Subaru Corporation (hereafter referred to as Subaru), a company that takes on the challenge of manufacturing with cutting-edge technology, is implementing digital transformation (DX) innovation that uses an AI model jointly developed with Fujitsu to accurately judge the quality of grinding for engine parts to support mass production operations. To find out more about this innovation, Fujitsu Evangelist Koji Takeda visited Subaru’s Oizumi Plant at the Gunma Manufacturing Division to hear first-hand accounts from the factory floor.
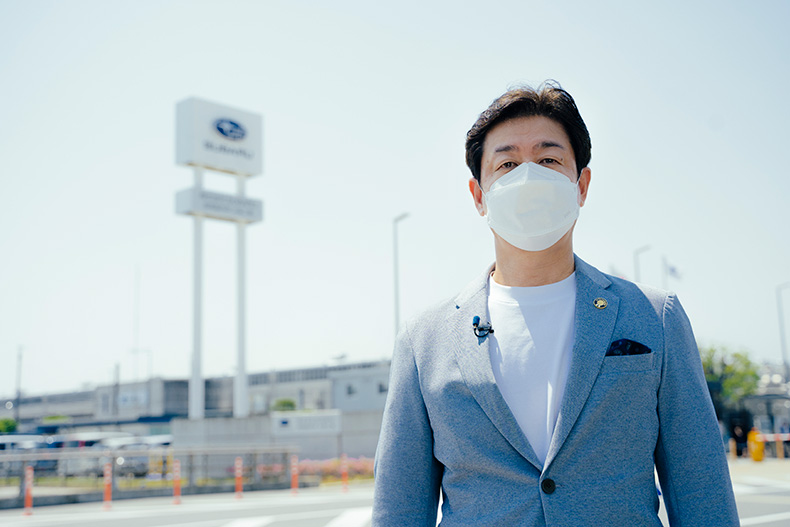
- Table of Contents
Improving Automotive Production for a Better World
For this article, we visited Subaru’s Oizumi Plant, which is part of its Gunma Manufacturing Division. This is a power unit plant that primarily manufactures automobile engines and transmissions on a large site of approximately 300,000 square meters. The plant is at the heart of Subaru with plans to establish a new production base for electric vehicles (EVs) at the site by 2027.
We spoke with Suguru Ohba, the head of Subaru’s DX project, who led planning, execution management, and DX human resources development, about Subaru's vision and his thoughts about this collaboration.
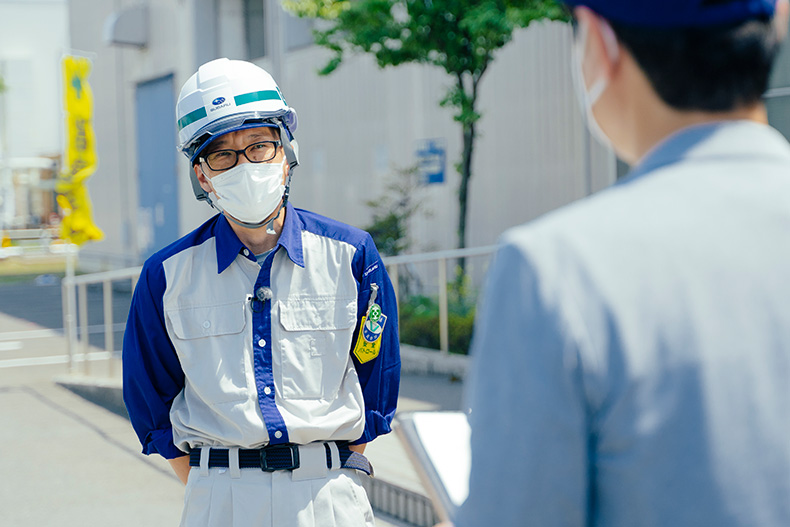
Takeda: Subaru's aspiration is to become a company "delivering happiness to all". What are you doing to achieve this purpose?
Ohba: Our main goal is to deliver safe and reliable products to our customers. Since I am in charge of manufacturing, I am committed to delivering high-quality products to our customers to ensure them trouble-free service.
