。こうしたアジャイルでの改善が結果的にシステムの現場からの満足度アップや、業界の新規賛同者拡大・納得性につながったのだと考えています。
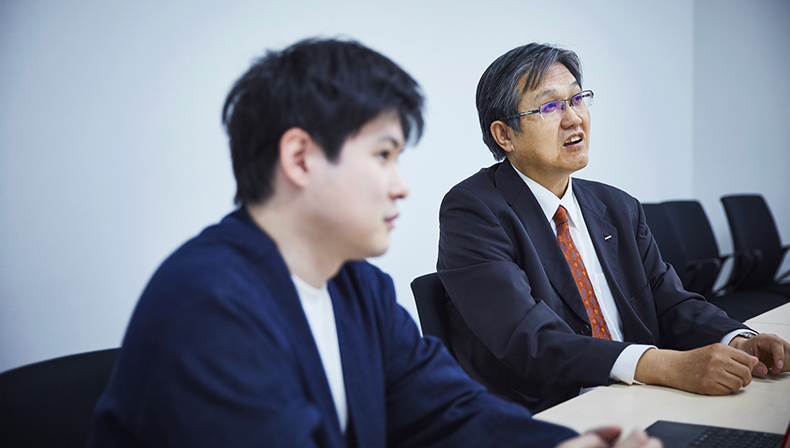
スマートフォンアプリの開発がプロジェクトの転機に。今も続くAI精度向上への努力
――通常とは大きく異なるソリューション開発を進めるにあたり、直面された問題もあったのではないでしょうか?
上前氏: AIに学習させて精度を上げるためには、大量のサンプル写真が必要です。当初はPCに個々の撮影サンプルを集めていたため、マシンを現場に持っていったり、現場から写真を送ってもらったりして何とかAIモデル検証をしていたのですが、それでは小回りが効かず、議論も進みませんでした。そこで、現在のスマートフォン向けアプリに切り替えて解決した経緯があります。
吉田: こういった実証実験では、PC上で小さくやることが一般的です。一方で、各社が自由に使えるPCの調達が難しいこと、また物理的に重く、使い勝手のフィードバック以前で話が止まってしまうことから思い切ってスマホアプリを作ってしまうことにしました。この作戦で状況は大きく変わり、各自のスマートフォンを手に取って自由に操作できる環境が整い、どのように業務フローが変わるのかを関係者全員が具体的に把握できるようになりました。
――現在は段ボール汚破損の判定精度を高めているフェーズとのことですが、具体的にはどのようにされているのでしょうか?
上前氏: AIが汚破損の種類を特定する「破損タイプ精度」と、5枚のレコメンド写真の中に、判定対象と近似する写真が何枚あるかという率を見る「選択精度」の両面から詰めている最中です。現場でも、撮影した段ボール上の汚破損箇所に注釈コメントを付けていくアノテーション作業を実施するなどの方法で、精度向上の努力をしています。
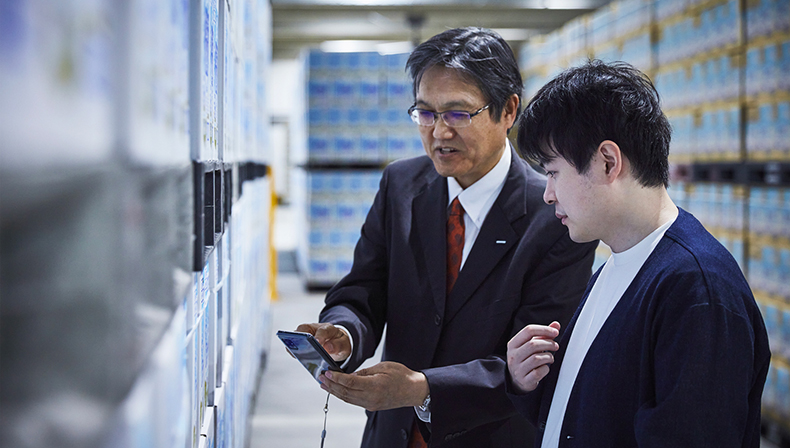
多くの社会課題解決を目指して
――このプロジェクトの将来像はどのようなものでしょうか?
