ものづくりに最先端テクノロジーで挑む株式会社SUBARU様(以下、SUBARU社)は、富士通と共同開発した「COLMINA現場品質AI運用管理パッケージ」で、エンジン部品の研削加工の品質を高精度に判定し、量産運用を実現するDX改革を推進しています。その革新性を探るべく、富士通エバンジェリストの武田幸治がSUBARU社の群馬製作所 大泉工場を訪れ、現場での生の声を取材しました。
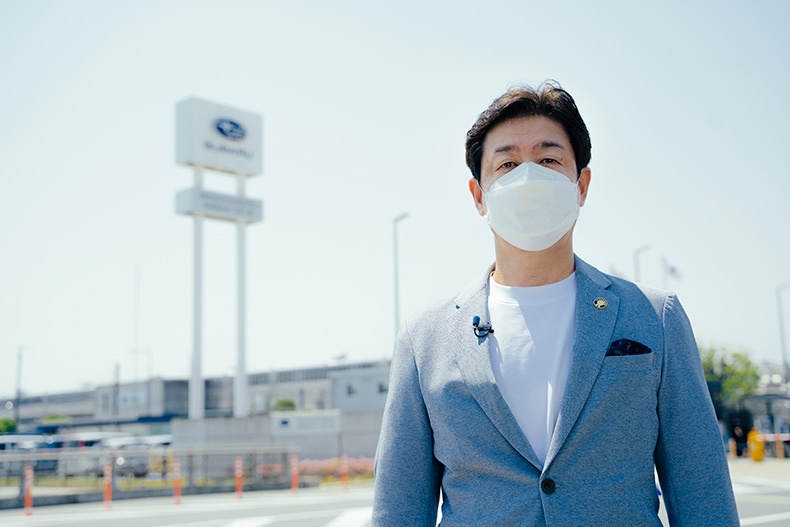
- 目次
自動車生産の最前線が目指す世界と課題
今回訪れた群馬製作所 大泉工場は、約30万㎡の広大な敷地を持ち、主にエンジンやトランスミッションなどを製造するパワーユニット工場。2027年にはEVの新たな生産拠点の設立も予定されている、言わばSUBARU社の心臓部です。
今回のプロジェクトにおいて企画から実行のマネジメント、DX人材育成を主導した同社DX企画主査の大庭卓氏に、SUBARU社のビジョンや今回の協業への思いについてお聞きしました。
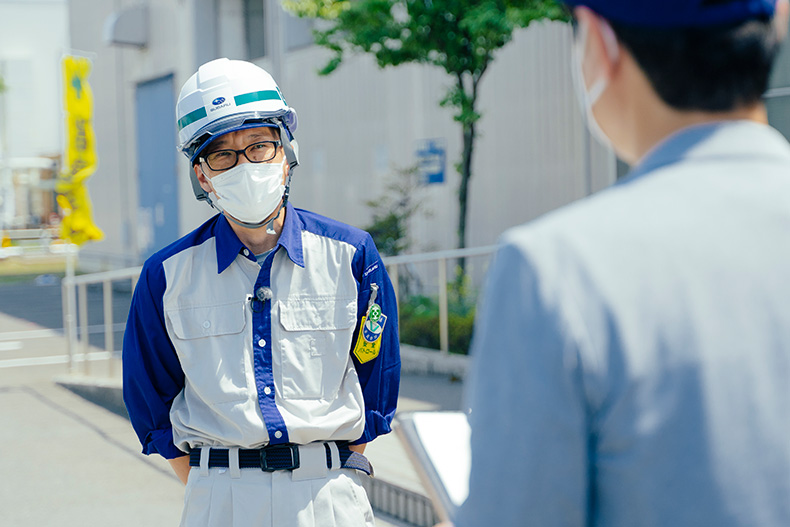
電動車両生産技術部 DX主査兼生産技術統括部
DX企画主査 大庭卓氏
武田: SUBARU様のありたい姿は「笑顔をつくる会社」ということですが、大庭さんはそのパーパスに向けてどのような取り組みをされていますか?