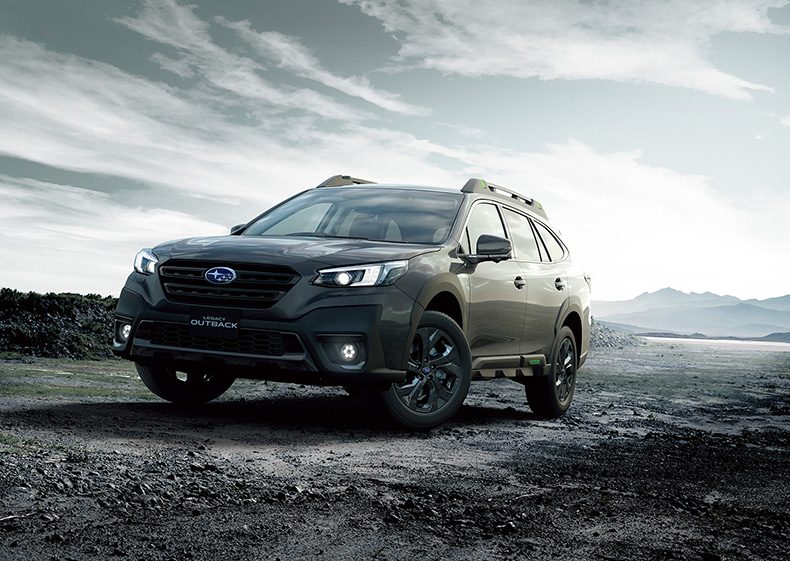
Takeda: I see. The automotive industry is said to be in the midst of a period of once-in-a-century upheaval. What are the challenges facing the industry?
Ohba: The first and most pressing issue is the shift toward EVs. And in terms of overall work styles, such as workforce availability and diversity, we as engineers are faced with the challenge of creating a system that can produce high-quality products no matter who is in charge.
Takeda: Subaru announced its mid-term management vision, STEP, in 2018. Please give us an overview of what that is all about.
Ohba: Within STEP we have set "quality" as the number one priority and are implementing manufacturing quality reforms. The mission for the manufacturing side is to guarantee quality in the manufacturing process and to raise our level of "own-process assurance" so that no defective products are passed on to customers or even to subsequent manufacturing processes downstream. Beyond that, I would like to contribute to manufacturing in Japan by creating a production line that produces only high-quality products and produce a new and improved quality assurance method using data.
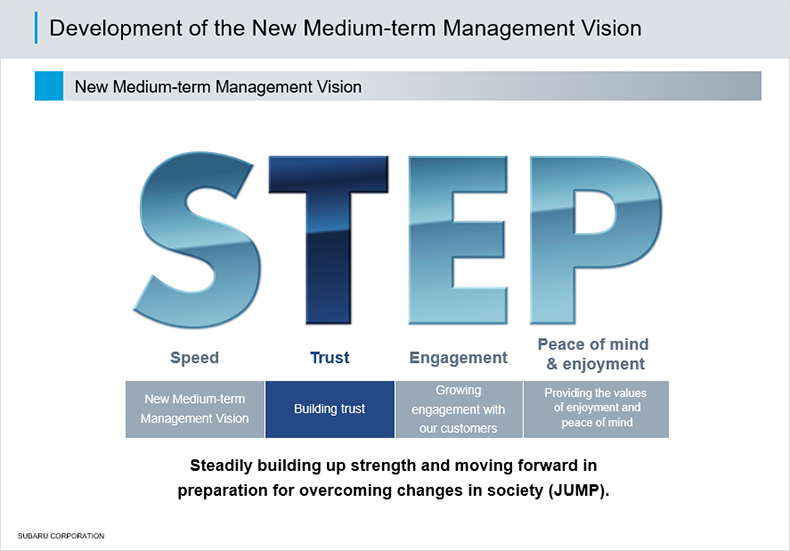
Takeda: As part of a leading company in the manufacturing industry, I share your devotion to the pursuit of higher quality. What challenges have you taken on as part of STEP?