吉田: 今、集まっている汚破損サンプルの写真は約1000枚ほどですが、5000枚程サンプルが溜まった段階で、自動検品用のモデルが作れるものと予想しています。
その頃には、議論もさらに進め、たとえば同じ穴あきの破損でも位置によって出荷可否判定に与える影響が異なるので、そこまで踏み込んで判定できるようにするつもりです。さらには、時期や状況による統計的な情報をアプリのダッシュボードに表示して、汚破損が起こりにくい置き方のアドバイスなども可能にしていきたいと思っています。
上前氏: 新しい倉庫が加わるだけで現場担当者の判断が異なり、精度が下がることもあるほど、AIと人の判定は繊細です。だからこそ、流通業界全体が協力して一定の判定基準に従うことが大切だと考えています。良い人間関係と同様、AIと人が互いに認め合えるように開発を進めていますので、1日も早く誰もが納得できる判定を実現したいですね。
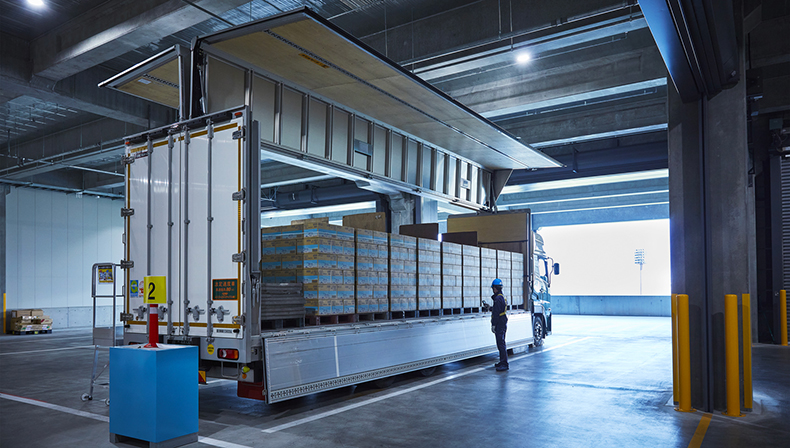
――最後に、これからの技術と社会の関係や、社会貢献への思いなどをお聞かせください。
吉田: 両利きの経営の理論では、企業が生き残っていくための対象となるテーマや解決手法を見つける「知の探索」と、既存事業を改善していく「知の深化」の両方が必要だと言われています。このうち探索への投資が、日本ではROIの根拠立てを強く求められ、おろそかになりがちです。この問題を解決するためには、根拠を描くための下書き、つまりベースが必要です。だからこそ、今求められているのは、さまざまな社会課題に対してソリューションになりそうな仕組みを限られたコストの中で素早く広く全体がわかるように「具体的なスマホアプリなどのモノ」を作り、その先が見えるようにすることだと考えています。