大庭氏: 私たちは、お客様に安心・安全な商品をお届けすることを一番の目標に掲げています。その中で私は製造を担当しているので、高品質なものをしっかりお客様にお届けし、迷惑をかけないようにすることが何より大事なことだと考えて取り組んでいます。

武田: なるほど。自動車産業は今、100年に一度の大変革期と言われていますが、業界の課題はどういったところにありますか?
大庭氏: まず急務となっているのが、電動化への対応。そして労働力の確保やダイバーシティなど働き方全体で、我々エンジニアとしては、誰が担当しても高品質なものをつくることができるシステムづくりが課題になっています。
武田: SUBARU様は2018年に中期経営ビジョン「STEP」を発表されましたが、概要を教えてください。
大庭氏: 「STEP」では“品質”を取り組みの一丁目一番地に定め、ものづくりの品質改革を実行しています。製造側としてのミッションは、製造工程において品質を保証し、お客様はもちろん後工程へも悪いものを渡さない「自工程保証」の格上げです。その先には良品しか製造できないラインをつくり、データの活用によって従来とは違う高次元の品質保証方法を構築することで、日本のものづくりに貢献したいと考えています。
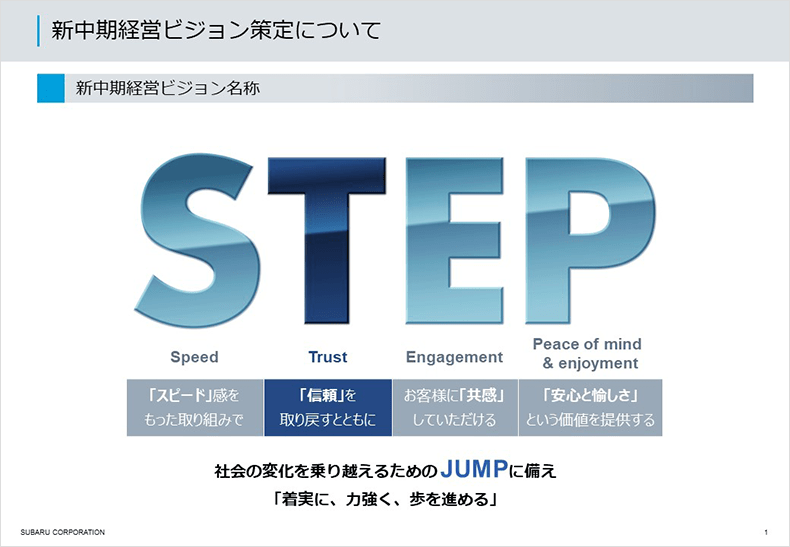
武田: 製造業をリードされている企業として、さらなる高品質を追求される姿勢に共感します。その「STEP」を受けて、今回チャレンジされたことを教えてください。
大庭氏: 単に人や計測器を増やして検査をするのではなく「AIデータの活用でいかに生産性を維持しつつ品質を確保するか」という点が新しい挑戦でした。
武田: なぜ富士通をパートナーとして選ばれたのでしょうか?
大庭氏: 当初、品質とそれに影響する複数の要因データとの相関分析の部分で苦労していて、様々なベンダーさんから相関分析ソフトやAIの売り込みがありましたが、上手くいきませんでした。そんな時に富士通さんから、単なる商品の売り込みではなく「人」と「技術」を介した他にはない協業の提案があり、実際に工場に入ってもらい膝をつき合わせ、“一緒に創り上げる”取り組みができたことが一番大きな理由です。
現場知見とデータ知見を融合させた“共創”への挑戦
2018年より始まった協業のミッションは、エンジン部品の一種でバルブ開閉の役割を担うカムシャフトの研削加工の品質を高精度に判定するAIモデルを構築すること。そのプロジェクトを円滑に進めるために、メンバーの連携や舵取りをリードした富士通 ものづくりソリューション事業部 シニアマネージャーの塩田学に話を聞きました。
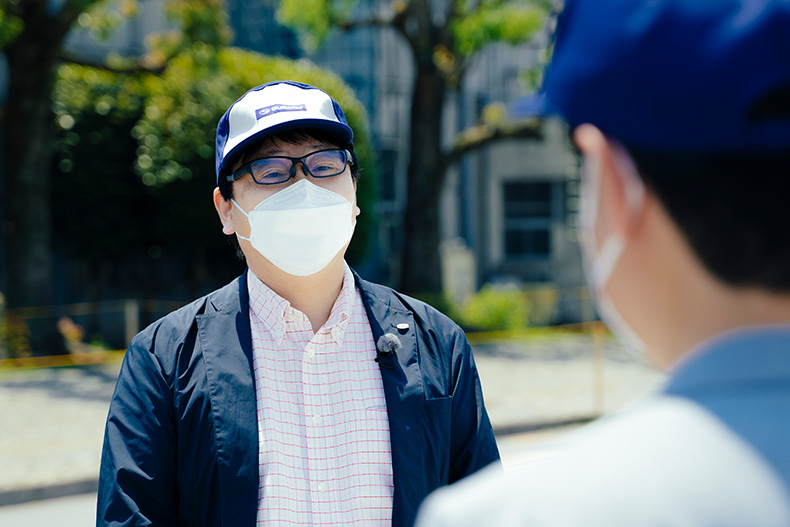
富士通株式会社 ものづくりソリューション事業部
シニアマネージャー 塩田学
武田: 今回、どのような思いでこのプロジェクトを推進されましたか?