Ohba: This time, rather than simply increasing the number of people and instruments conducting inspections, our challenge was to "ensure quality while maintaining productivity by using AI data."
Takeda: Why did you choose to team up with Fujitsu?
Ohba: In the beginning, we were struggling with analyzing the correlation between quality and the multiple factors that affected this. A number of vendors tried to sell us correlation analysis software and AI, but they weren’t convincing. At that time, rather than giving us a typical sales pitch, Fujitsu approached us proposing a unique collaboration involving "people" and "technology" in which we were able to actually get inside the factory and work on a solution together.
The Challenge of "Co-creating" by Integrating On-site Knowledge and Data Knowledge
The mission of this collaboration, which began in 2018, is to produce an AI model that can accurately judge the quality of the grinding process in the production of camshafts, the component responsible for opening and closing the valves in the car engine. We spoke with Manabu Shiota, Senior Manager of the Fujitsu Manufacturing Solutions Division, who was in charge of coordinating and directing the project team.
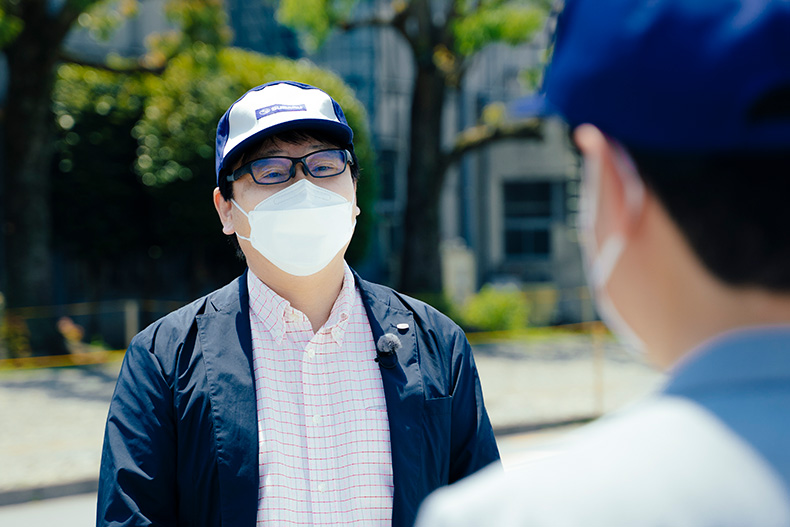
Takeda: What were your thoughts in undertaking this project?
Shiota: AI projects often end in the proof of concept (POC*) stage. However, my personal motivation is to never give up on anything, to push forward with the customer with a goal in mind, and to be happy with the results. In this project I was deeply committed to introducing AI into the manufacturing process in order to achieve Subaru's goal of improving the level of manufacturing quality assurance. We undertook the project in a way where we could set clear short-term targets together with Subaru while keeping in mind the need of adapting to the actual conditions on site as we progressed.
- *The verification of new technology in the pre-development stage.
Takeda: It sounds like a new form of collaboration in which you learned and built together with the client rather than simply asking them to use our existing products.
Shiota: That’s right. It really was "co-creation". As data analysis professionals, we at Fujitsu provided feedback to Subaru on how we analyzed the data. Subaru, on the other hand, shared their knowledge from the field with us so that we could use that to improve our data analysis capabilities. The manufacturing professionals and data analysis professionals engaged in friendly competition with each other on an equal footing. We really surprised them at the time of our first proposal because, even though we had no on-site knowledge at the time, based on our analysis we identified some data that correlated with processing quality and we explained that to them. When the Subaru team heard this, they looked at us and said, "How did you know that!" I still remember the look on their faces. That was the beginning of this co-creation project.
So, what does the high-accuracy AI model look like exactly? We talked to Kenta Ishiwaki, Manager at Fujitsu's Manufacturing Solutions Division, who is the AI developer.

Takeda: What are the features of this high-accuracy AI model?
Ishiwaki: The AI model predicts the surface roughness and shape of camshafts with high accuracy and in real time based on sensor data from each machining facility. It can also provide real-time information about wear to the grinding wheel tool that is used in machining. Furthermore, these AI models can be centrally managed using the COLMINA Quality AI Operation Management Package, which in the case of Subaru is operated on their own servers.