この作業によって、AIに付随する人やアプリケーションとの作用が明確になり、単なる人の代わりのAIプロジェクトは業務フロー革新プロジェクトに昇華します。また、プロジェクトの最中で関わった皆がモノを触っているので、ROIの具体的な根拠を皆で持ち寄り、本格的な投資に踏み込めるという進め方が大事だなと考えています。
上前氏: AIによってあいまいな判定が改善されるということは、従事者間のもめ事が減るということでもあり、流通業者の信頼度の向上にもつながります。しかし、現場にしかわからないノウハウをソリューション開発に活かすには、業界全体の協力が不可欠です。共創によってコスト面も含めた壁を乗り越えた本プロジェクトのあり方が、さまざまな社会課題解決の前例になればよいですね。
たとえば、飲料の梱包段ボールの汚破損問題に限らず、流通業界にはフォークリフト運用における安全管理など、解決すべきテーマがいくつも存在しています。今回の取り組みは、それらはもちろん、他の業界が抱える課題に対しても十分応用できるものと期待しています。
突き詰めれば、SDGsの観点から消費者の皆様にも梱包段ボールの役割を見直していただき、広く社会で、輸配送や使用に支障がない範囲の軽度の汚破損が許容されれば、究極的にはAIによる判定ソリューションが、その役割を終えることさえ夢見ています。
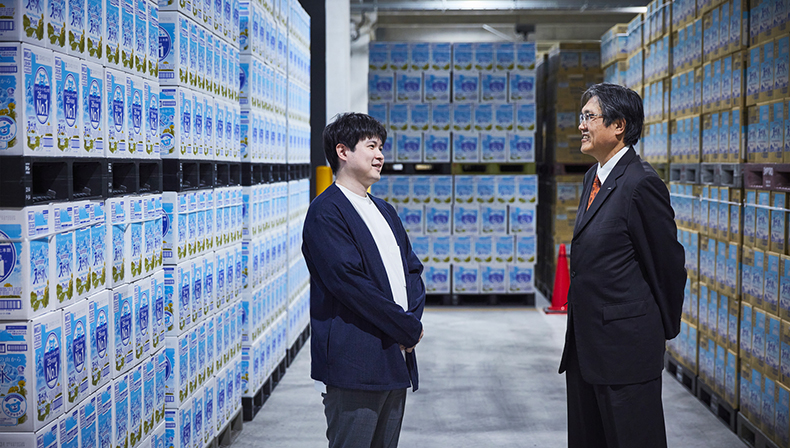
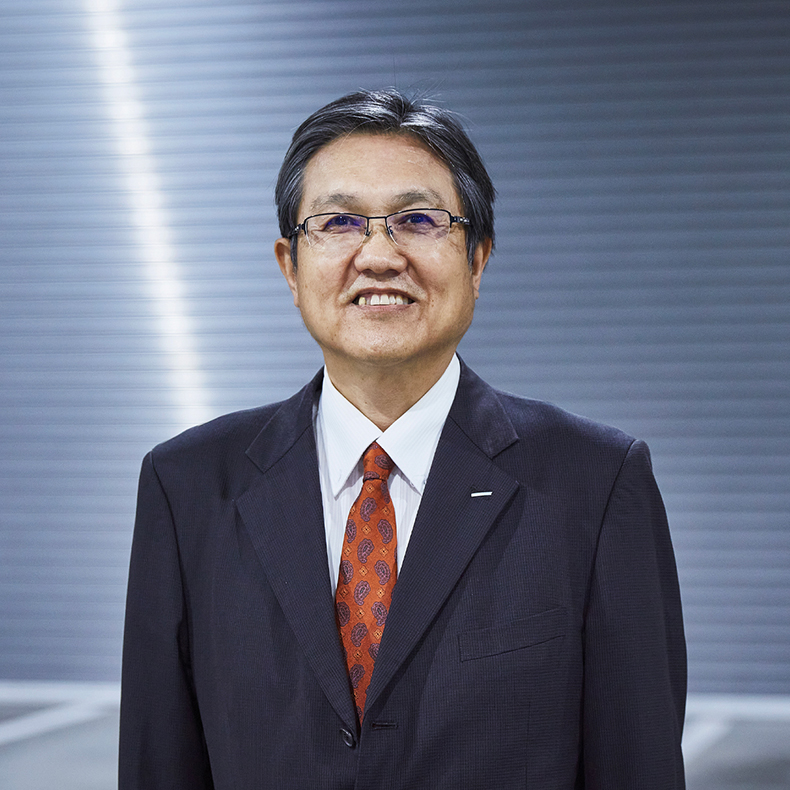
サントリーホールディングス株式会社
サプライチェーン本部
サプライチェーン改革推進部 専任部長
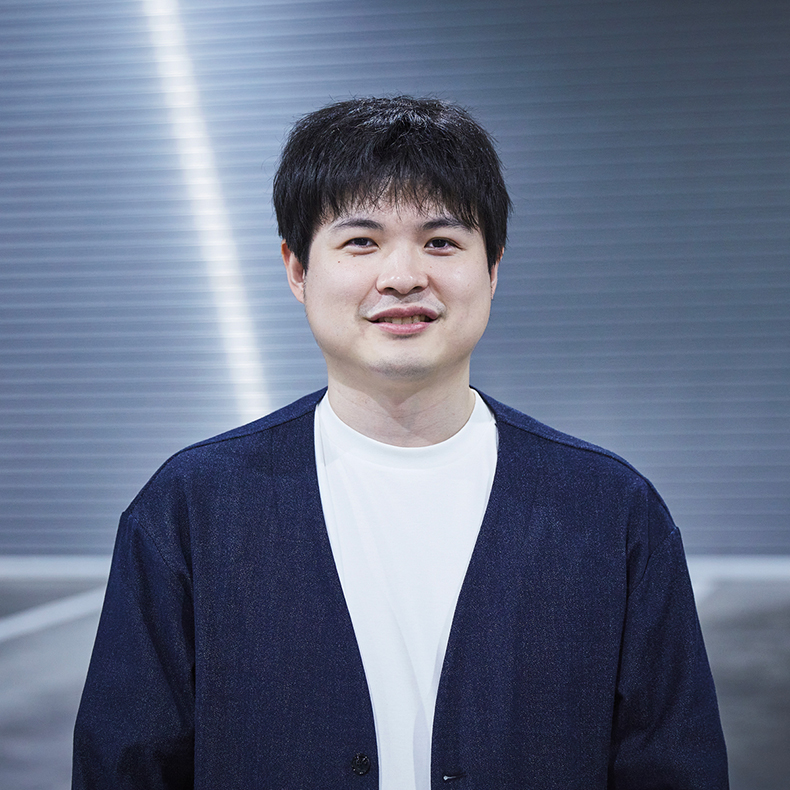
富士通株式会社
Uvance本部データサービス事業部
新サービス開発部 データサイエンティスト