塩田: AIのプロジェクトはPOC(※)で終わることも少なくないのですが、私のパーパスは「何ごとも諦めず、目標をもってお客様と邁進し、成果を出して喜び合う」こと。今回は、何が何でも製造現場へAIを導入し、その成果としてSUBARU様の掲げた製造品質保証レベルの向上に貢献したいという強い思いがあったので、“現場”に適応するイメージをもちながらSUBARU様と一緒に考え、悩み、議論し、短期間の目標を設定してクリアする方法で推進しました。
- ※新しい技術の、開発の前段階における検証のこと
武田: お客様に既存の製品を活用していただくのではなく、共に学び構築する、これまでにない協業のカタチだったのですね。
塩田: そうですね。まさに“共創”です。富士通はデータ分析のプロとして、SUBARU様にどのように分析したかという部分をフィードバックする。一方でSUBARU様は現場の知見を我々に伝え、それらを得てデータ分析の能力を向上させる。製造のプロとデータ分析のプロ同士が、同等の立場で切磋琢磨しました。初回提案の際に、我々が、現場知見がないにも関わらず、分析をもとに加工品質に相関するデータをピックアップして説明した時、「どうしてわかったのですか?」と驚かれたのが今でも忘れられません。それがきっかけで共創プロジェクトが始まりました。
実際に、今回の高精度AIモデルとはどのようなものなのか。AIの開発者である富士通ものづくりソリューション事業部 マネージャーの石脇健太に話を聞きました。
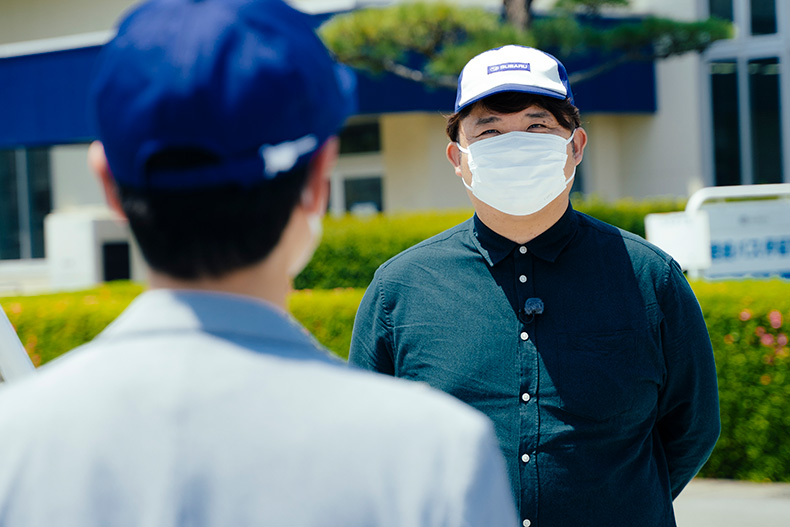
マネージャー 石脇健太
武田: 今回の高精度AIモデルの特長を教えてください。
石脇: 各加工設備に紐づいたセンシングデータをもとに、カムシャフトの表面の粗さと形状を高精度かつリアルタイムで予測を行うAIモデルです。また、加工に使用している砥石の摩耗具合をコンディションベースでリアルタイムに推論することもできます。さらにそれらのAIモデルは「COLMINA現場品質AI 運用管理パッケージ」によって一元管理することが可能で、SUBARU様の場合は自社のサーバーで運用されています。
武田: なるほど。このプロジェクトにおいて、石脇さんのミッションはどういったものだったのでしょうか?