Takeda: I see. So, what was your mission for this project?
Ishiwaki: Since we are a manufacturing company, our highest goal is to ensure quality in the product. For that reason, we worked together with the Subaru team on site rather than from behind a desk in order to use data analysis for problem solving. We took the data from areas related to product quality and verified these results in order to teach the AI. Throughout this process, we were committed to the goal of digitally transforming the production process. We took on the challenge of developing a high-accuracy AI model that could realize continuous manufacturing and evaluation simultaneously on a mass production scale, which is quite a substantial feat.
Takeda: How will the digital transformation of production processes with AI models contribute to the manufacturing industry?
Ishiwaki: In manufacturing processes, including those for automobiles, there are work processes for production and subsequent inspection processes, and there are cases where the production process is wasteful because it is not possible to determine the accuracy and quality of the products until they reach the inspection point. This high-accuracy AI model enables simultaneous manufacturing and evaluation in order to remove defective items at the point of production and eliminate the loss of materials, parts, and labor.
Takeda: So, this AI model contributes not only to manufacturing efficiency but also to the environment. Could you tell us about some of the moments that stood out during the collaborative development of the model?
Ishiwaki: Camshafts are relatively consistent in shape, however, there are differences in the data we collected depending on the size of the camshaft. The Subaru team was able to identify the errors in the manufacturing process based on their knowledge of the field, and we used that practical knowledge as a hypothesis to extract and analyze data based on logical knowledge in order to build an AI model that we could control in common. However, we had to re-create the model from scratch because it didn’t perform well initially. That was a painful experience. The reason we were able to overcome this obstacle is because Subaru appreciated our attitude of thoroughly investigating the cause of the problem and never giving up. I feel that in order to convince the personnel working on site, AI engineers must stand in the client's shoes and be close to them, so that we can synchronize our thinking and realize co-creation in the truest sense. That’s one thing I learned during this project.
High-accuracy AI Models Contribute to Quality Assurance and Cost Reduction
The high-accuracy AI model was tested from 2019 to 2020, followed by the development and demonstration of the COLMINA Quality AI Operation Management Package for mass production operations, which was conducted over a period of one year and four months starting from 2020. The full-scale operation of the AI model began in January 2022. We visited the site where two production lines grind camshafts for approximately 1,500 cars per day and heard about the benefits of this process.
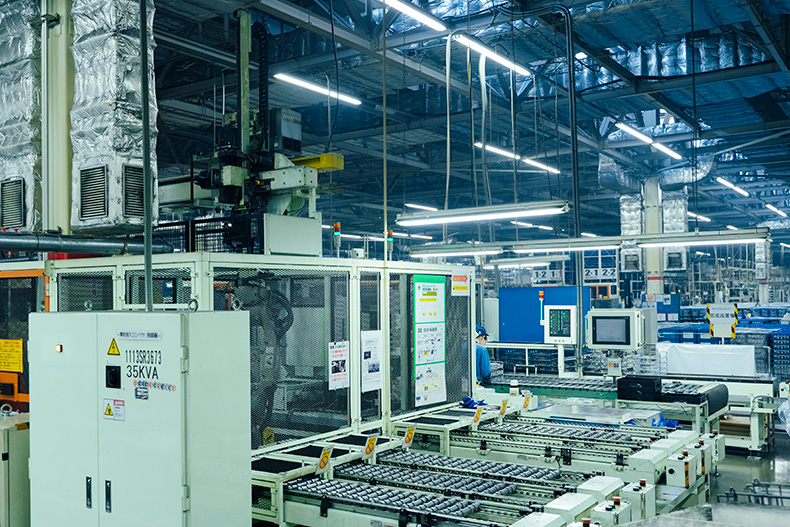
Takeda: How do you think the workers here like this AI technology?