石脇: 製造業ですので、目指すところは品質を担保するというミッションは当たり前ながら、机上ではなく現場でSUBARU様と共に課題解決につながるデータを分析し、品質に寄与する部分のデータを使用したAI学習とそれらを検証することを重視しました。その中で、常に意識していたのは「生産プロセスをDXする」こと。量産という規模で、継続的に製造と評価を同時に実現する、世界でもまれな高精度AIモデルの開発に挑戦しました。
武田: AIモデルによる生産プロセスのDXは、製造業にどのように寄与するのでしょうか?
石脇: 自動車を含む製造業の生産プロセスには、生産するための作業工程とその後に検査工程があり、生産されたものは精度や品質が悪いものがあっても、最後の検査工程に辿り着かなければ判断できず、無駄な加工が行われているというケースが存在します。この高精度AIモデルにおいては、製造と評価を同時に実現することで、製造の時点で悪いものを取り除き、部材や部品、作業時間のロスをカットすることができます。
武田: 製造効率だけでなく、環境面にも寄与するAIモデルなのですね。協業での開発において印象に残っているエピソードを教えてください。
石脇: カムシャフトの形状は似ているのですが、大きさによって収集するデータ内容に違いが出てきます。その誤差をSUBARU様は現場知見から知恵を出し、我々はそれを仮説として論理知見からデータを抽出、分析し、共通的に制御できるAIを構築することができました。ただ、一度つくったモデルが誤った結論に至ってしまったために、一からつくり直したのは苦しい経験でした。けれども、その壁を乗り越えられたのは、原因を徹底的に追究して諦めずに検討する姿勢をSUBARU様に評価していただけたからです。今回の取り組みを通して、現場の皆さんに納得していただくためにはAIエンジニアこそお客様の目線に立ち、寄り添うことで思いが一つになり、本当の意味で共創が実現できたと実感しています。
高精度AIモデルが品質保証とコスト削減に貢献
今回の高精度AIモデルは、2019年から2020年にかけて実証実験が実施され、さらに2020年から1年4カ月にわたって行われた、量産運用を想定した「COLMINA現場品質AI 運用管理パッケージ」の開発・実証を経て2022年1月より本格稼働が始まっています。2ラインを使用し、1日約1,500台分のカムシャフトの研削加工を行っている現場を訪れ、その効果について聞きました。
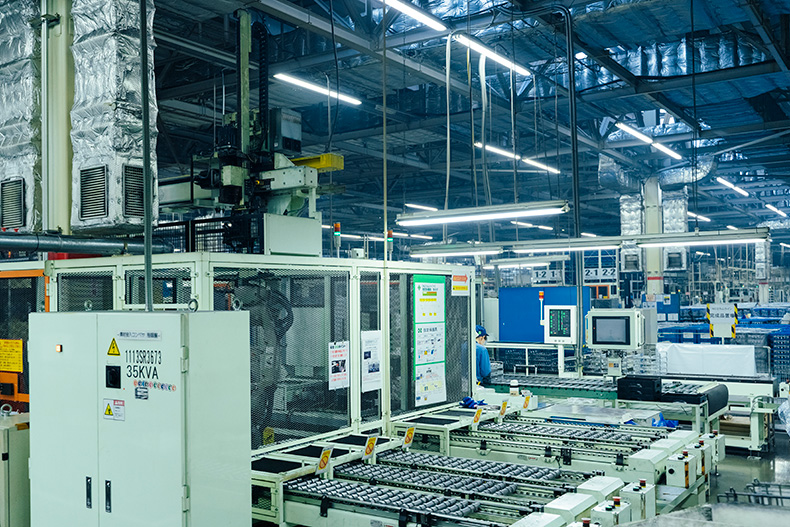
武田: 現場作業者の方々は、このAI技術をどのように受け止められていますか?
大庭氏: これまでは全数の目視検査や抜き取り計測をしていましたが、各種センサーデータを活用することで、現物を測らなくても加工した瞬間に全数の品質を予測できる技術に驚いています。常時確認している予測精度も期待通り。カムシャフトの品質保証はもちろんですが、量産ラインでの本格稼働という実績が得られたこと、そして技術構築までのプロセスを含めて一つのモデルケースができたことに、大きな価値があると実感しています。
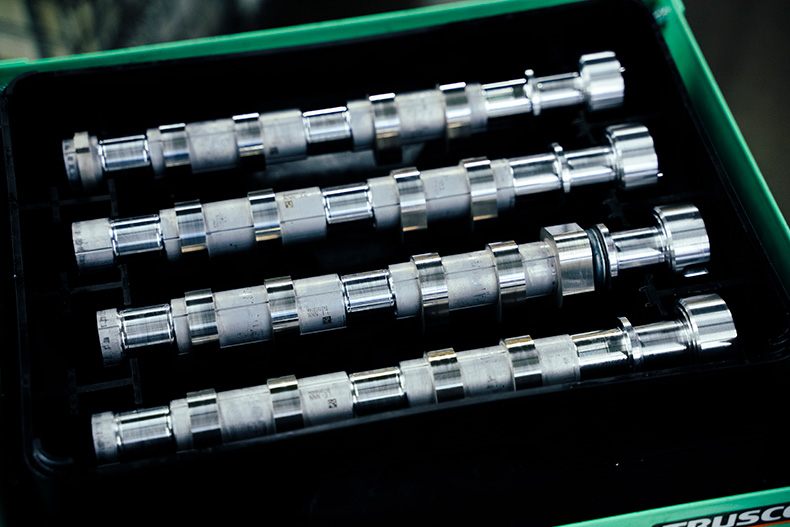
武田: 嬉しいお言葉です。その成果が得られた要因は、どこにあると思われますか?
大庭氏: 開発過程において両社がお互いの領域を学び、毎日議論を進めながら、それぞれのノウハウを融合して推進したことが今回の成果につながりました。今では会社という枠組を超えて、一つのチームだと私は思っています。
「すべての製造業の持続可能なものづくりに貢献する」という思い
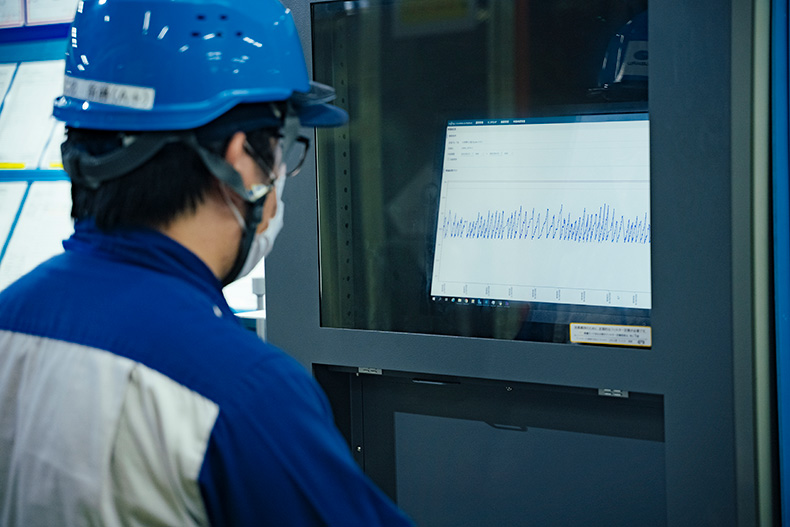
SUBARU社と富士通は、カムシャフトの研削加工にとどまらず、AI技術やIoTを活用したさらなる挑戦を計画しています。その展望はどのようなものでしょうか。
大庭氏: 引き続き、予測精度を確認していきながら2022年度内には目視作業の廃止を目指しています。そして新たな品質保証のモデルラインとしてしっかりつくり込み、ボディ領域など他部品や他工場への横展開を図るとともに、今回のようなDXを企画・推進できる人材を増やしていくことで品質改革を実現していきたいです。製造業全体においても、新しい技術を広めることで日本の技術向上に貢献し、サステナブルなものづくりに寄与していきたいと考えています。
武田: まさに今回の共創は、製造業の技術革新につながる大きな一歩だと思います。今後、富士通にどういったことを期待されていますか?