Ohba: We used to visually inspect and perform sampling measurements for all the products that came off this line so we were surprised that this technology can predict the quality of products at the moment of processing without actually measuring the products just by utilizing sensor data. The accuracy of the prediction, which is constantly being checked, is very high. In addition to increasing the quality assurance of our camshafts, we believe this system is of great value because we have achieved a proven track record for full-scale operation on the production line and we have created a model case that includes the process of technological development.
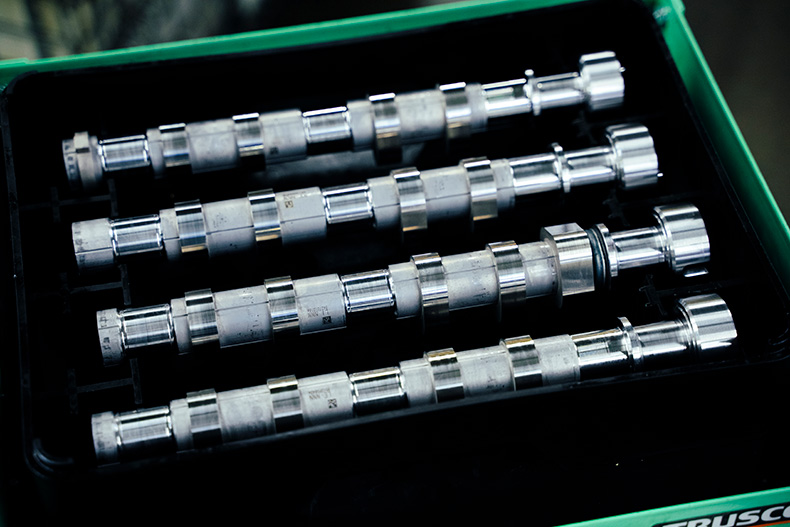
Takeda: That's very kind of you to say. What are the factors that you think led to these results?
Ohba: During the development process both companies learned from each other's areas of expertise and through daily discussions we combined our respective areas of know-how to undertake the project. This is what led to the results we achieved this time. I truly believe that we are now one team, beyond the framework of a single company.
The Desire to Contribute to Sustainable Manufacturing
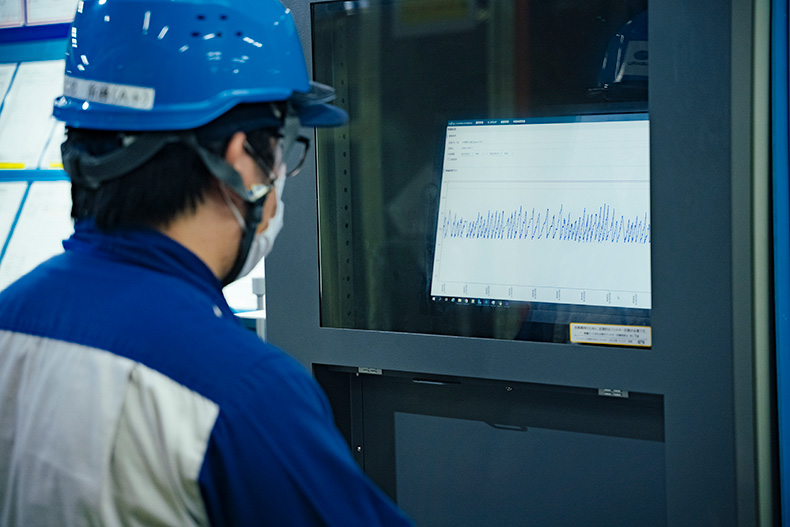
Subaru and Fujitsu are thinking about more than just grinding camshafts, they intend to use AI technology and the Internet of Things to take on other challenges too. So, what are they planning exactly?
Ohba: We are continuing to check the accuracy of our quality assurance predictions and are aiming to eliminate visual inspection within fiscal year 2022. We would like to firmly establish this as a new production line model for quality assurance and expand it horizontally to other plants such as those producing the car body and other parts as well as achieve quality reform by increasing the number of personnel who can plan and undertake DX like this project. In the manufacturing industry as a whole, I would like to contribute to the improvement of Japanese technology by spreading new technologies and help develop sustainable manufacturing as well.