大庭氏: 今後も様々な最新技術を活用しながら、共にものづくりを変革していきたいと思います。
武田: ぜひやりましょう。では改めて、SUBARU様が目指すものづくりのゴールとは?
大庭氏: 品質の向上にゴールはないと感じていますが、あえて言えばお客様に品質でSUBARUを選んでもらえる。エンジニアとしてその高みを目指します。
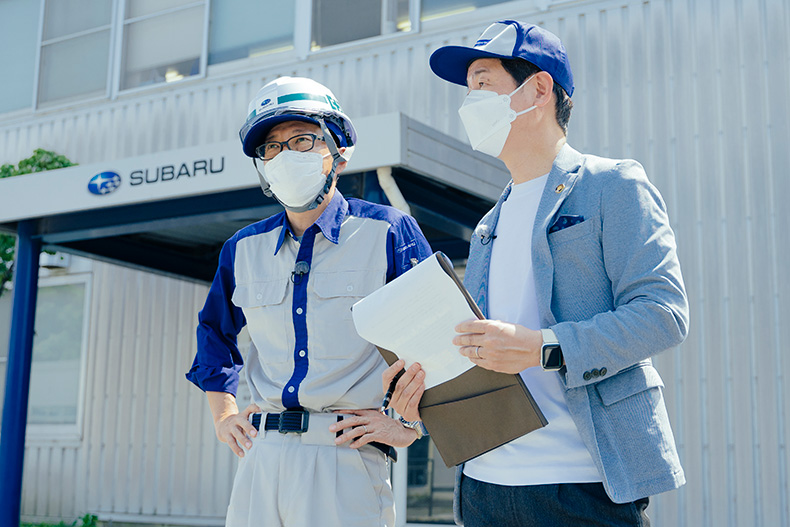
日本の製造業に寄与する――。その思いは富士通も同じです。
武田: 今回の高精度AIモデルは、どのような貢献をしたと思われますか?
塩田: 不良品を出さないものづくりの仕組みと、それらを現場で管理運用するサービスを構築したことでSUBARU様が目指す品質向上に貢献できたと思います。これらの仕組みを広く使っていただくことで自動車製造品質をさらに向上させて、最終的には自動車事故ゼロに貢献していきたいです。
最後に、今回のプロジェクトをはじめ、ものづくりの領域における持続可能なAI活用の仕組みづくりと商品開発に深く携わる、富士通ものづくりソリューション事業部の山本淳史に話を聞きました。
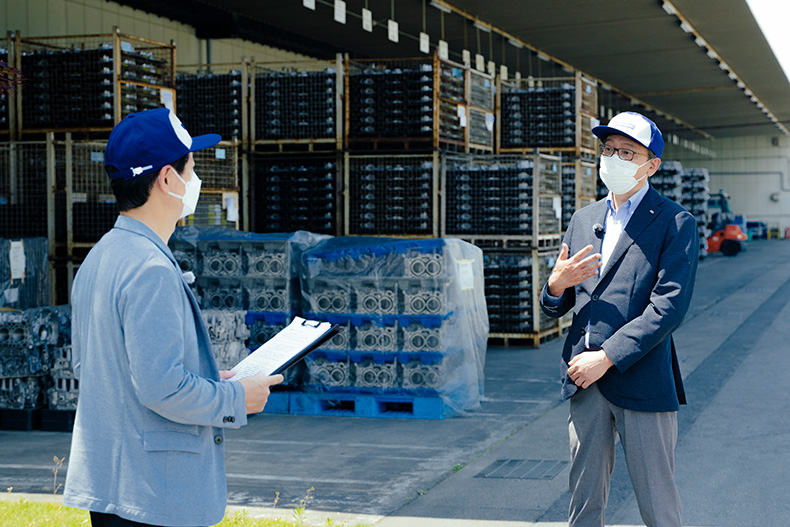
山本淳史
武田: 山本さんは、どのような思いでこのプロジェクトを推進されましたか?
山本: 私自身のパーパスは「製造現場に遍くデジタル技術を届け、日本のものづくりをより強靱にする」こと。私たち製品開発者の思いは、すべての製造業の課題を解決していくことです。日本の製造業の頂点に位置する自動車産業、その中でも独自の車づくりと品質に強いこだわりをもたれているSUBARU様との共創プロジェクトに長年携わってきた中で、この思いはより強くなりました。
武田: その中で商品化した今回のAIモデルとCOLMINAをはじめ、製造業における富士通のデジタル技術の展望を教えてください。
山本: 新しい高精度なAIモデルの開発がゴールではありません。重要なのは、それらを製造現場に導入し、運用維持までサポートさせていただいて、お客様の持続的な活用領域を拡大していただくこと。それによって富士通が重点領域として取り組んでいるSustainable Manufacturingにつながっていくと考えています。持続的なAI活用によって、DX人材不足の解消だけでなく、これまで人が実施していた業務の自動化や匠のノウハウの喪失といった課題解決にも貢献できます。
私たちは、すべての製造業の課題を解決する支援をしていくために、さらに魅力的な商品開発に取り組んでいきたいと思っています。
武田: 今回、自動車業界でデジタル改革を推進する最前線を取材して、単にITベンダーが「製品を提供する」、メーカーが「それを適用する」という関係ではなく、お互いがパーパスを共有して、共にゴールを目指すことが大切だと改めて実感しました。ありがとうございました。
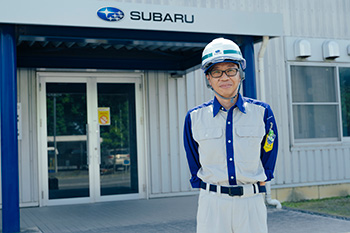
電動車両生産技術部
DX主査兼生産技術統括部 DX企画主査
大庭卓氏
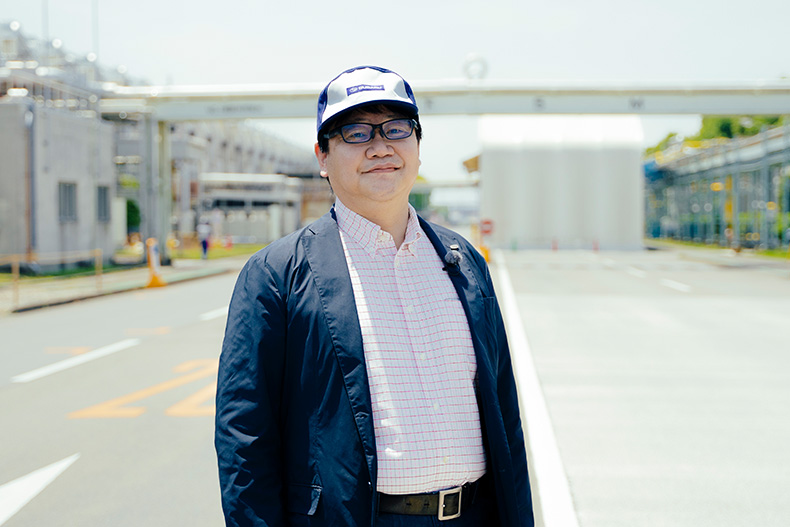
ものづくりソリューション事業部 シニアマネージャー
塩田学
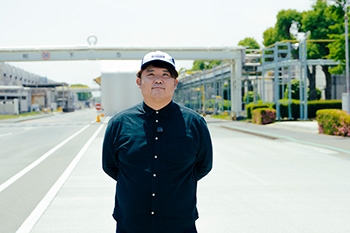
ものづくりソリューション事業部 マネージャー
石脇健太
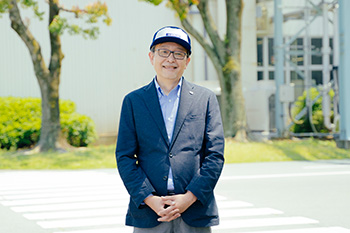
ものづくりソリューション事業部
山本淳史

エバンジェリスト
武田幸治