Takeda: I think that this collaboration is a major step toward technological innovation in manufacturing. What do you expect from Fujitsu in the future?
Ohba: We will continue to transform manufacturing together by utilizing new technologies.
Takeda: Let's do it. So, again, what is Subaru's goal for manufacturing?
Ohba: I feel that there is no end to improving quality, but I would venture to say that our customers choose Subaru for our quality. As an engineer, I will continue striving for that high level.
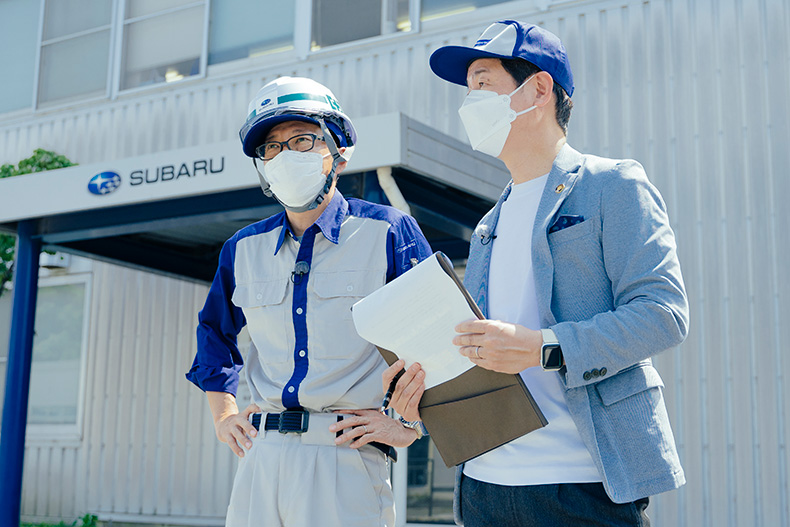
Fujitsu is committed to contributing to Japan's manufacturing industry. Let’s see how that looks.
Takeda: What kind of contributions do you think this high-accuracy AI model has made?
Shiota: I believe that we have contributed to Subaru's goal of improved quality by establishing a manufacturing system that eliminates defective products as well as a service that manages and operates this system on site. I would like to further improve the quality of automotive manufacturing by making these systems widely available, and ultimately contribute to the goal of zero automobile accidents.
Finally, we talked with Atsushi Yamamoto of the Fujitsu Manufacturing Solutions Division, who is involved in this project and other product developments as well as the creation of mechanisms for sustainable AI utilization in the field of manufacturing.
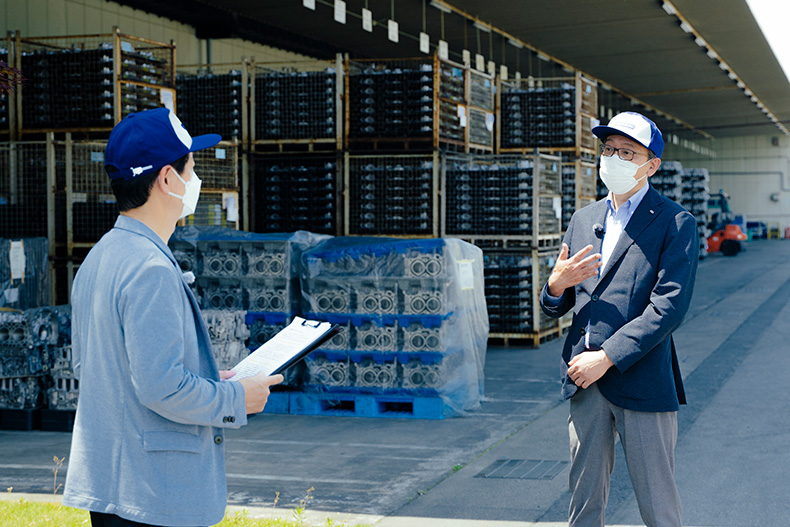
Takeda: What were your thoughts on being involved with this project?
Yamamoto: My personal purpose is to bring digital technology to manufacturing sites all over the world in order to make Japanese manufacturing more resilient. Our product developers want to solve problems within the manufacturing industry. This sentiment has been particularly strong as we have been involved in the automotive industry, which is at the top of the Japanese manufacturing industry, and as we have been involved in co-creation projects with Subaru, a company that has a strong commitment to unique automotive manufacturing and quality.
Takeda: What is the outlook for Fujitsu's digital technology in the manufacturing industry, including this AI model and COLMINA, which were commercialized in this field?
Yamamoto: The goal is not to develop new, high-accuracy AI models. What is important is to introduce the models we already have to manufacturing sites and provide support for their operation and maintenance, thereby expanding the areas of sustainable use by our clients. We believe that this will lead to sustainable manufacturing, which is a key focus area for Fujitsu. Sustainable use of AI will not only help solve the shortage of DX human resources, but also help solve issues such as the automation of tasks previously carried out by humans and the loss of expertise in the workforce.
We are committed to developing even more attractive products to help solve challenges within the manufacturing industry.
Takeda: This report from the frontline of digital innovation in the automotive industry made me realize anew how important it is for both parties to share a perspective and work together toward a common goal rather than simply having an IT vendor "provide" a product and a manufacturer "apply" it. Thank you for your time today.
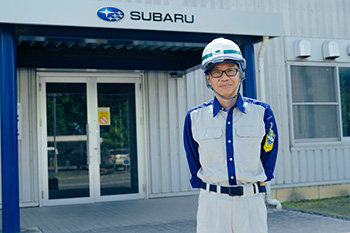
Manager, DX Planning, Manufacturing Engineering Management Department, Manufacturing Division, Subaru Corporation
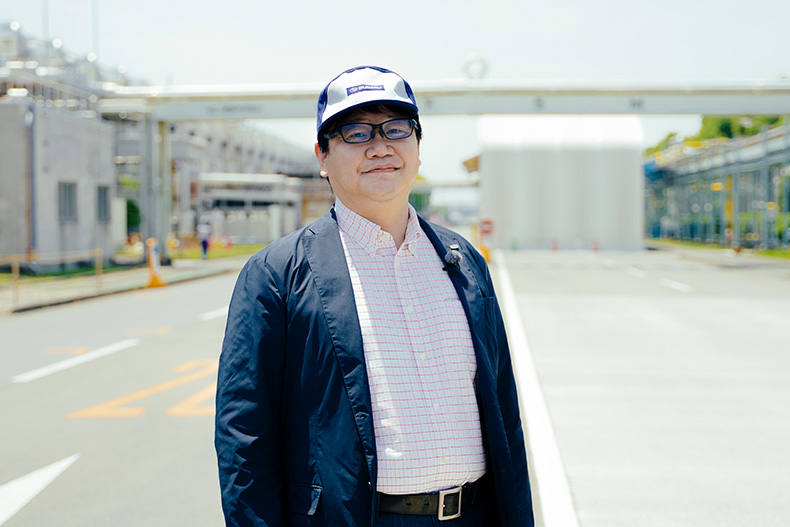
Senior Manager, Manufacturing Solutions Division, Fujitsu
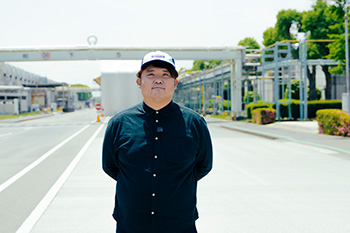
Manager, Manufacturing Solutions Division, Fujitsu
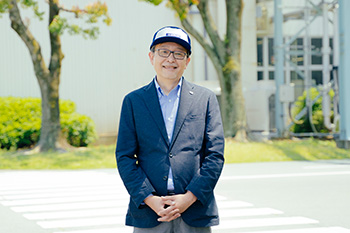
Manufacturing Solutions Division, Fujitsu
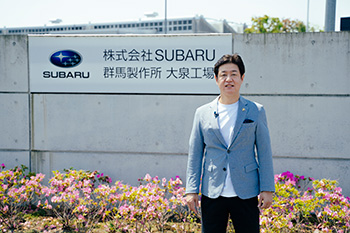